Do you incorporate 3D modeling and 3D printing in your work?
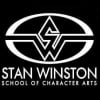
With the cost of 3D printers at an all-time low, and so many great options for CAD and 3D modeling software like On-Shape, Fusion 360, FreeCAD, Tinkercad, Blender, etc. it's never been easier to incorporate rapid prototyping into a project.
Our latest course series "Modern Miniature Effects" features the use of 3D models and 3D printing to help create a miniature cargo ship and a monster octopus. Check out part one and part two!
/Chris
Do you use 3D modeling or CAD, and if so, which software do you prefer?
Do you have your own 3D printer, or do use use a printing service or maker space?
Our latest course series "Modern Miniature Effects" features the use of 3D models and 3D printing to help create a miniature cargo ship and a monster octopus. Check out part one and part two!
/Chris
1
Comments
I've been using Blender for over a decade now - I'm a little obsessed - and use it for just so many things. Loading references (like game models), modelling mechanics, digital sculpting, rendering, and even video editing - sometimes some environment design too. When it comes to modelling mechanical parts, it isn't as good as CAD software (there are CAD plugins for Blender), though I continue to use Blender as that way my workflow sits primarily in one program, which thanks to its large community, is constantly improving.
I started off with a Creality CR10s printer, which was great to learn about the intricacies of FDM 3D printing. I now own a Bambu P1P, which is a lot more reliable, though I'm glad I had the learning experiences with my first printer. Would love to get my grubby mits on a resin printer (to print in high detail my sculpts and more durable mechanics), but alas I don't have space I can dedicate to one.
I still very much appreciate and respect the more traditional fabrication process and try to pick them up where I can, although I have more peace of mind working with what digital technology allows me to do, such as undo's and creating backups of projects.
The majority of the work I do is on full scale Big Daddies from BioShock. When we create them, my friend and work partner creates the model for us based on the original in-game design. This ensures that every original detail from the game is captured. It also ensures that we are able to scale all pieces proportionately.
Because of the size of these monsters, I have 3 large format FDM printers in my shop, along with 4 medium sized resin based printers for the detail pieces (visors, tube connectors, rivets, port holes, etc.). I try to get these things printed quickly, otherwise I don’t think we’d be able to do them very fast at all, so I do use CraftCloud for when I want a really REALLY big piece done and quicker than I would do it.