Options
Brainstorming on fabricating optically clear hollow objects
All right guys, time for a new installment in Project: Inadvisable Uses of LEDs. I'm working on this cosplay for international competition qualifiers this fall, and I'm currently trying to figure out the light bulbs. I've identified and started prototyping seven (!) possible methods, and I'd like to pick your brains to see if you can think of others.
References:
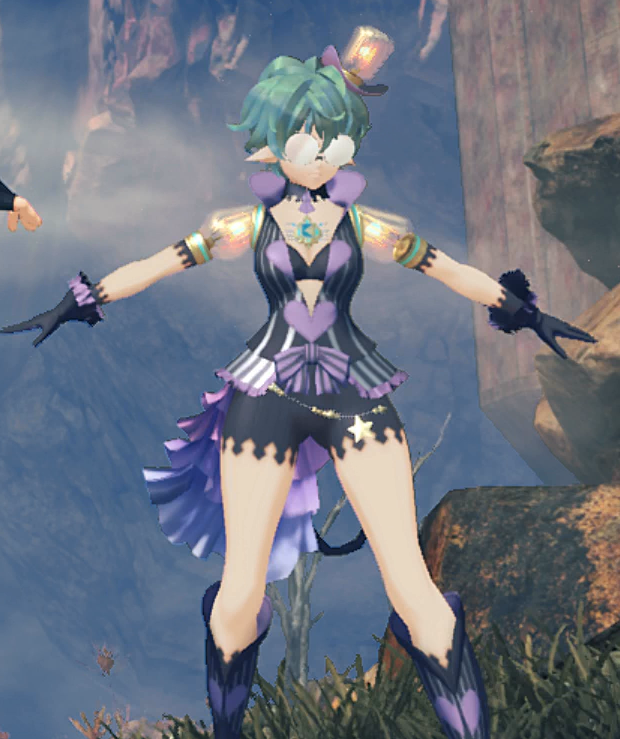
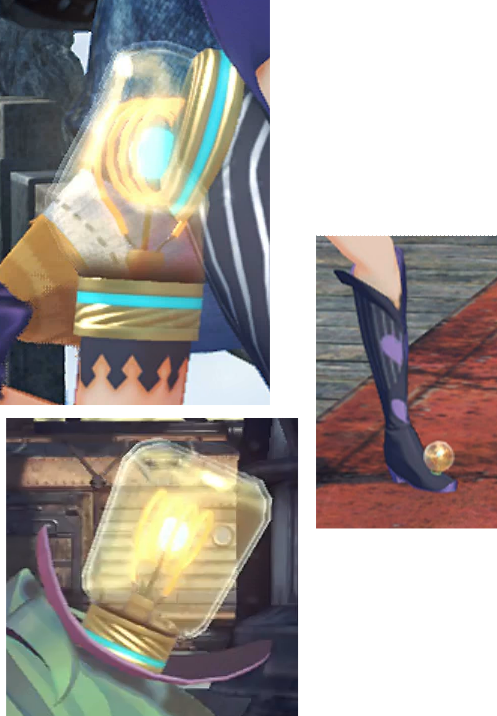
The important thing for this is that I want them to be seamless. They don't have to be perfectly optically clear or consistent thickness, but they need to be close (I can live with a bit of uneven thickness, translucence, or bubbles for artistic reasons). I need to fit things inside of them, and weight is a significant concern, so they need to be hollow.
I'd also like to fabricate them in a way that allows me to have plenty of spares. I have access to most tools I could need (yay makerspaces!)These are the options I have explored.
Resin casting
I've successfully made a silicone glove mold of the outside of the smallest bulb, with plaster bandage mother mold, so that's one problem solved. I use mostly polyurethane resin (I love Innovative Polymers products. Absolutely indestructible, enormous variety, and the best customer service I've ever seen), but I'm open to other materials.Casting in a two part (?) mold
Probably my best shot at even thickness, but I'd have to do some tricky bits with the core. My current best idea is to additionally make a glove mold of the inside of the bulb and backfill it with a flexible foam, so that it's stable while casting and can be squished to remove it from the final part. Not entirely sure how I'd handle registration with the exterior glove mold, but that should be a solvable problem.
Rotocasting in a glove mold
Structurally plausible (I've tried and succeeded), but the translucent rotocasting resin I'm using is not as clear. Optically clear rotocasting resins don't seem to be a thing (which isn't surprising; they're fairly temperamental even for regular casting.) There are some shenanigans I plan to try with the optically clear resins, involving additives and temperature, but they're kind of a yolo thing with a low probability of success.
3D Printing
FDM printing in clear filament
I'd need to do considerable finish work to remove layer lines, which is possible, but could be difficult to achieve on the inside of the bulbs. I'd also need to avoid supports for optimal clarity, which means that some of the flatter spots just don't print in vase mode. I tried 

SLA printing in clear resin
Likely to achieve the look I want, but print size is limited (the shoulder bulbs flat out won't fit at all unless I break them down into at least three pieces). That said, SLA resin is the easiest material on the list to join seamlessly after printing, if necessary. On the other side, it'll take ages and be difficult to easily produce copies.Thermoforming
Injection blow molding into a glove mold
Quite possible, but I'm still trying to figure out temperatures and the best way to attach my air compressor to the PETG bottle pre-forms. I'm running another few tests today. If this works, it will be perfectly transparent and very fast. See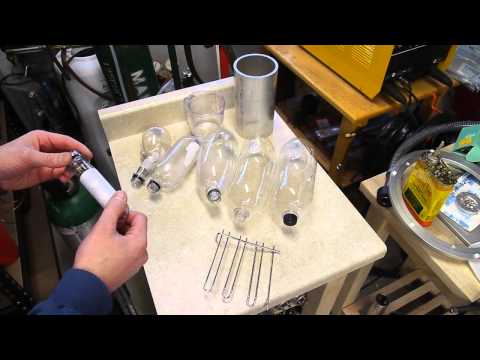
Vacuum forming
Given the undercuts and height, I likely wouldn't be able to form these in one piece, which would leave me with a seam. I don't think there are any materials that are easy to thermoform that could be joined seamlessly.Fabrication
Machining from a clear material - Lolnope I am not even gonna go there. I mean it's probably possible to use a giant chunk of acrylic on a lathe, but it's impractical for so many reasons.0
Comments
/Chris