Questions About Latex (Sealing Clay and Adhesion)
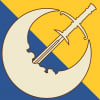
in Lab work
Hiya folks! I'm finally gonna dip into learning latex skinning techniques - I've put it off for too long since I don't really have the workspace for the mess, but somehow, I'll make it work.
I've watched a few courses here on molding/casting latex so I've got some idea of what I'm doing - I'll learn more as I make mistakes - but I'm wanting some extra help before I get started.
Firstly, from what I remember, people seal their clays before making the plaster molds, to protect the surface of the clay and make it easier to demold later. I've got a tub of Monster Clay I was hoping to use to sculpt the creature, but I don't want to have to throw that clay out if I have to add contaminants to it. Is there a way to create the mold without sealing it? The mold wall for the flange is also a concern. If it is best to seal it, what's a decent sculpting clay that isn't too painful on the budget, that I could toss out afterwards?
If for some reason I need to glue latex to itself, does it adhere to itself (with some fresh latex as a glue) or will I need an adhesive like Pros-Aide? And if I needed to glue the latex to plastic (such as PETG or PLA), is Pros-Aide good for that too?
I've watched a few courses here on molding/casting latex so I've got some idea of what I'm doing - I'll learn more as I make mistakes - but I'm wanting some extra help before I get started.
Firstly, from what I remember, people seal their clays before making the plaster molds, to protect the surface of the clay and make it easier to demold later. I've got a tub of Monster Clay I was hoping to use to sculpt the creature, but I don't want to have to throw that clay out if I have to add contaminants to it. Is there a way to create the mold without sealing it? The mold wall for the flange is also a concern. If it is best to seal it, what's a decent sculpting clay that isn't too painful on the budget, that I could toss out afterwards?
If for some reason I need to glue latex to itself, does it adhere to itself (with some fresh latex as a glue) or will I need an adhesive like Pros-Aide? And if I needed to glue the latex to plastic (such as PETG or PLA), is Pros-Aide good for that too?
0
Comments
The while the furniture polish may not exactly be a sealant, it's still a foreign material to the clay that I worry will mean the clay will be useless afterwards. Do you just throw out the clay afterwards? If so, what clay do you use?
stir..and pour back into the container
@James Shaver When you're adding the mold wall to the sculpt to make the flange, how do you prevent the clay from sticking to the sculpt and messing up the details?
@Troy Mccombs So the additives (furniture polish) mixed into the clay now don't mess up the clay at all, and you can keep reusing it?
Sorry guys if I'm re-iterating some stuff, I just want to make sure I'm on the same page as you before getting into all of this. I really appreciate the advice!
Wet clay (for wall) doesn't really stick to oil clay very well. I've never had a problem getting it apart from the sculpture. And no, furniture polish won't hurt the monster clay. You can reuse it forever. The furniture polish breaks the surface tension of the clay so that the plaster top coat doesn't bead off when you're brushing it on
Also, when you melt the clay and mix it all back up after you are done with a sculpt, any surface coating makes up such a small percent of the total volume that it does not really impact the quality of the clay in any meaningful way.
/Chris
I've got some Rustoleum clear coats, so I'll be able to use that when I'm ready to cast. Unfortunately, I don't seem to be able to find any water based clays easily available - I can get WED clay from Barnes, where I'll be getting my other plaster/latex supplies from, but I worry that it's a fair amount of money to spend on something I only need a little of, and aside from that I don't have room to store that amount of clay, I worry it may dry out before I get to use it again.
So, I wonder - what about air dry clays, like this? Or even Play-doh? I was thinking foam clay, but that wouldn't sculpt well enough to produce a nice flat seam line.
Edit: Reading in a couple of places that Play-doh contains Aluminium Sulfate, so that would be a no-go to avoid contaminating the clay I would want to use with silicone in the future. Perhaps Sculpey clay, or Chavant?