Great White alternate materials???
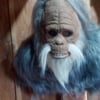
in General
If ya'll remember a few months ago i did a sculpting of a Great White shark head..i did a test casting in resin and it came out malformed and misaligned..backed it with foam and its quite heavy....wondering for a wallmount to sell if maybe i should do it in urethane rubber or silicone with foam backing??? KONG came out pretty well as a urethan rubber/foam backed piece...but a little nervous to try it with a piece like this that has a bit of a "hangout/ hangover"
Did a test paintup to see how it might look...i am motivated enough to correct the defects and try remolding it as a one piece to eliminate the seams...
want to maybe get a more "professional" opinion..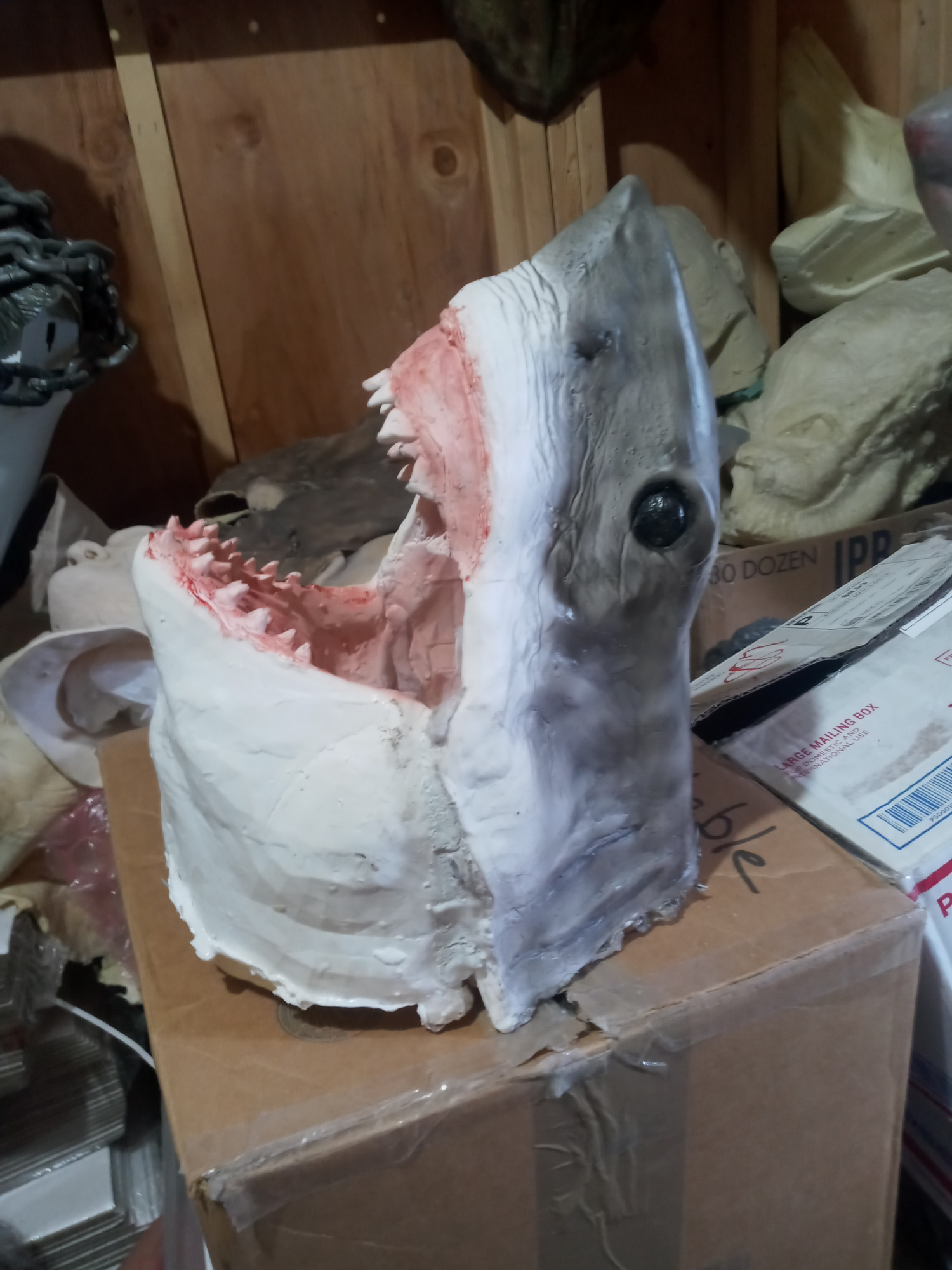
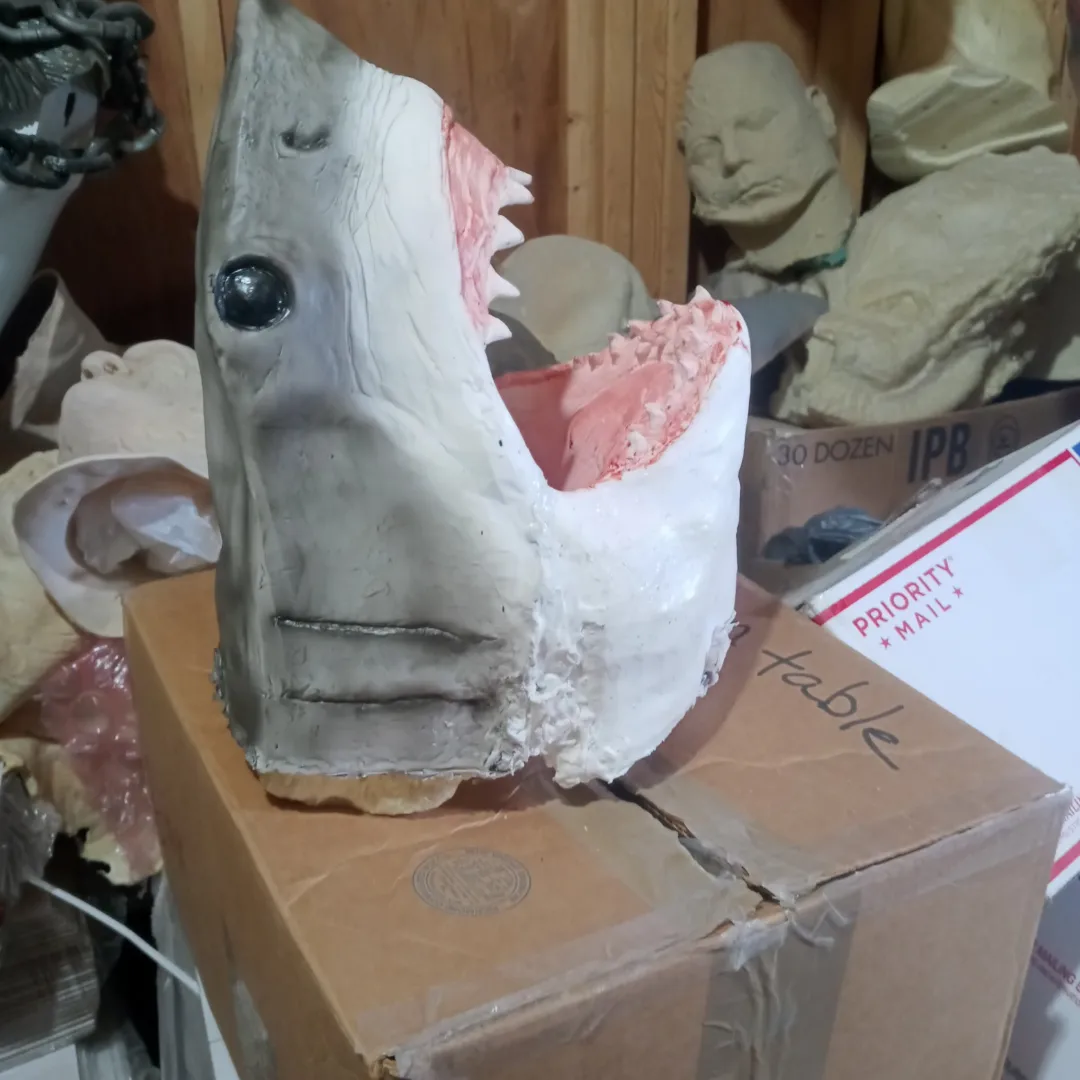
Did a test paintup to see how it might look...i am motivated enough to correct the defects and try remolding it as a one piece to eliminate the seams...
want to maybe get a more "professional" opinion..
