Options
Molding a full size bust
Hi Folks,
I'm working on my first larger (full scale) scale sculpture and have so far only ever made molds for something much smaller, and generally just a box mold. I've had a look around at tutorials, so I have a broad understanding of the techniques, but I'm hoping for some more specific guidance here if possible. I'm assuming I should be brushing on the silicone and making a shell.
Any advice would be greatly appreciated. Cheers!
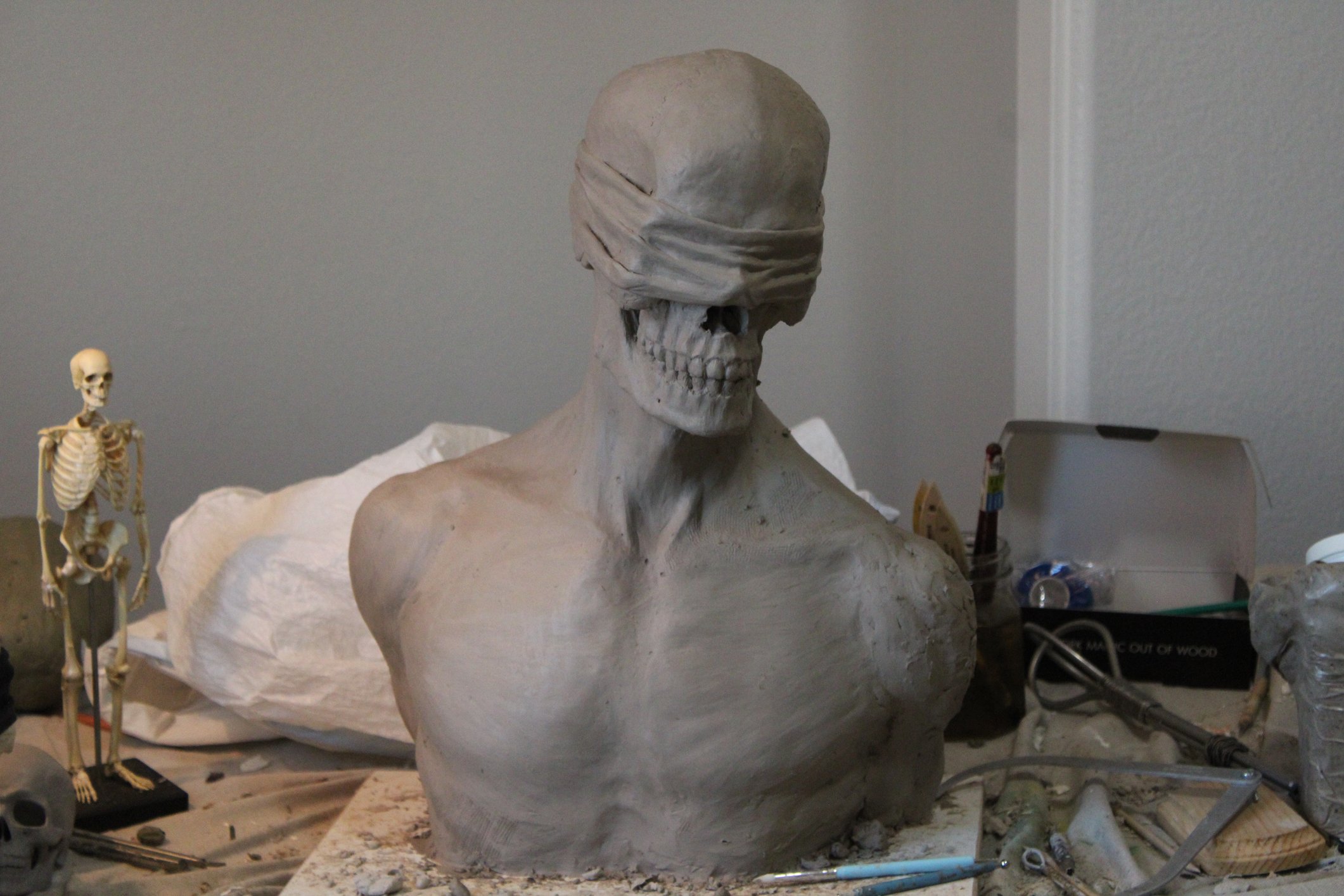
I'm working on my first larger (full scale) scale sculpture and have so far only ever made molds for something much smaller, and generally just a box mold. I've had a look around at tutorials, so I have a broad understanding of the techniques, but I'm hoping for some more specific guidance here if possible. I'm assuming I should be brushing on the silicone and making a shell.
