Best Of
Handmade Maleficent Costume
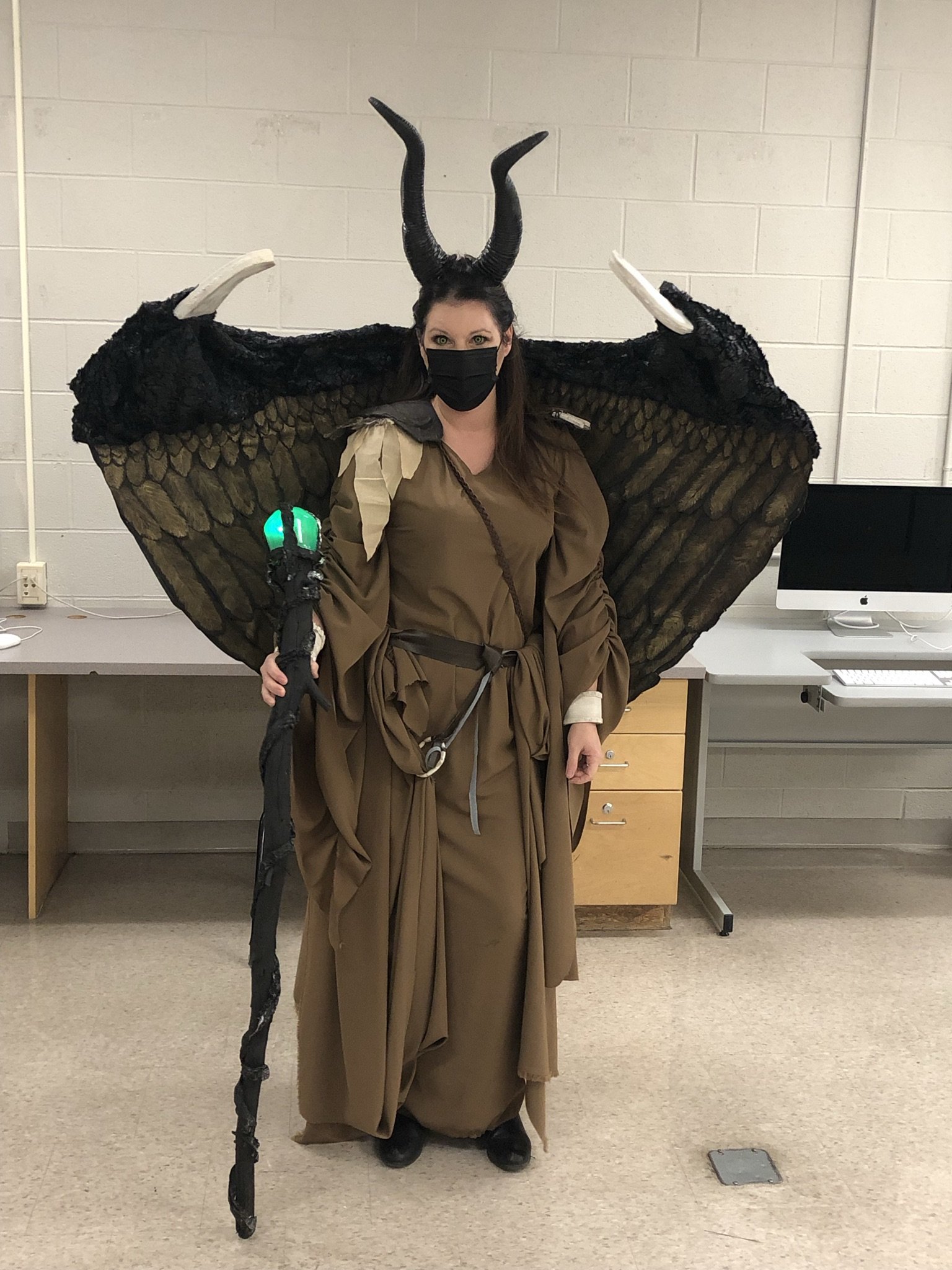
I made the wings, dress, skirt, staff, jewelry, belts, and modified the horns that came as a skullcap into a headband
Re: Rex the Dragon
Thank you! Yeah, all in is about 60 lbs. most of that being the mechanics, electronics, and fire extinguisher. It was a lot of fun making, but now is just as much fun interacting with the public. Sooo many different and memorable reactions !!
