Best Of
Ms. Psychotron
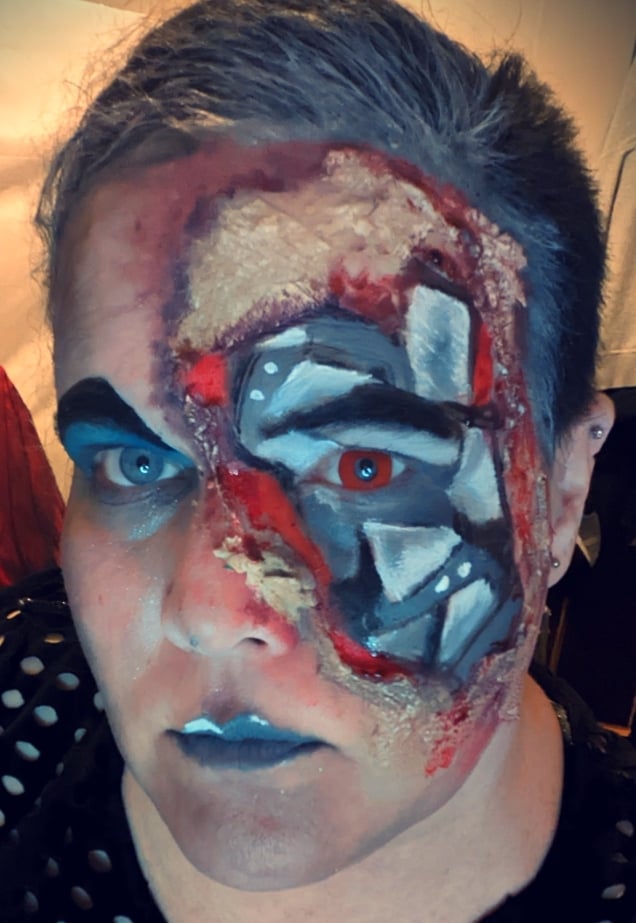
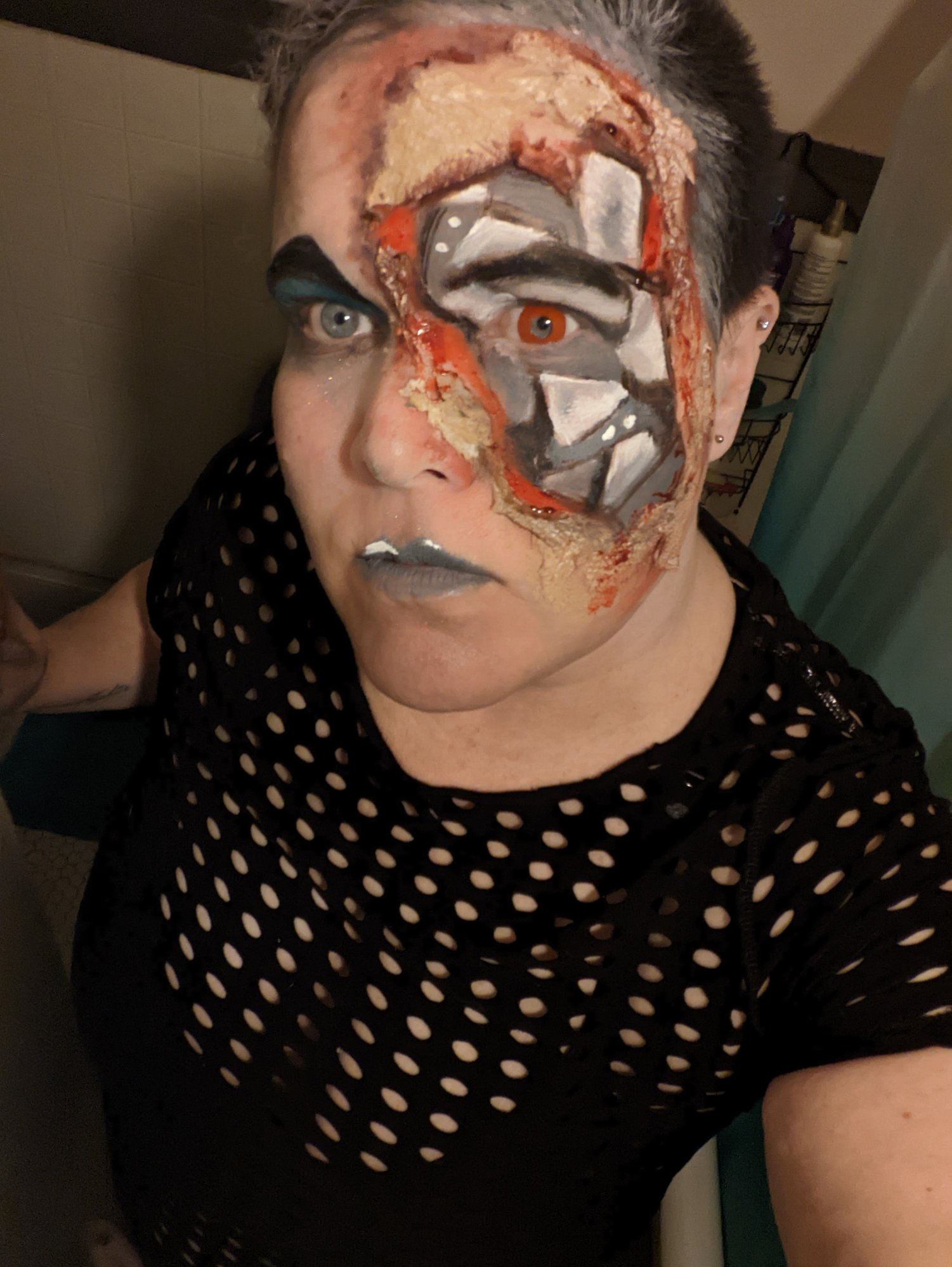
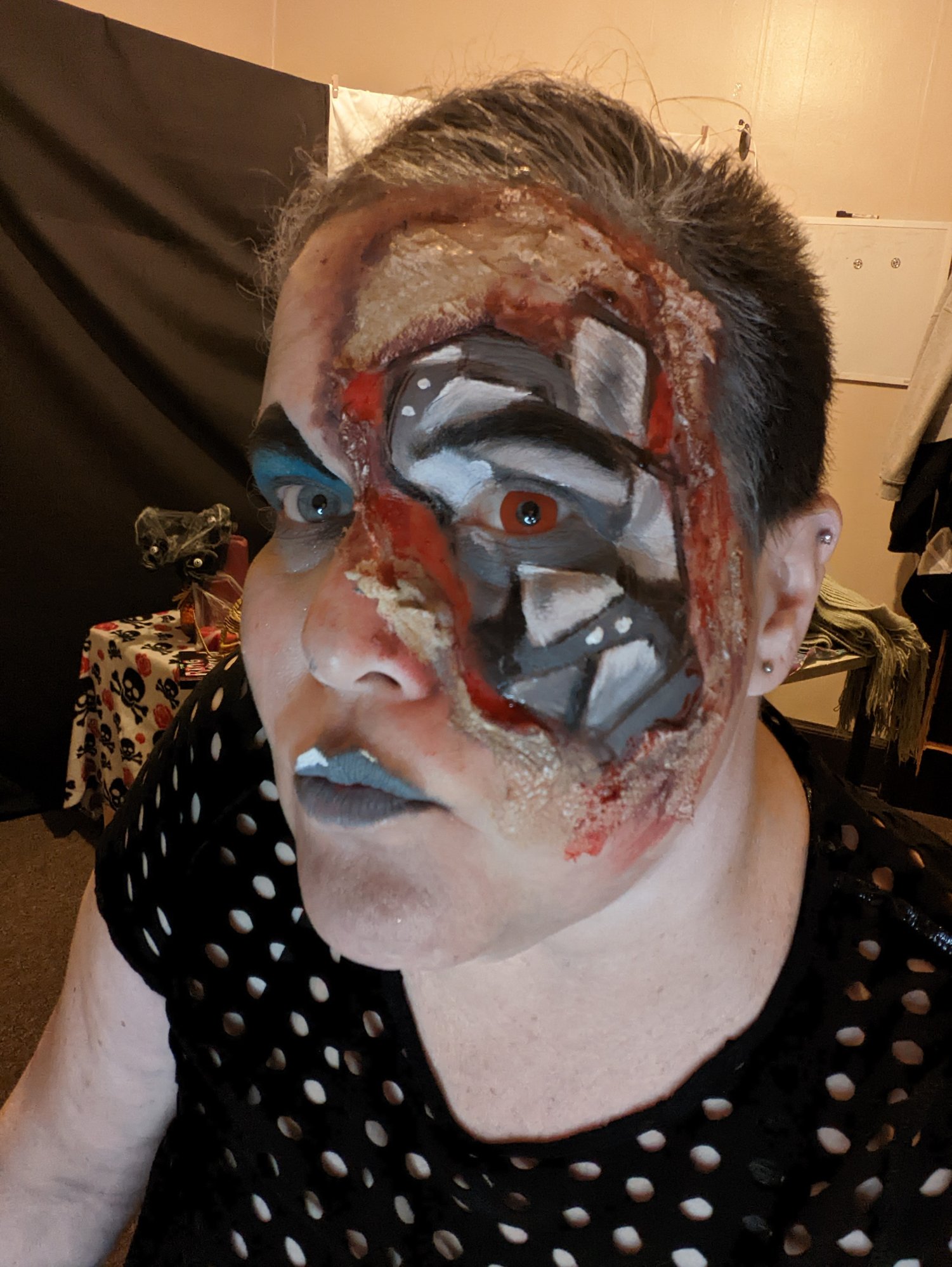
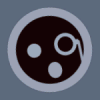
DécaDanse Avec Moi – Julie, La Poupée Dansante
Hello everyone, my name is Giulia and I am an Italian freelance makeup artist based in Bologna. I was always been very passionate about special make-up and from last year I have had the opportunity to work like trainee in some important Italian workshops for various projects.