Any advice would be greatly appreciated. Cheers!
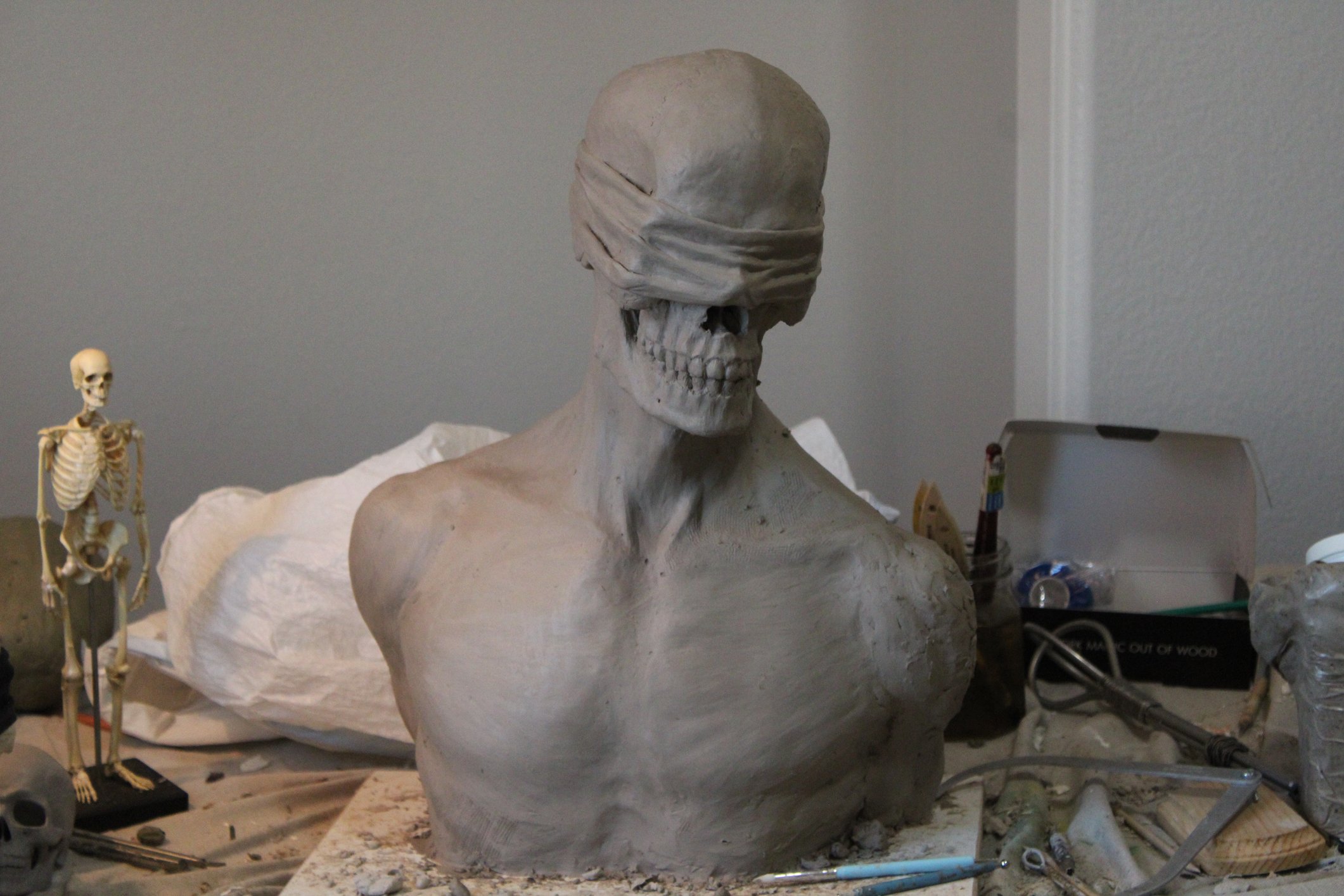
0
Comments
The basic method would be to determine your case line, which would most likely be across the tops of the shoulders and over the crown of the head, and then clay up a wall along the back half of the sculpture (or use shims) to mask off half the sculpt. Then you would add keys, mix up a thickened batch of silicone to fill in deep areas and undercuts to simplify the form, then brush on a few layers of silicone over that. Then you would lay up your mother mold on top of that, remove your mold wall or shims, and do the same process on the second half making sure to add release so the silicone and mother mold of the first half do not bond to the second.