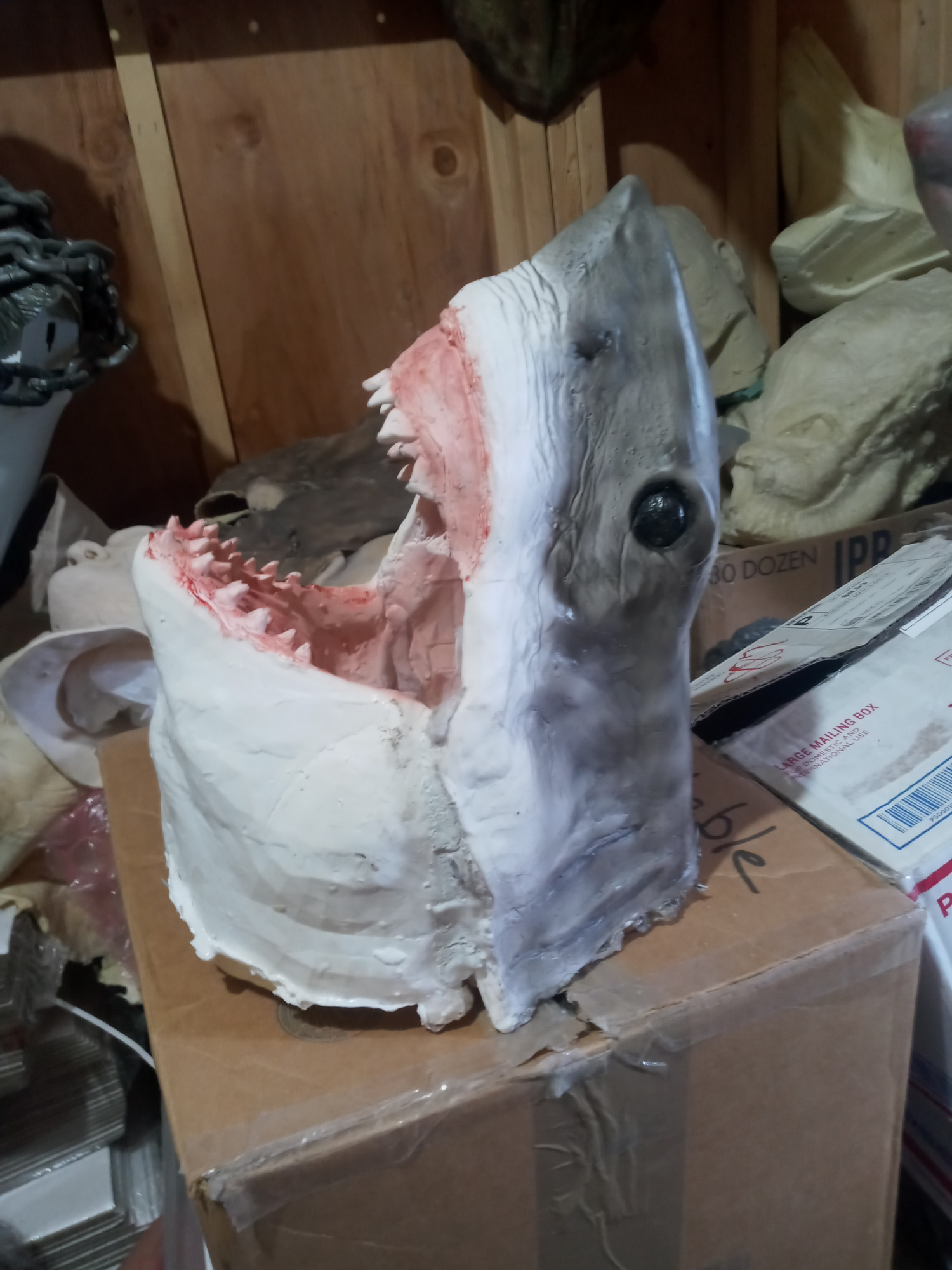
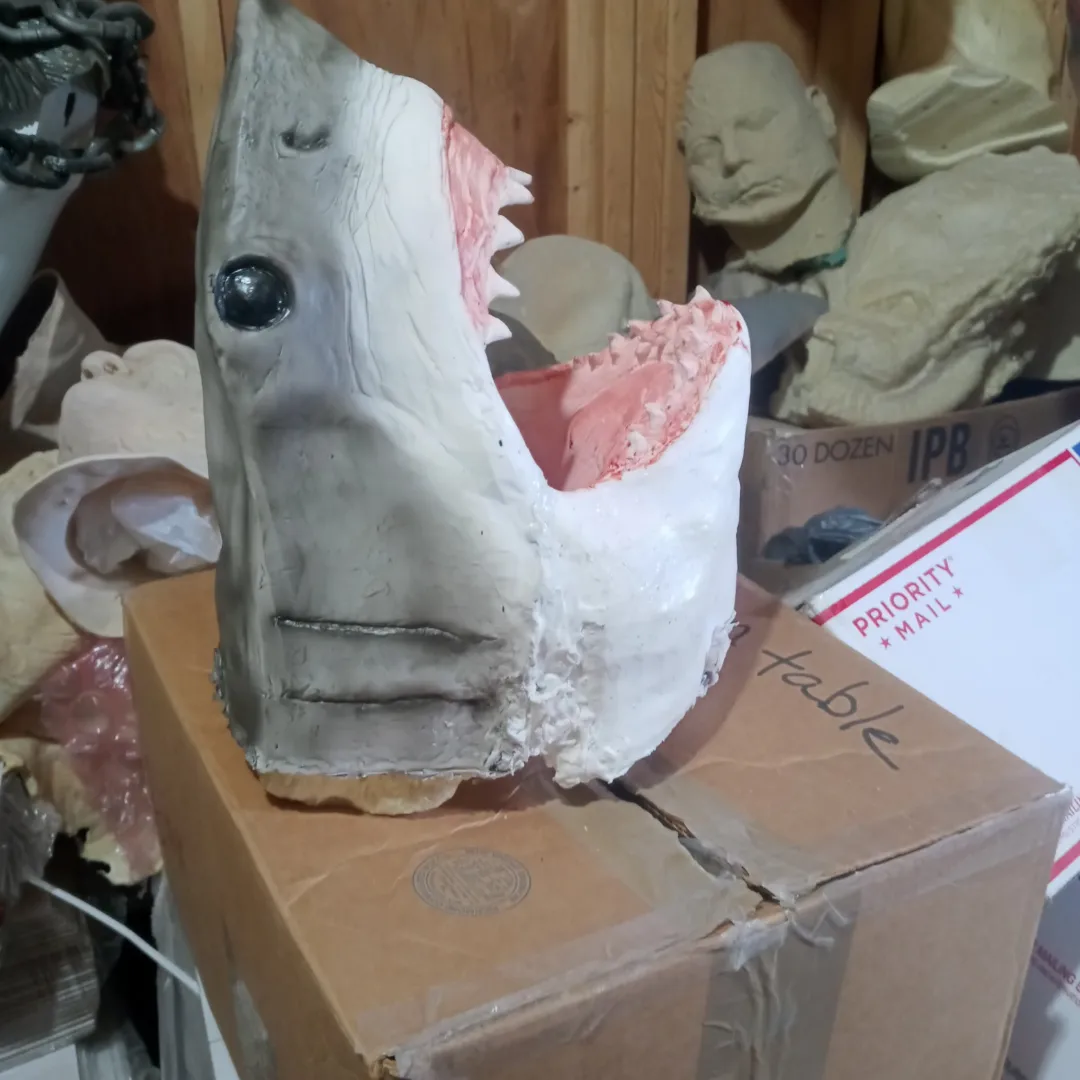
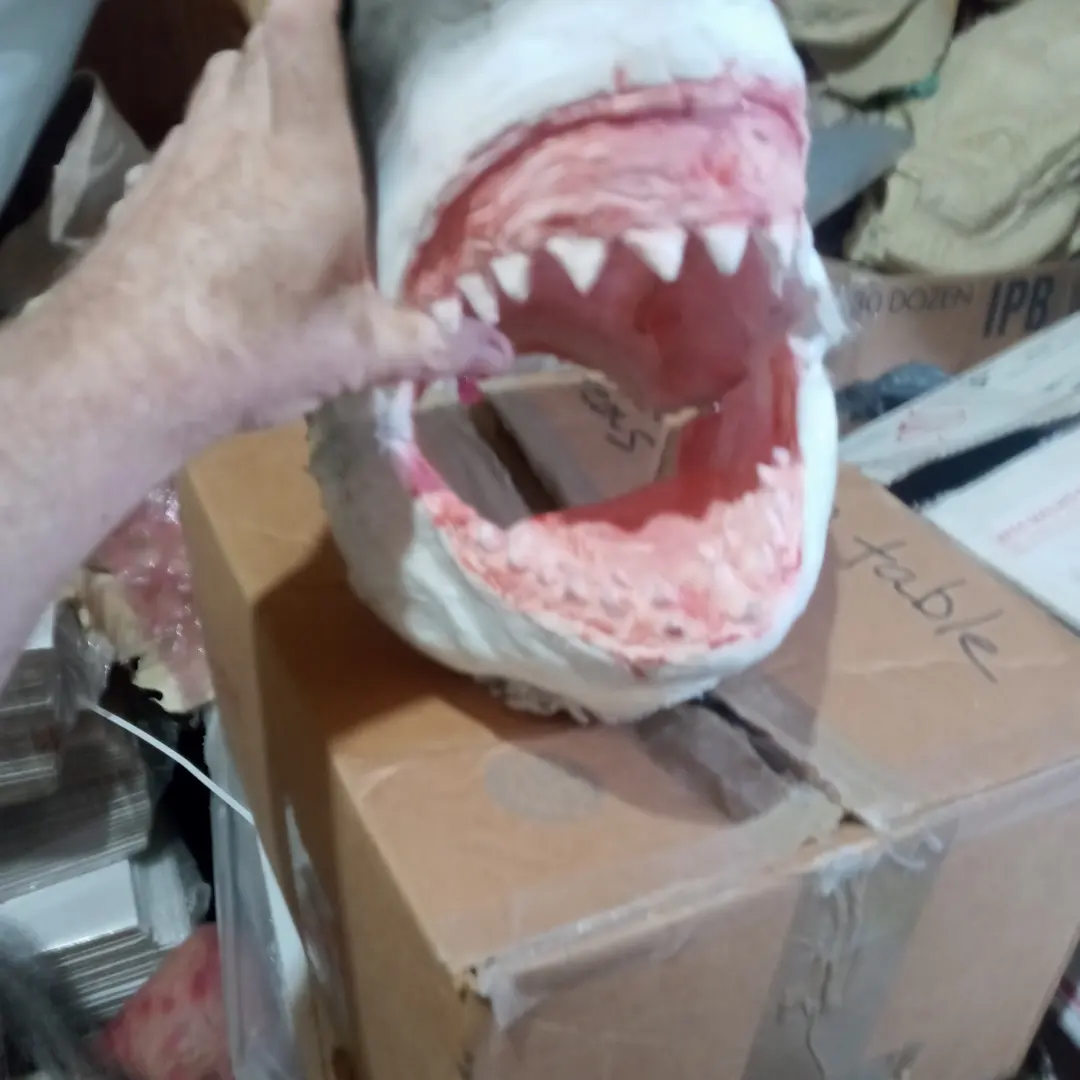
1
Comments
Rotocasting would be a possible option to keep weight down. You would mix up small batches of resin and rotate the mold around to build up thin layers, leaving a hollow form that can then be backfilled with foam, or even strengthened with more resin and fiberglass.
The paint job looks awesome!
/Chris
The top of the head was "sunken in" in the middle and one of the sides was concaved in..the teeth themselves did not come out as well as i wanted them to..a bit blocky instead of like the normal way a sharks tooth would look..(as i sculpted it)
I had thought maybe moving forward with making wallhangers of this shark and the dinosaurs...i might try to make an outside skin for more "realism" doing it in a ureathane rubber since they were going to be static pieces.
Someone also gave me an idea of doing a urethane skin backed by a resin shell and filled with foam...not sure if that in itself would be a good idea ( how well would the ureathane adhere to the resin?) Made me think it was kind of a little too much work
Another, slightly more outside-the-box option would be to do the same resin skin step as above, then pack the mold with sand, or even dry rice, (if your mold design would allow it). Then after the skin cures, you could pour out the sand and add more layers as desired. This would let you keep it hollow rather than the foam option, and also would allow for fiberglass backing.
I'm sure there are other good options too, those are just the first that come to mind.
/Chris