One
of my favorite hobbies is performing the characters created to
improve my sfx make up skills during some themed events. Today for
the contest I would like to propose to you one of these latest
creatures.
My
inspiration for this character takes place from an idea; the desire
to describe the suffering of a creature who after having lost what
she held dearest, finds in a soul mate the power to be reborn. The
soft colors of the 30's circus are the background of our story. Julie
was a french dancer and circus acrobat. She was known as La poupée
dansante, because during her show she used to wear a beautiful doll
mask that covered her face. Indeed the mask hid two face scars that
caused to Julie so much shame. One day, while she was on the
tightrope, she fell. The trauma was so grave that since then she
hasn't been able to dance as before. The mask that protected her from
naughty and indiscreet people’s eyes was broken on the right side,
exposing that shameful macabre smile. Julie felt useless and the
people around treated her like a broken toy that can be thrown away.
In the end they kicked her out of the circus. Julie was ravaged, she
had lost all her certainties. She wanted to end it all. Was the
encounter with Jerome to safe her. He was a gruff tramp clown who can
no longer make people laugh. Their same suffering has made them
inseparable e from those day they support each other in their
“DecaDance” life.
The
mask of Julie is made in resin. I sculpted it on a plaster core of my
face. After that, I made a mold with layers of silicone and plaster