Re: Creation of puppets, about latex and hands
Baby powder is usually a good idea on latex as it removes the tack so it does not stick to its self. You can also rinse it off later to remove the excess which should let you paint on the surface without issue. That said, there's less to worry about if you paint it first.
To make the hands more menacing you could elongate the fingers or add long nails/claws as you suggested, as long as they fit your character. Sometimes simply making the fingers longer is enough. Just don't make them too long or it look comical or distracting.
I'm not sure where you could find those stickers in Europe, but you could find some images online (or design your own) then have them printed locally or get sticker paper for your own printer if you have one.
Your characters are off to a good start!
/Chris
To make the hands more menacing you could elongate the fingers or add long nails/claws as you suggested, as long as they fit your character. Sometimes simply making the fingers longer is enough. Just don't make them too long or it look comical or distracting.
I'm not sure where you could find those stickers in Europe, but you could find some images online (or design your own) then have them printed locally or get sticker paper for your own printer if you have one.
Your characters are off to a good start!
/Chris
How to Make an Eye Mechanism - Design, 3D Printing & Assembly
I recently finished this course about a month back. I found it incredibly helpful. I've yet to print my mech, but plan to soon. Obviously, it is dated, but nonetheless very useful. I wasn't very versed in 3d design, with the exception of Tinkercad and basic Sketchup. I wanted to take this course to learn how to work in Fusion 360. It definitely helped me get moving in the right direction and It's now an essential part of my workflow. Thanks, SWSCA and Dave!!
Yesterday I watched this
https://www.youtube.com/watch?v=8mmlJdVcJkg
Super cool video. Everyone should check it out...
With how much 3d tech has grown since this course and seeing how heavily the industry now relies on it, will there be (could there be) more SWSCA courses covering 3d printing and the different ways it can benefit the creature making process? I feel like there is a ton of potential content that a lot of this community could enjoy and benefit from.
In the above video featuring the workflow over at Legacy, they turn to 3d scanning, modeling, and printing all throughout their process to make models, molds, maquettes, prototypes, finished parts, accessories, mechanisms, etc... I know that a quick youtube or google search and a little bit of perusing can answer most 3d print enthusiasts' questions, but personally, I would love to learn at the feet (screens) of the masters...but I digress.
Great course as always! Thanks, SWSCA Team!!
Yesterday I watched this
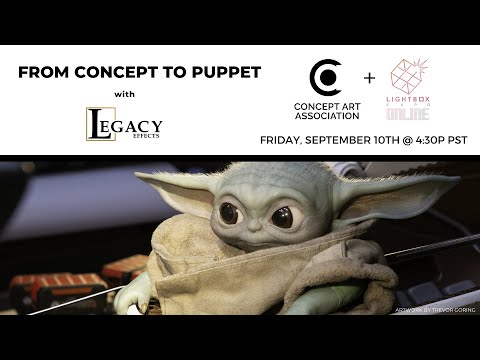
Super cool video. Everyone should check it out...
With how much 3d tech has grown since this course and seeing how heavily the industry now relies on it, will there be (could there be) more SWSCA courses covering 3d printing and the different ways it can benefit the creature making process? I feel like there is a ton of potential content that a lot of this community could enjoy and benefit from.
In the above video featuring the workflow over at Legacy, they turn to 3d scanning, modeling, and printing all throughout their process to make models, molds, maquettes, prototypes, finished parts, accessories, mechanisms, etc... I know that a quick youtube or google search and a little bit of perusing can answer most 3d print enthusiasts' questions, but personally, I would love to learn at the feet (screens) of the masters...but I digress.
Great course as always! Thanks, SWSCA Team!!
Re: How to Make an Eye Mechanism - Design, 3D Printing & Assembly
Hi Justin,
Glad you liked the eye mech lesson. I got a lot out of that one too. As you mentioned things in that space (from software to printing and assembling techniques) have all continued to evolve, so I'm sure we'll be revisiting the world of 3D printing in the future. Especially now that more and more artists are able to have their own 3D printers at home since quality 3D printers have dropped in price significantly. And Fusion 360 has also become a great and widely used application.
When I built the eye mech from this lesson I took a more modular approach to its design since I had access to a newer method of connecting 3D printed components using threaded brass heat-sink inserts. You just design small holes in your part then sink the insets in using a soldering iron with a special tip. This lets you easily bolt components together (Rather than gluing or solvent welding them) so you have strong connections that can easily be taken apart for maintenance, upgrading components, etc.
