Need Help Casting Silicon brains for medical student teaching
I need help from the experts here on creating totally encapsulated brains out of silicone. I have a 5 gallon kit of Dragon Skin 10 medium from Smooth-On to make the 25 casts, but the difficult aspect so far is making a mold that can be reused over and over to have the detail needed for teaching medical students about the brain and its features without needing to use and/or destroy cadaver brains from human donors.
Here is a link to my Molding history with various medical molds.
https://youtu.be/TONrFV0AGTY
The biggest problem I have is that because the fissures of the brain are so thin, the silicone gets trapped and then tears. I have tried using straight vaseline, but then the vessel details are lost. Also I have tried creating a smooth cast 310 brain and filling in the fissures with clay. but now am faced with the brain needing to be a multi part mold or to cut the brain int 3 parts and then mold them as 2 part molds and then cast them out of silicon and then glue them back together hoping that they all mate back the same way.
Please advise, thanks!
Rick
Here is a link to my Molding history with various medical molds.
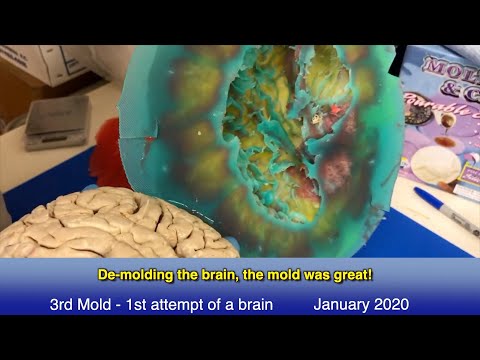
The biggest problem I have is that because the fissures of the brain are so thin, the silicone gets trapped and then tears. I have tried using straight vaseline, but then the vessel details are lost. Also I have tried creating a smooth cast 310 brain and filling in the fissures with clay. but now am faced with the brain needing to be a multi part mold or to cut the brain int 3 parts and then mold them as 2 part molds and then cast them out of silicon and then glue them back together hoping that they all mate back the same way.
Please advise, thanks!
Rick
Post edited by Rick Melges on
0
Comments
With that said, I could only imagine pouring a resin mold that would become far harder than silicone and attempt to gently and slowly remove you valuable original from it. This harder cast would allow you to keep your detailed but thin edges when casting the final duplicates in a softer material to be removed in a similar way. You are correct in thinking this would create the need for a split mold but I don't see how the softer mold will produce this with major shifting of the thinner parts. I could not vouch for the level of detail that could be achieved or the possible chemical interactions that might be adverse when using resin on a wet organic surface, it not curing at all would be a possibility (likely different results per brand). The temperatures needed for resin molding changes across product lines and may create quite a barrier to successful casting. That would take far more experience than I have.
I would have suggested creating an initial shell and then silicone casting over that but you have already described your need for vein detail and that would likely be lost. All in all, feather edges in silicone molds will not cast as needed.
That said, those thin details between the folds will be the biggest challenge, as they will be the first part to wear out. After the resin mold is cast you could go in and trim some of the protrusions down so they will not be quite as deep, which would help with mold longevity, but the castings would not have the same deep crevasses as the original subject.
You can also save your first successful casting from the mold as a master, so when you have to eventually re-make the mold you can do so based on the casting, rather than a new brain.
/Chris
Chris, I have a Gallon Kit of Smooth-on 45D Semi-Rigid Resin. The problem with this resin it reacts with any kind of moisture. For this reason I cant make a 45D Mold of the brain itself it is too moist.
My thoughts here were to make a Hard resin cast with the featheredged fissures covered over with Sculpltex medium clay. and sculpt away any mold lock areas, then make my 25 silicone casts from that mold. But the Brain is oddly shaped and hard to avoid mold lock. It's like 3 water balloons flowers tied together at the knots, you cant make a clean 2 part mold, nor even a 3part mold.
I was thinking that maybe take my Hard cast Brain and cutting the 3 sections apart. then slicing it through an appropriate center line. Then casting each half against a hard surface like plexiglass. the halves could be glued back together using silicone and once all six parts are made int 3 parts to silicone glue those 3 parts back. This is a long and drawn out process for accuracy that could also fail miserably.
My Fall back I idea is to fill up the gaps between the hemispheres, and cerebellum and have a centimeter gap so they know there was a gap. (LOL) Then make a 2 part Smooth-On 45D semi rigid cast and then make my 25 Smoot-on Dragon Skin 10 NV silicone casts with a hard mother mold and cradle with the brain stem as the pour entry and multiple ports for vents this will be the brain upside down.
What do you think?
Since that first silicone casting is just used for making rigid molds, you can also use a more durable silicone for it.
Otherwise, your idea of filling the gaps slightly would be ideal. You could possibly even do a combination of both solutions.
/Chris
What do you think?
Even with a spray, it would be difficult to get down into the recesses to insure no moisture inhibits the resin. That's why I would start with a silicone mold, produce a durable silicone master casting, then make a resin mold off the master casting. Then you can run as many castings as you like, and when the mold wears out you can just remold the master casting.
/Chris
If you watched my Video you can see that I failed miserably 5 times making a Silicone cast of a silicone mold even using really stretchy materials and platinum silicone.
"Even with a spray, it would be difficult to get down into the recesses to insure no moisture inhibits the resin."
I had not planned to use the deep fissures because they have been soo problematic in getting the cast out of the moold without tearing the mold. I was hoping that several coats of the New skin spray with several coats of crystal clear would fill fill in those fissures and alleviate the the moisture problems.
But yes Testing would be the Ideal thing to do next on a small section.
what do you think?
As I mentioned before, you could start with a silicone mold of the brain, followed by casting a silicone brain (master), which would destroy the mold due to tearing, but you would get one good master casting. That casting could then be used to make the resin mold, which should be durable enough to get a good number of castings. When that mold wears out, you could create a new version off the master silicone brain.
That's just how I might approach it, but there are endless options out there!
Your barrier spray ideas could work, I would test them on a small piece or find a similar analog if that is the route you want to go.
/Chris