bandages. I painted everything with acrylic inks only with brushes.
The scars are two encapsulated silicone gel pieces that I have
sculpted on another plaster core of my face and placed on a flat
board. I applied these pieces by myself and colored them with alcohol
based colors. The costume is sewed and customized by myself as the
dread locks. Jerome was created and performed by my workmate Maxx.
I
really hope you appreciate and consider my application,
My
best regards,
Giulia.
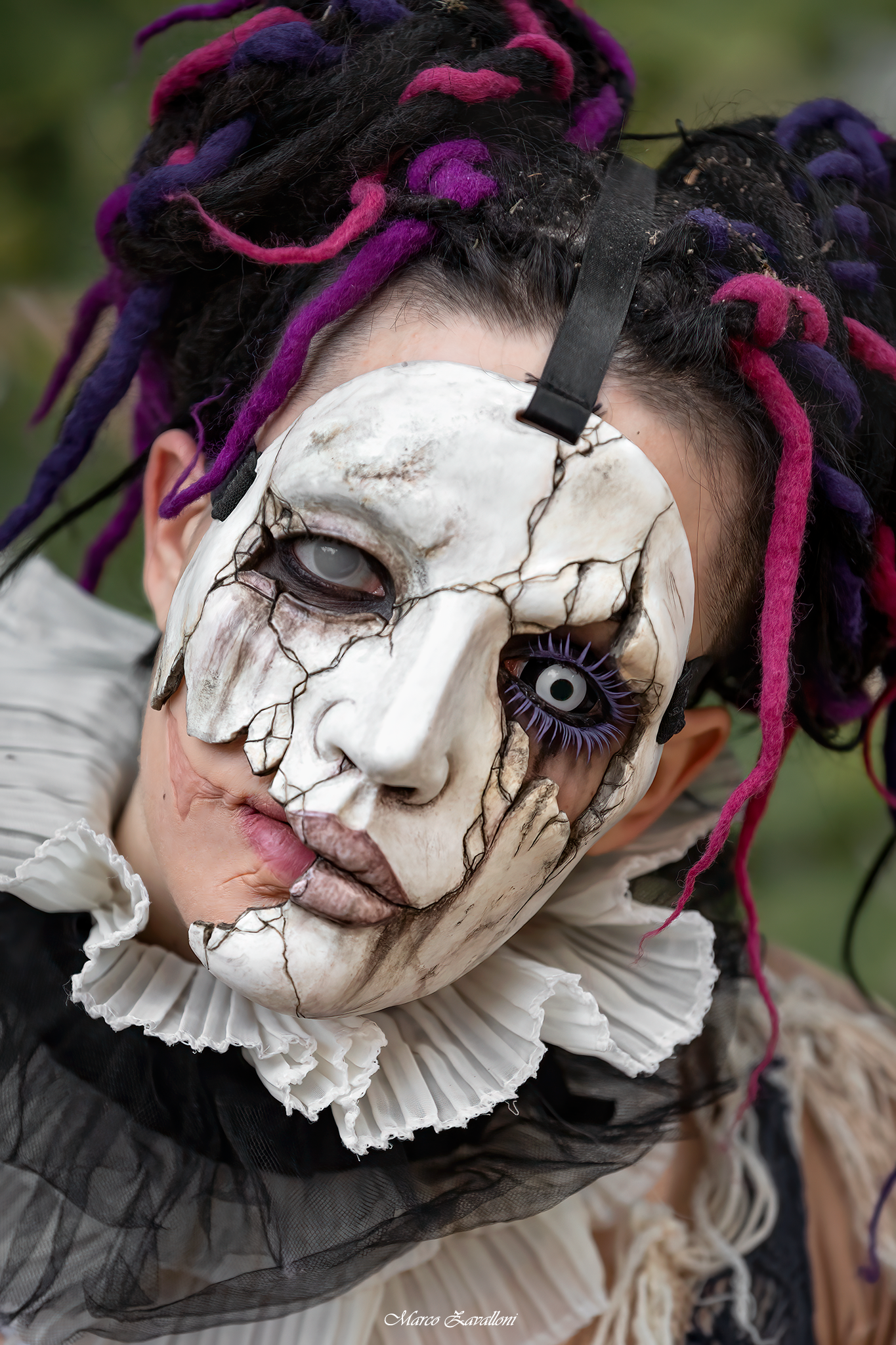