That is just a brief overview of the process skipping a lot of details and steps. I suggest watching some of our lessons that feature mold making to learn about the finer points like keys, pry points, bleeders/vents, setting up a solid rim, etc.
/Chris
What are the benefits of making the silicone in two parts rather than doing it as one piece, with the parting line raised up to a wall then cut with a mold knife, like in the image below.
The clay wall part sounds the most intimidating, especially since the sculpture is in WED.
The more advanced mold-making techniques often take into account the cost/time further down the line for multiple castings. Sometimes budget, time, or other resources can dictate a simpler method like the example you provided.
/Chris
Although I have no grand plans for how many to create, as a learning experience I think I will go for what you've suggested and try a two part mold.
I've got a premiere subscription so I'll look around. It seems like I'll need to gather the methods from a few videos.
One I can see that matches is "How to make a latex rubber mask" by Timothy Martin. He's making a stone mold for latex, but it's a similar size and it looks like the method for how he sets up a wall is relevant to what I'm doing.
A question I have in regards to that is the keys he makes are those big angular wedges. Are those the types more suitable for when it's going to be a stone mold? The ones I've seen for silicone seem to be either circular impressions, or long tracks that go all the way around. The larger ice cube shaped ones on the outside of the silicone mold to allow the plaster mother mold to lock in. Is that right?
/Chris
One last question: What's the best way to seal the WED clay for making a silicone mold? I'm going to go with the same "white clay" Timothy used in his videos for the wall, and I'm assuming I want the WED sealed in some way to avoid that joining.
/Chris
My question now is related to the surface of the mold, and whether I need to work to smooth things out for the plasti paste shell? I'm thinking I need to build up more of a ridge for the seam where I'll be making the cut (got a mold knife that will create the key as it cuts).
I painted on those raised sections running perpendicular to the main seam to work as keys for the mold jacket. I'm thinking I need to make the seam larger.
Any tips of where tyo go from here would be greatly appreciated.
It's really messy, but I'm not sure how much that matters. The plan is to build a clay wall tomorrow to make the shell. One piece for the back then two pieces for the front.
What may help is mixing small batches of thickened silicone and troweling it on to fill the deeper areas and even things out. A lot of the roughness can happen as the silicone starts to set up. After a certain point, you have to stop working the silicone or it will not smooth back out again.
I would suggest shaving off any of the rough edges or bumps with a razor or sharp knife first, then trowling on the small batches to even things out. Same for the keys, you may be able to shave those into smooth shapes so they can work properly.
It's all a process, and the learning never stops! Keep at it, and I look forward to seeing how everything goes!
/Chris
The mold knife is great from trimming down the excess, so I can shape out the seams and keys into cleaner forms, then trowel on thickened silicone.
I wonder if I could use foil, seran wrap or soemthing to help create an average of the surface for the plaster to form to
You can totally save this, but it will take patience and a good amount of effort. First I would shave and trim everything down as much as possible, then I would go in small sections with small batches of silicone. For example, starting on one half (or smaller) of the front side of the face, then the other half, then do the same for the back of the head. The goal is a smooth, almost machined look with no pockets or air bubbles between layers, no undercuts that would cause your mother mold to lock onto it, and clean keys that align the same way every time and can socket into the mother mold firmly.
You got this!
/Chris
You're in the home stretch!
/Chris
/Chris