Here's how mine turned out:
I'll check in with the team and see what our roadmap looks like for 3D printing courses. So much fun stuff out there to learn in so many disciplines.
/Chris
Glad you liked the eye mech lesson. I got a lot out of that one too. As you mentioned things in that space (from software to printing and assembling techniques) have all continued to evolve, so I'm sure we'll be revisiting the world of 3D printing in the future. Especially now that more and more artists are able to have their own 3D printers at home since quality 3D printers have dropped in price significantly. And Fusion 360 has also become a great and widely used application.
When I built the eye mech from this lesson I took a more modular approach to its design since I had access to a newer method of connecting 3D printed components using threaded brass heat-sink inserts. You just design small holes in your part then sink the insets in using a soldering iron with a special tip. This lets you easily bolt components together (Rather than gluing or solvent welding them) so you have strong connections that can easily be taken apart for maintenance, upgrading components, etc.
Here's how mine turned out:
/Chris
Re: Anybody here have experience with the Stan Winston School of Character Arts?
Hands Down Fully Recommend. All of the courses are in-depth and fantastic. Not to mention that Matt and Chris are fantastic about answering any and all questions you may have. I don't know of any other place where regular people like us can get help from the best in the industry at the click of a few buttons. This place is a treasure trove!!
Re: How to Make an Eye Mechanism - Design, 3D Printing & Assembly
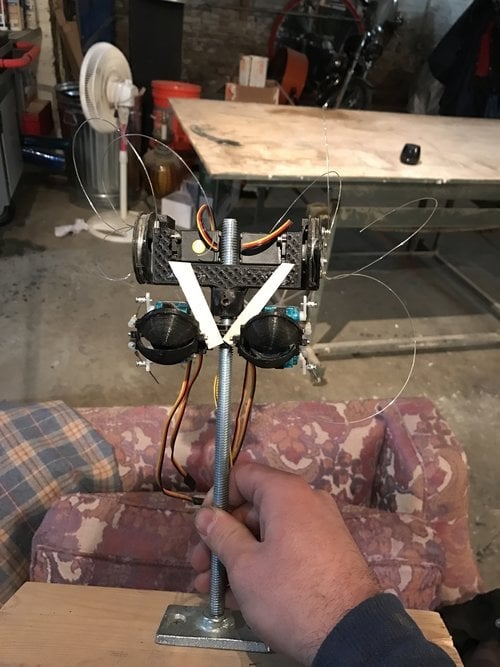
this guy works! I got a radio link at10 controller and have tested each of the motors. I need to channel mix the channels that control the 4 eyelid servos so I can use this in a real scene. I've been going through Gary See's stone mold making tutorial and Craig canon's animatronic head tutorial to build a head to add this eyeball mech into. I sculpted the head on Thursday and Friday and today I build a clay wall - tomorrow I'll finish the mold. I'll post more updates!
Re: Cosplay Lighting Help
Hi Samantha,
One option would be to heave each illuminated wardrobe piece contain a small micro controller (like an Arduino Micro or other small form-factor Arduino comparable micro controller) that has a wireless module like an Xbee.
This would allow you to have all the light sequences of the various wardrobe pieces sync up based on input form a "master" microcontroller.
Something like this requires some basic programming knowledge, but thankfully there are sites like https://www.adafruit.com that not only sell the various components, but also have code libraries that help you tie them together.
Wireless communication is not without its challenges though. Outside interference can cause problems, especially at large events where a lot of other wireless devices are operating.
I would try and use hidden wires where possible, as that could save you a lot of headaches.
/Chris
One option would be to heave each illuminated wardrobe piece contain a small micro controller (like an Arduino Micro or other small form-factor Arduino comparable micro controller) that has a wireless module like an Xbee.
This would allow you to have all the light sequences of the various wardrobe pieces sync up based on input form a "master" microcontroller.
Something like this requires some basic programming knowledge, but thankfully there are sites like https://www.adafruit.com that not only sell the various components, but also have code libraries that help you tie them together.
Wireless communication is not without its challenges though. Outside interference can cause problems, especially at large events where a lot of other wireless devices are operating.
I would try and use hidden wires where possible, as that could save you a lot of headaches.
/Chris