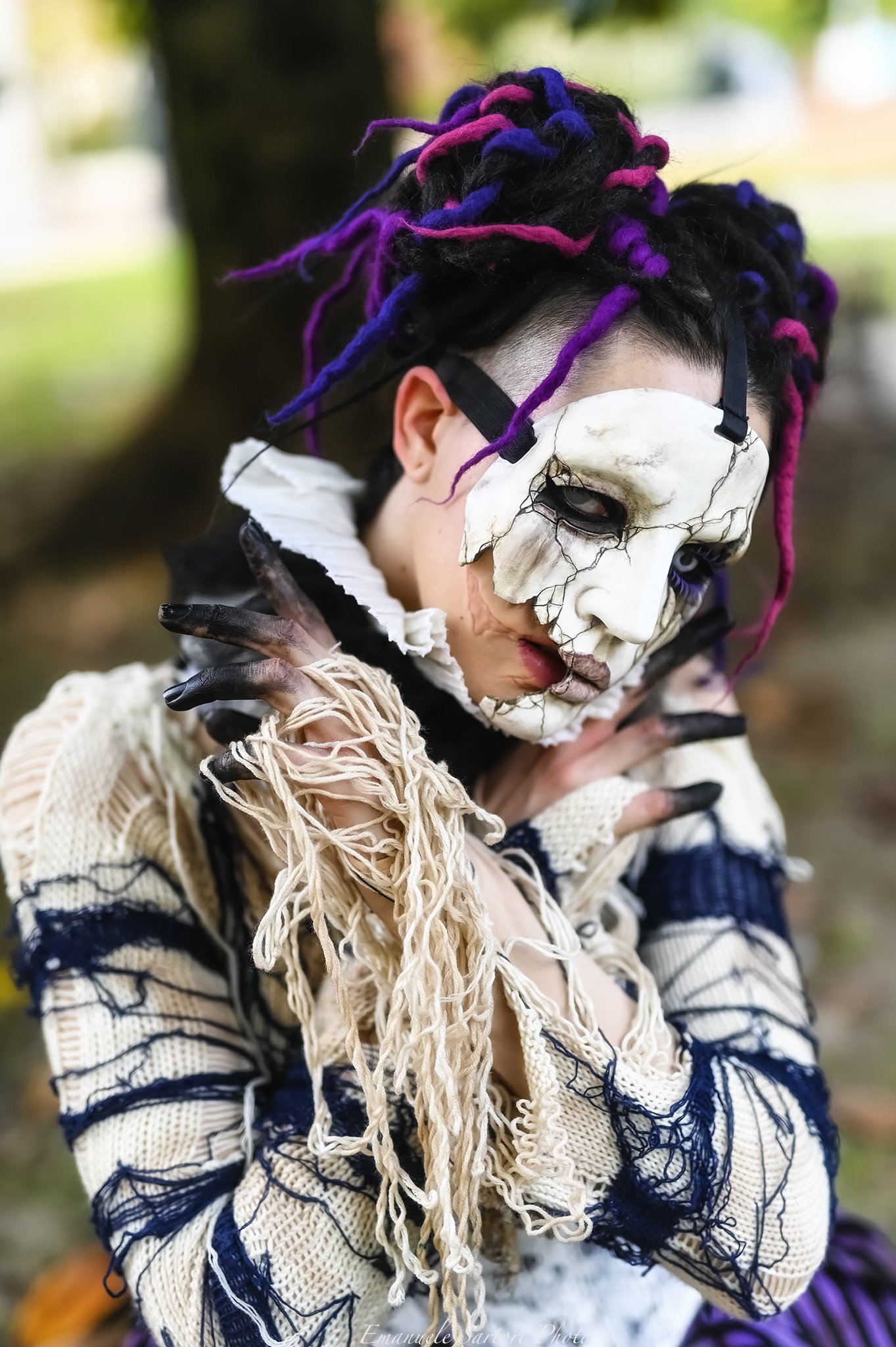
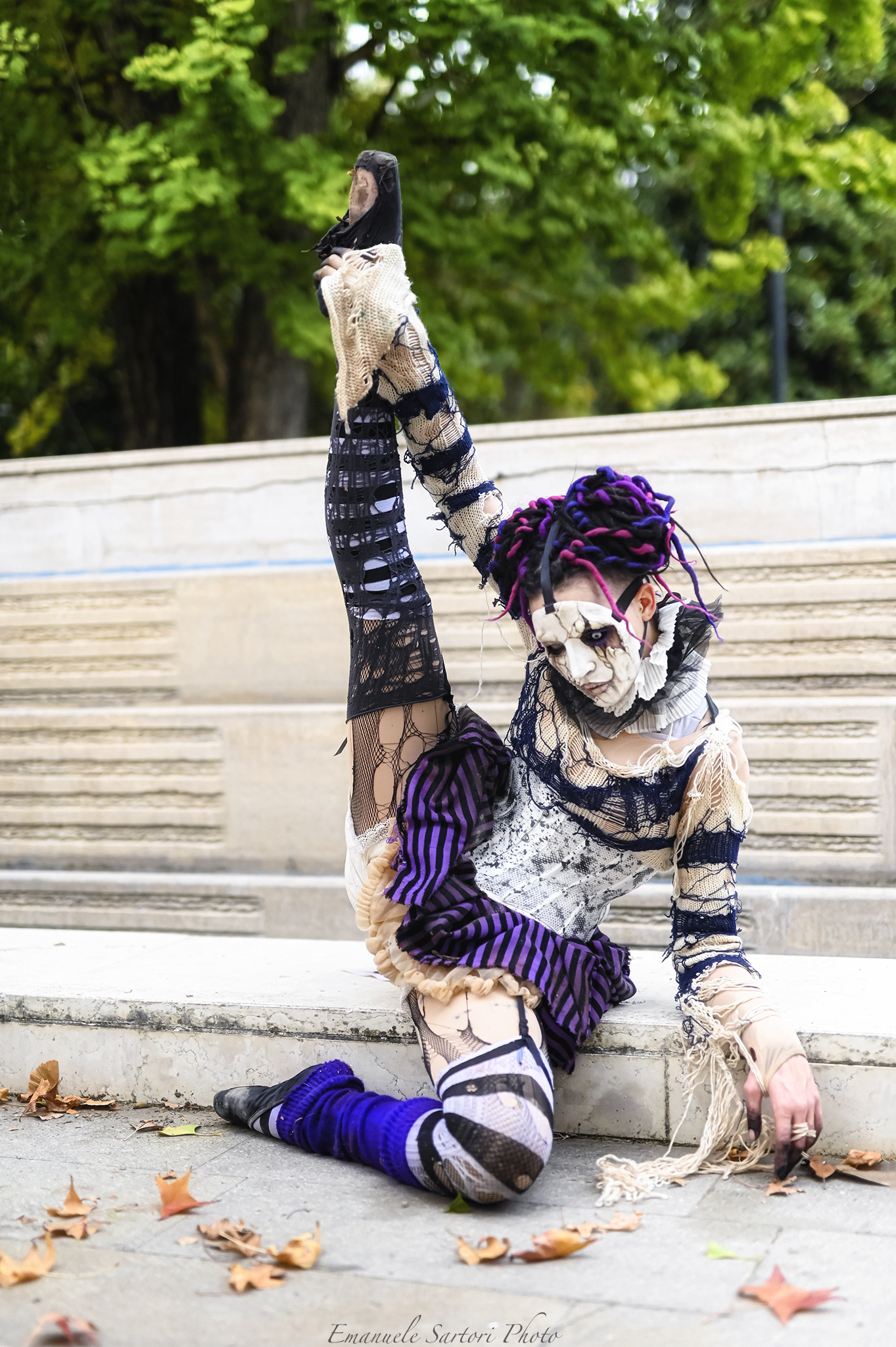
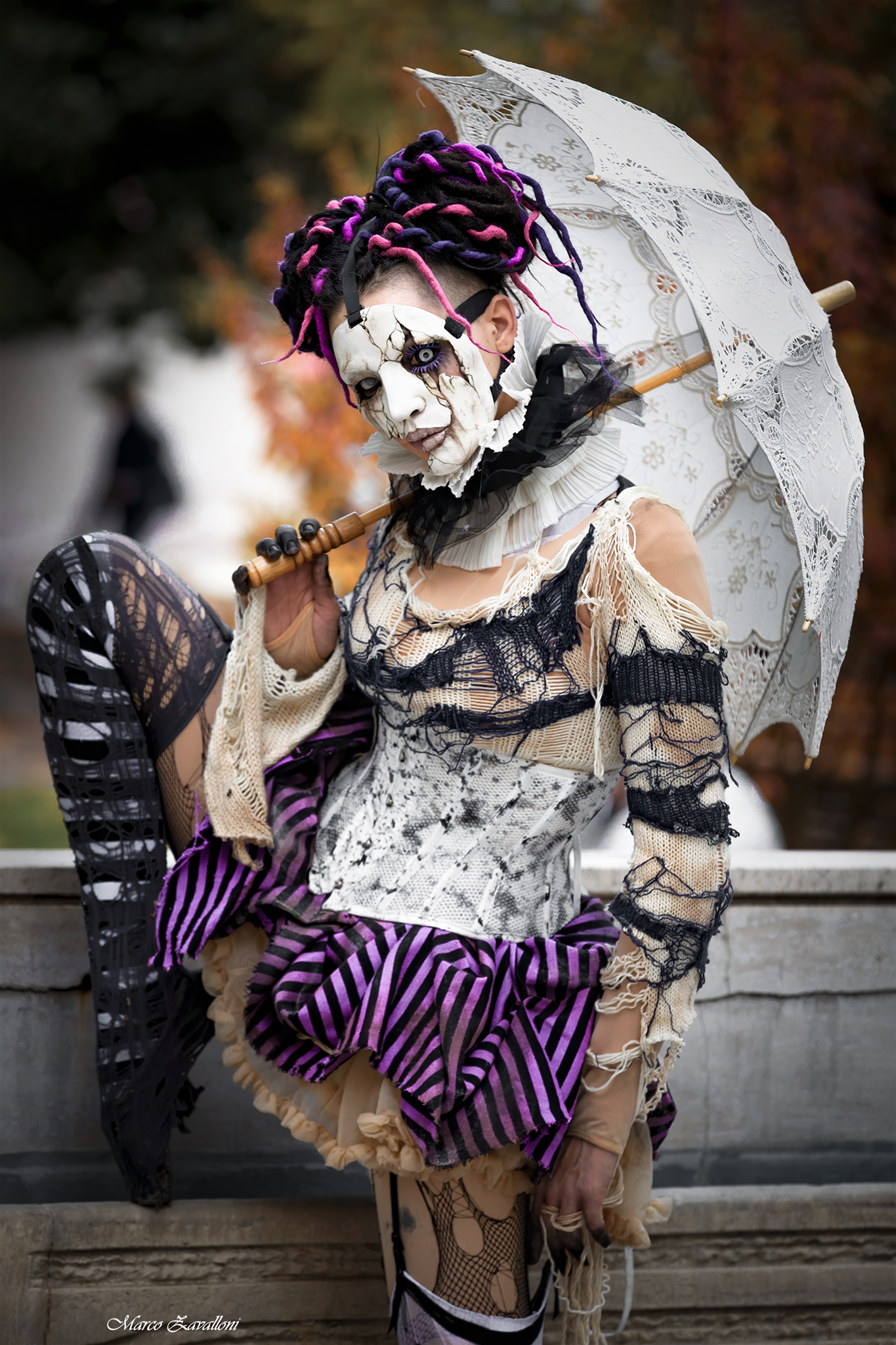
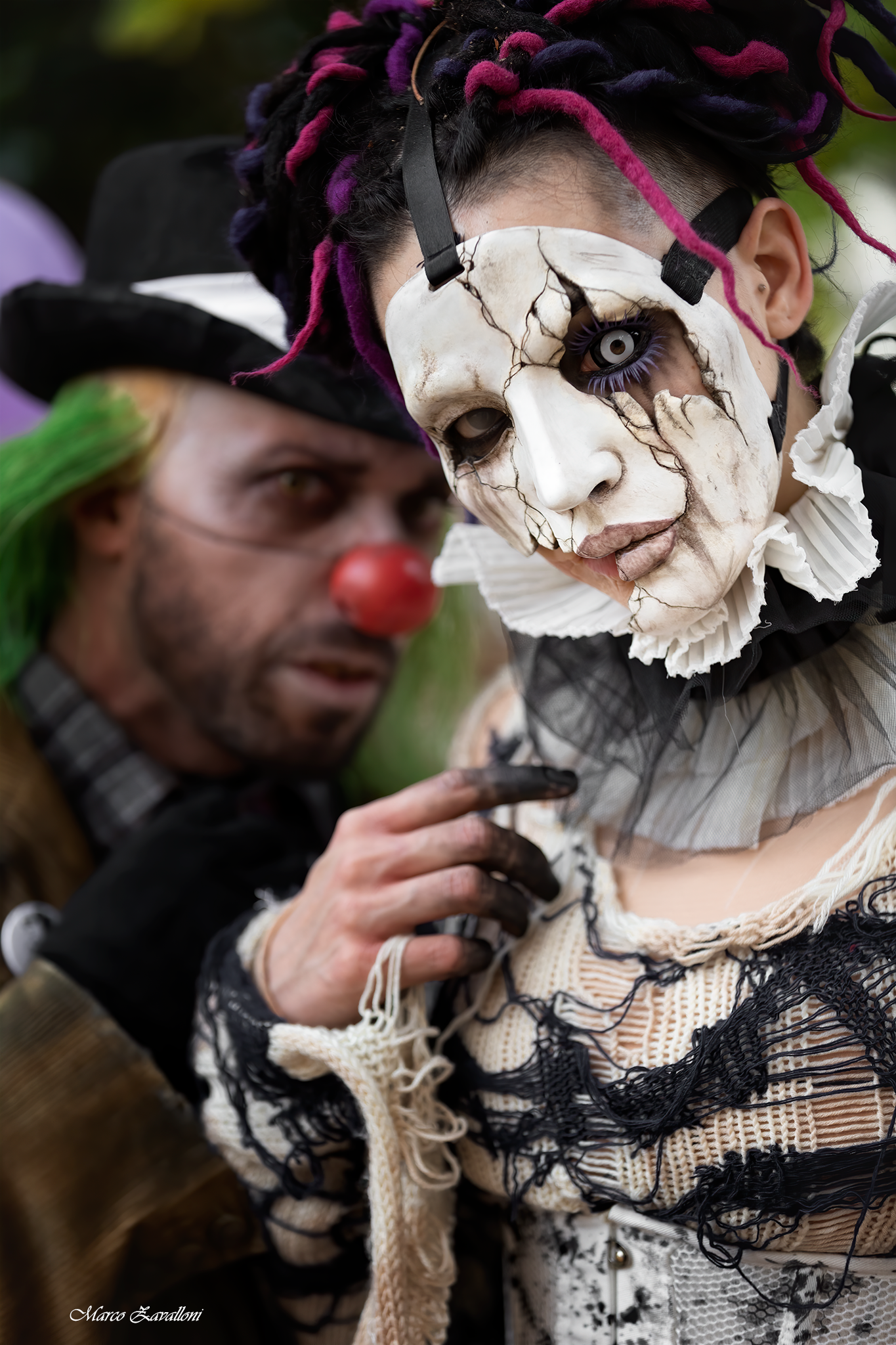
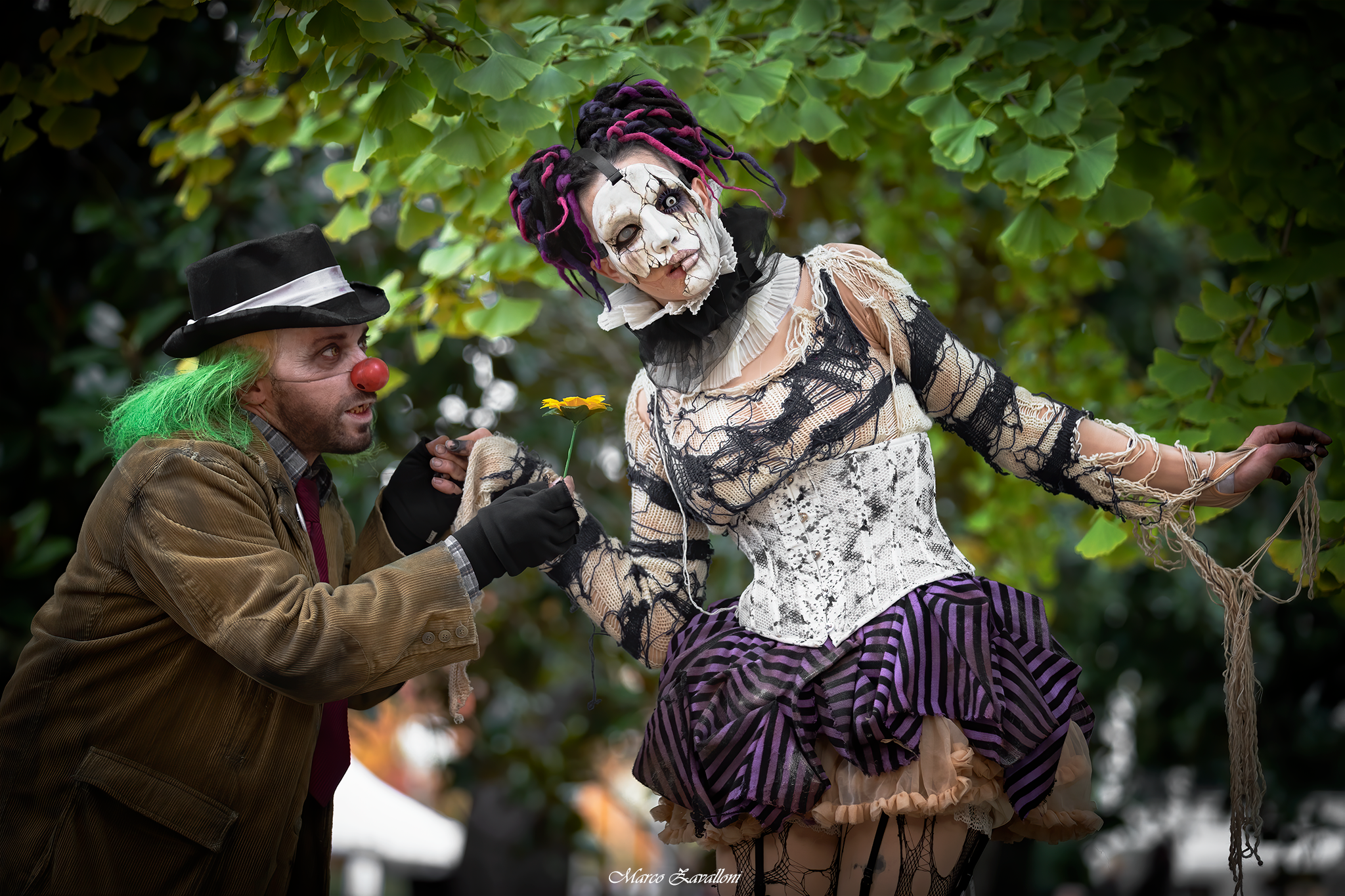
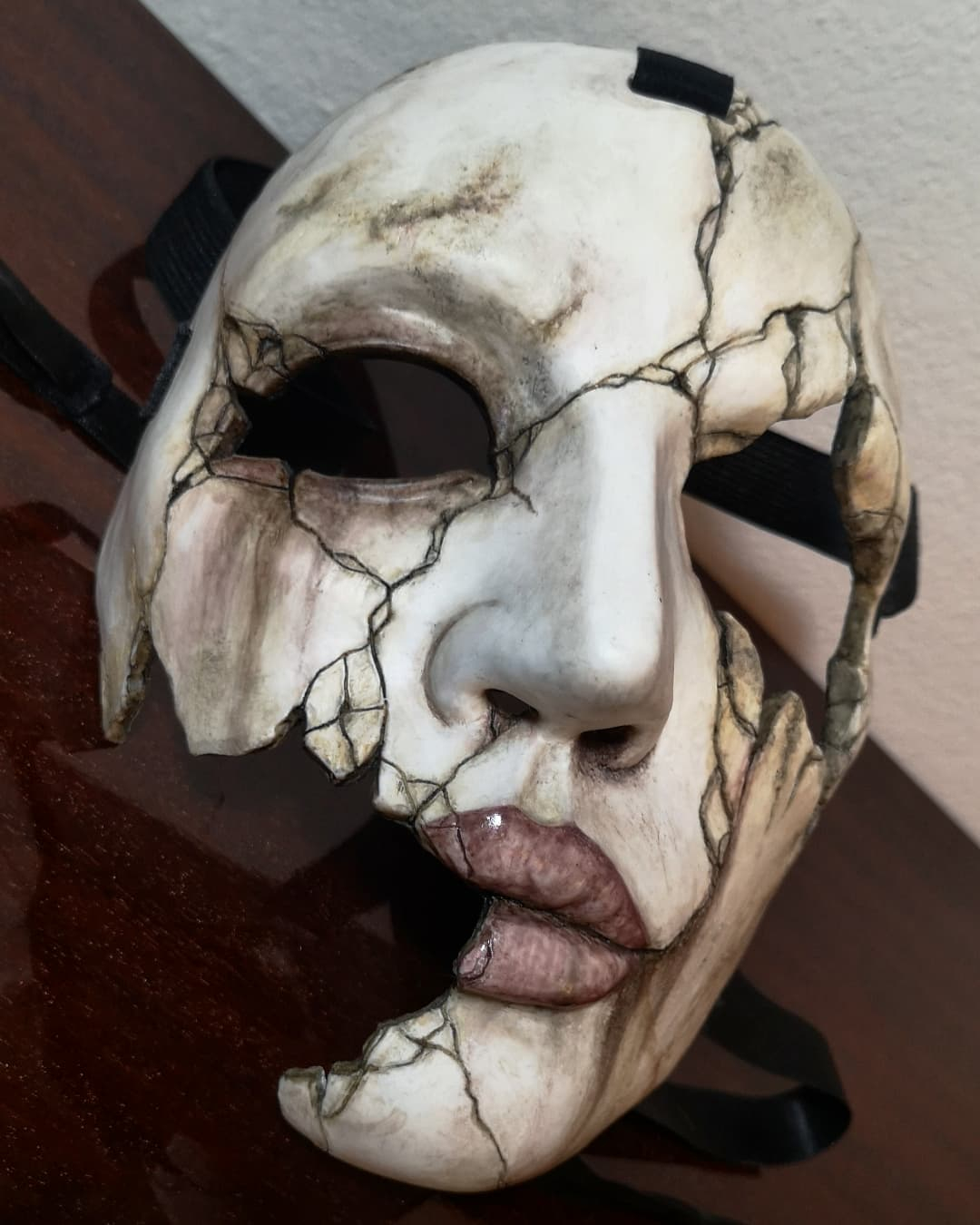
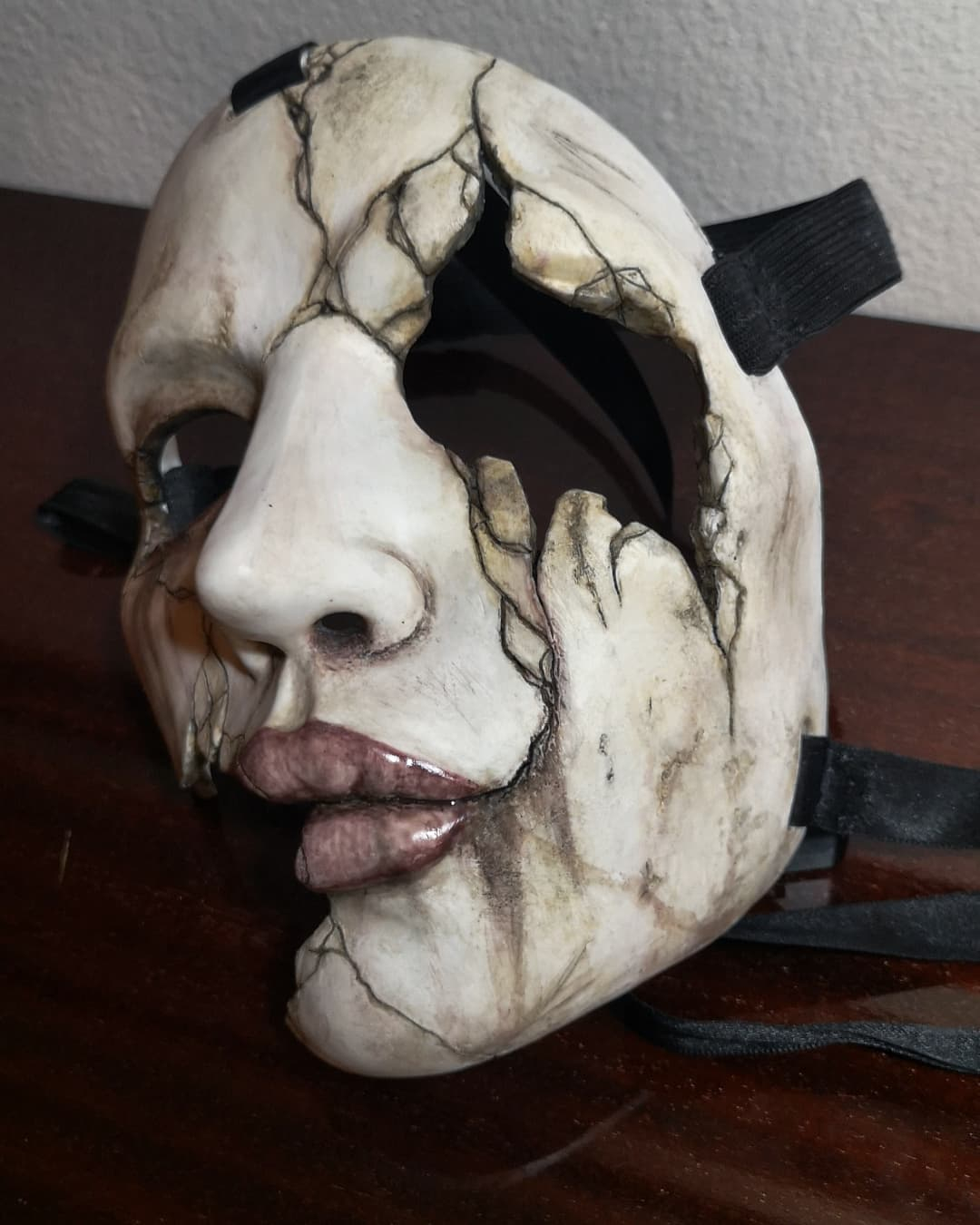
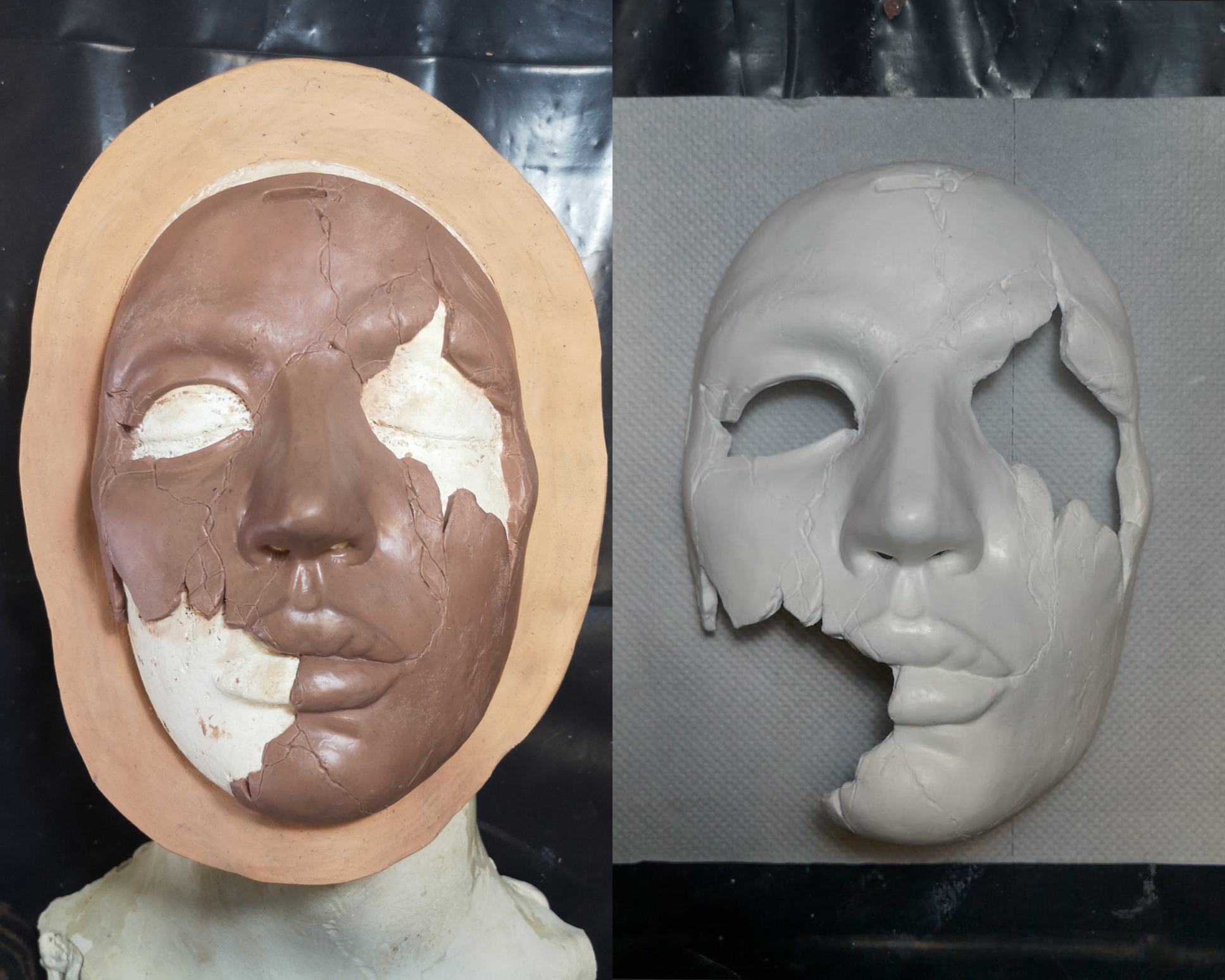
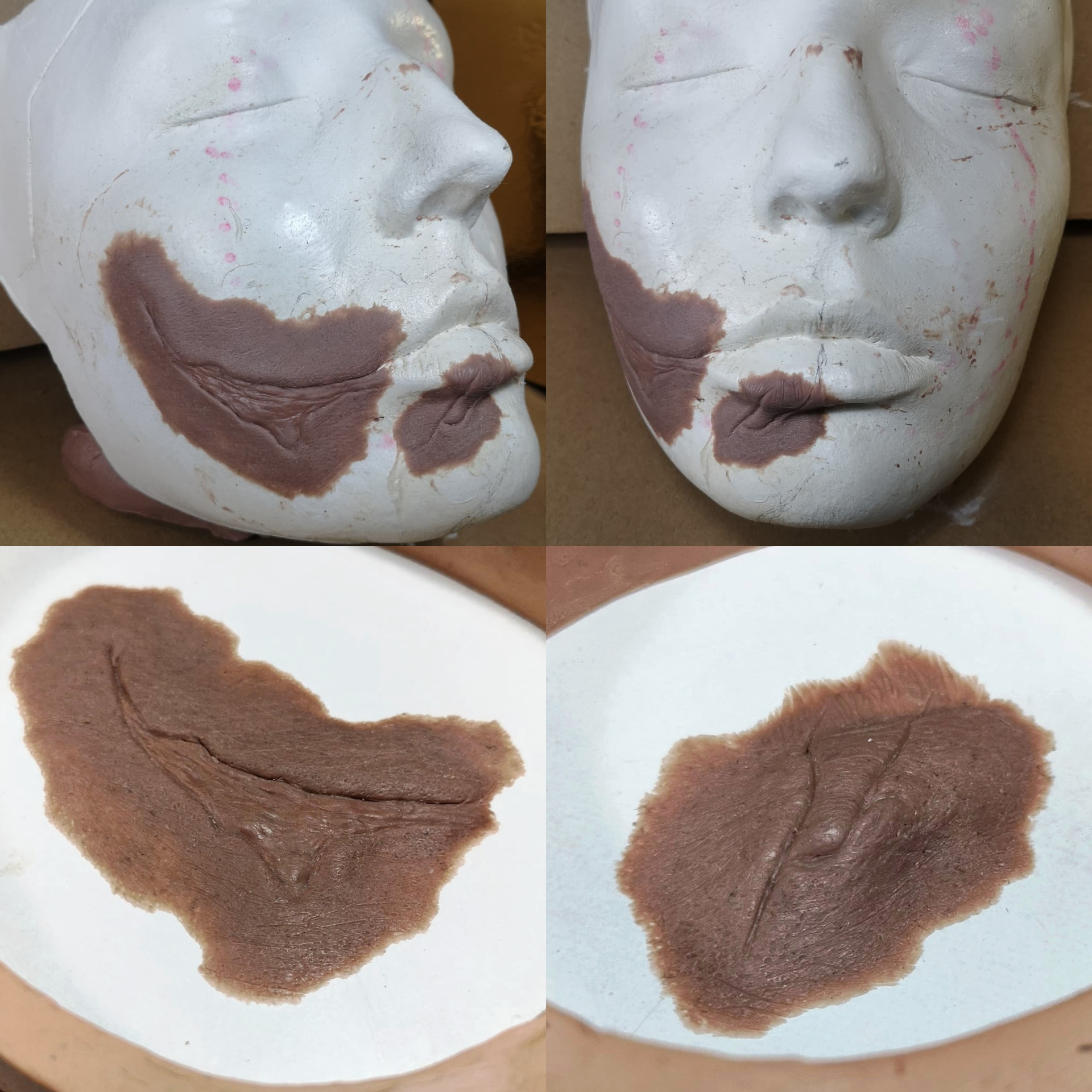
Punk Rock Peacock

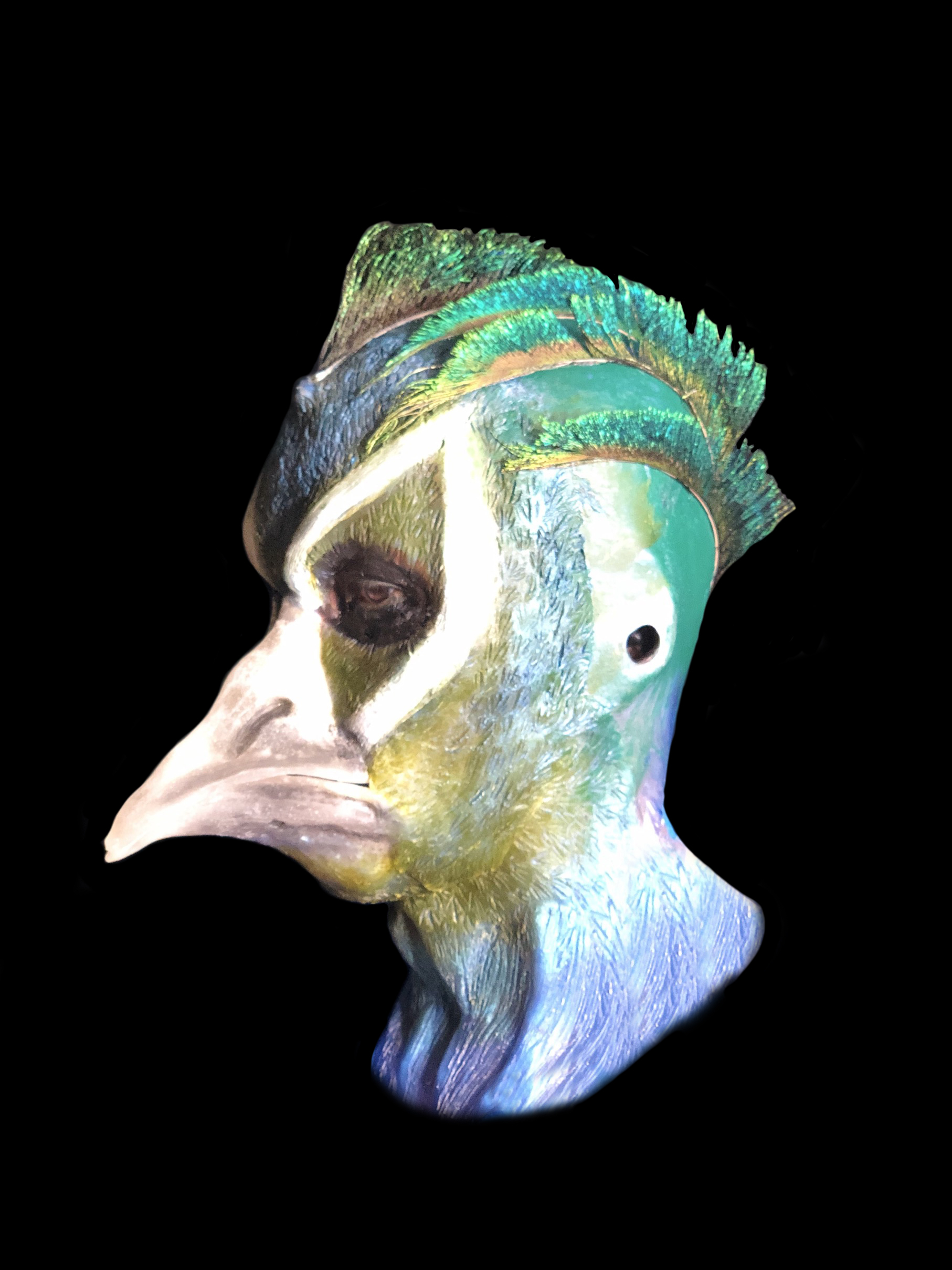
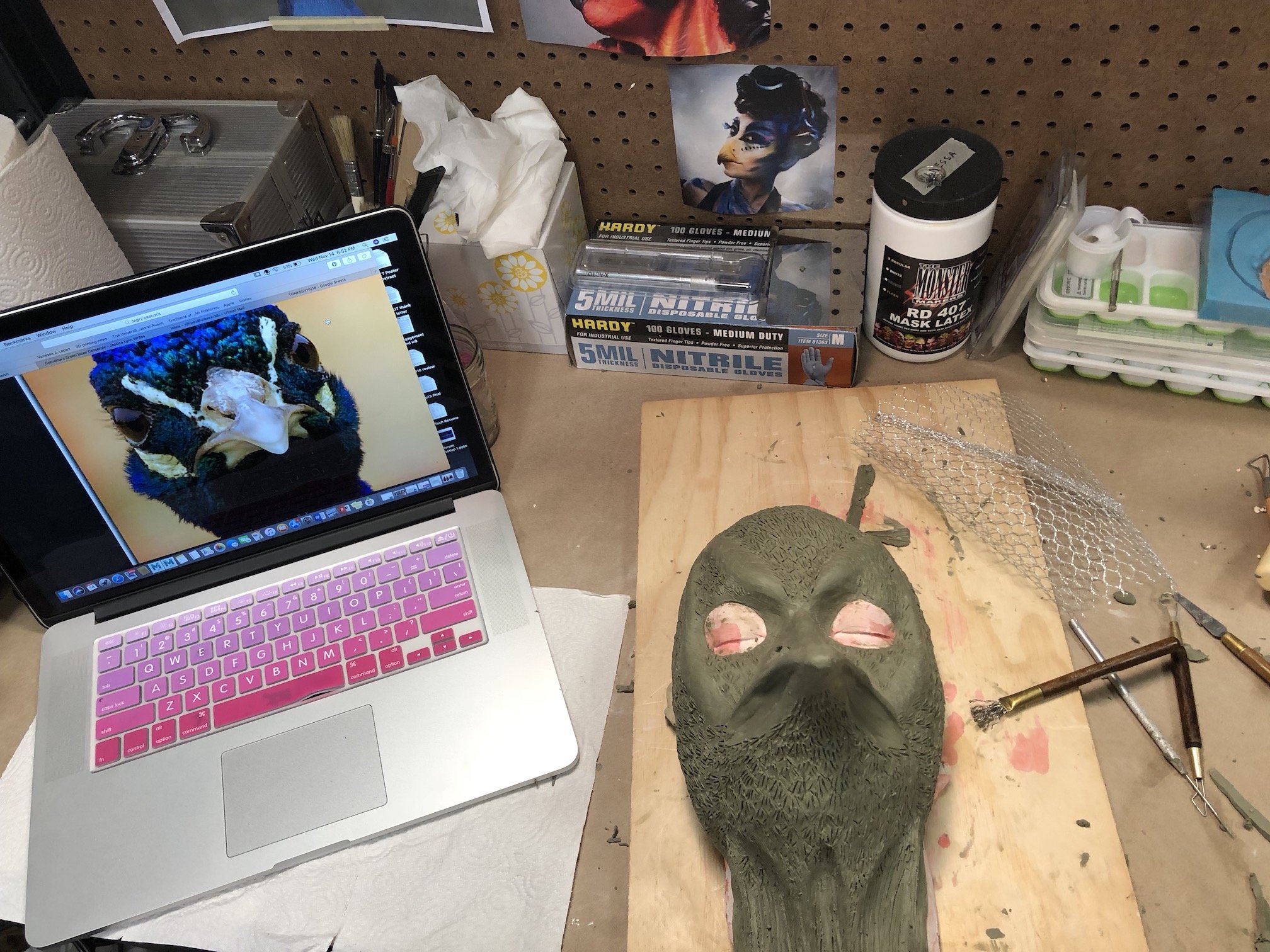
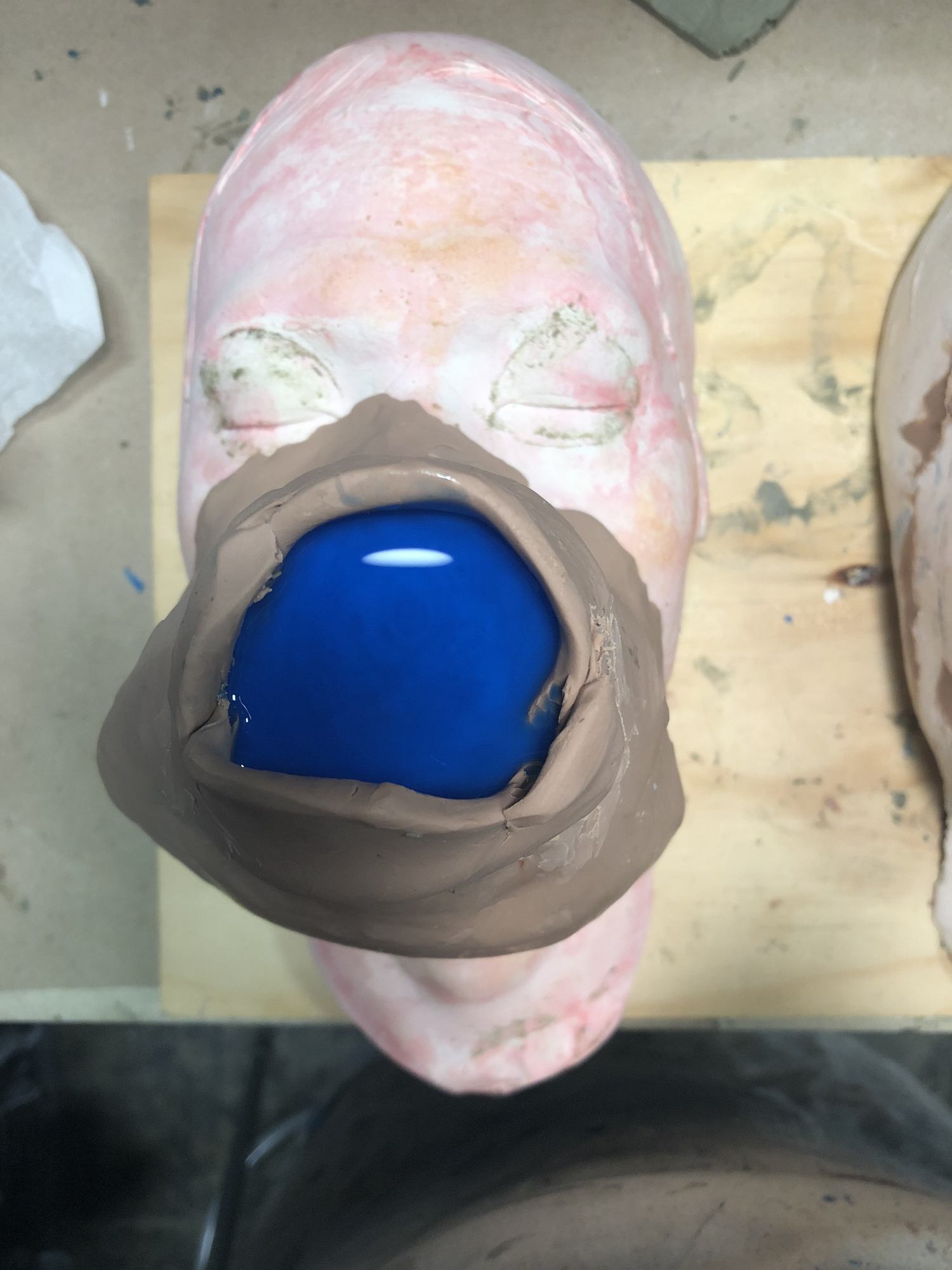
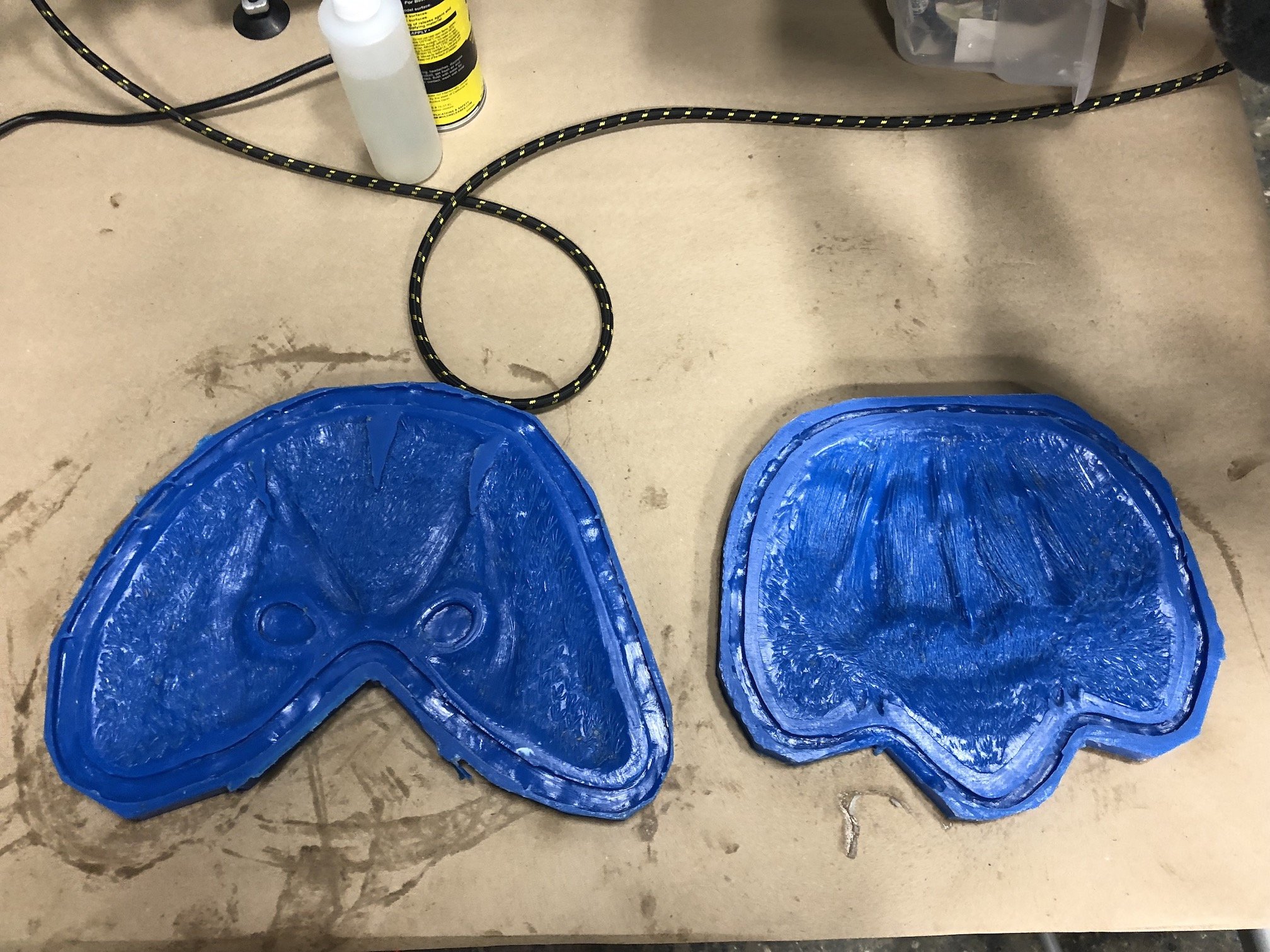
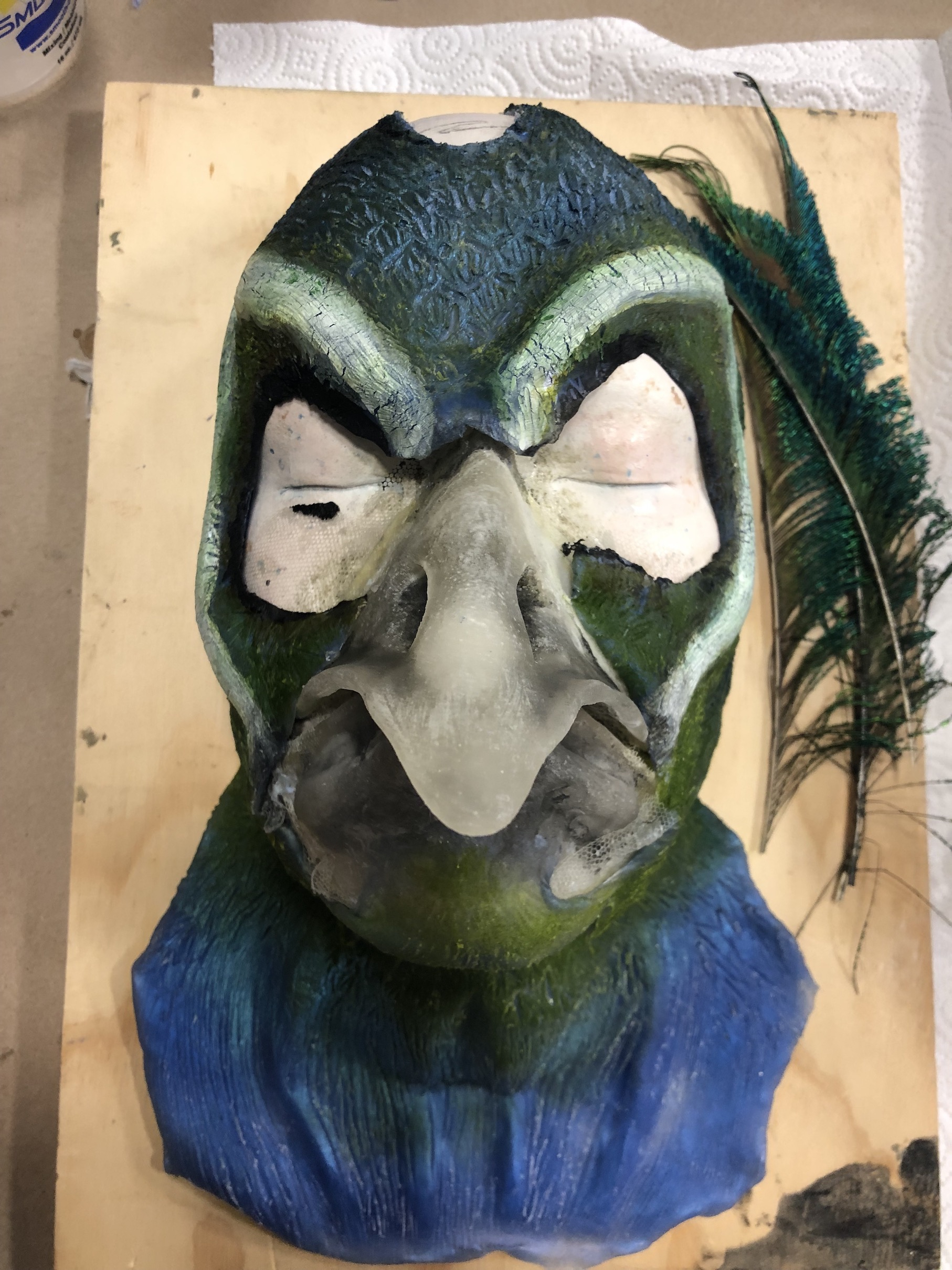
Re: Revenant Bear Grease Replacement
Look into making a mixture of beeswax and an oil, similar to how beard waxes are made. I'd also look into non-spoiling oils so the costume lasts. You could even mix in natural scents like pine, leather, smoke, to add to the impact of the costume, but I'd be careful to stick to pleasing scents and not go too heavy with them.
Lanolin may also be an optional additive/base.
Then you could mix in oil-friendly pigments to get the color and saturation you are after.
You can run small tests on scrap fabrics to fine-tune your mixture.
/Chris
Re: Remake of the props of a hybrid baby from the movie "Sweet tooth"
Souhaiter: The Wishing Well Spirit
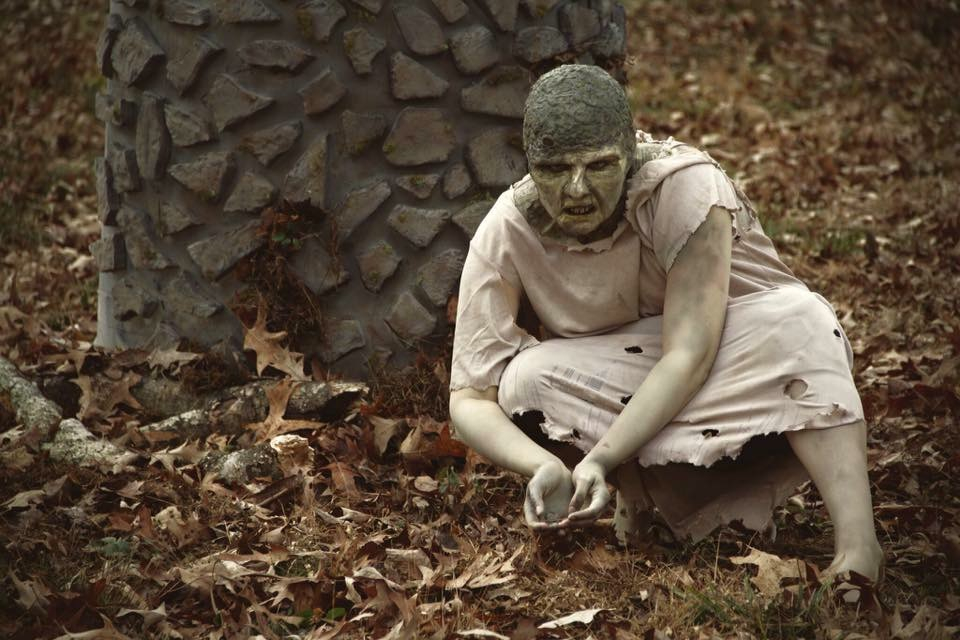
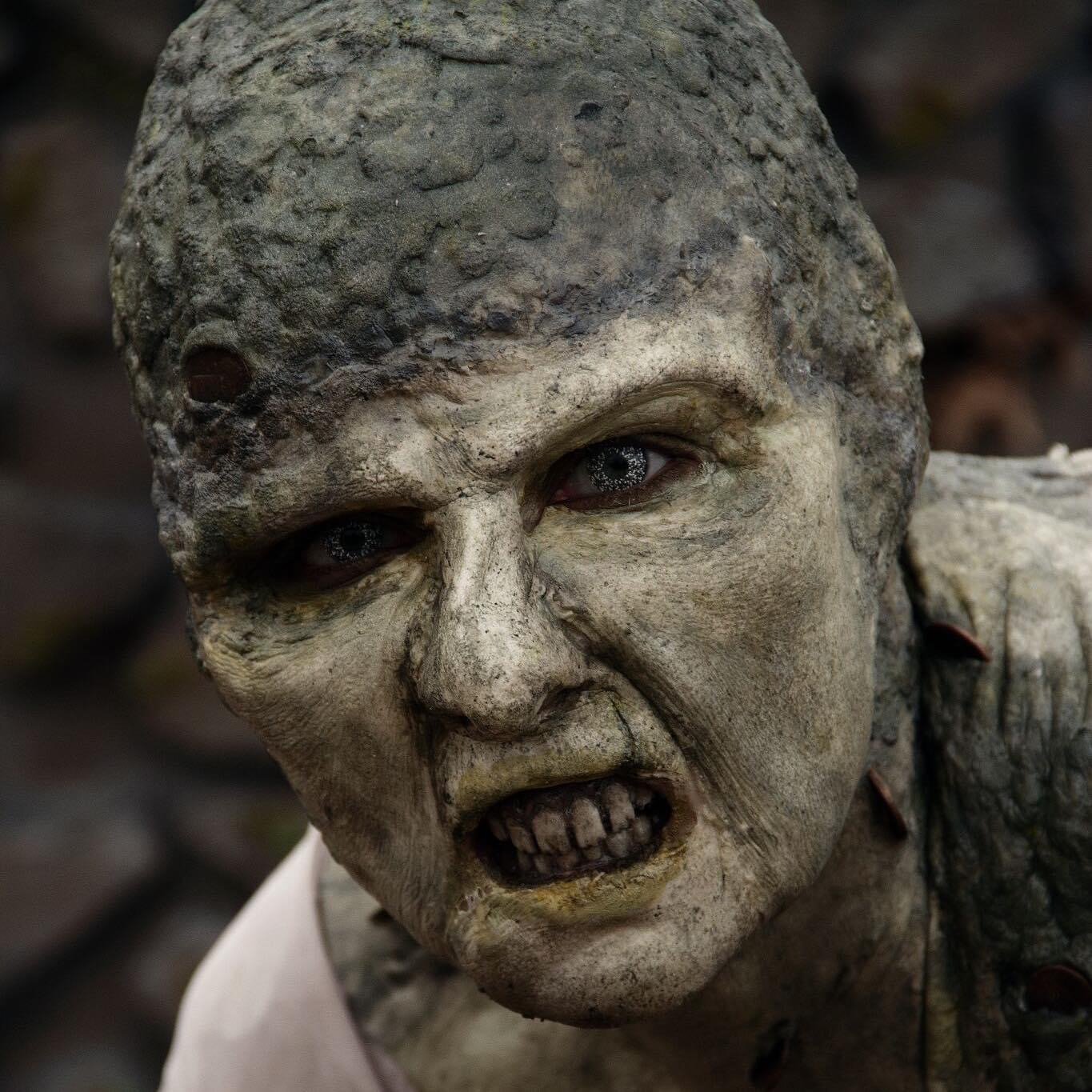
Eddie The Trooper - Iron Maiden
• Sculpted in chavant medium.
• 10 appliances run in Platgel10, deadened, and encapsulated.
• Painted using skin illustrator palettes and EBA endura paints for airbrush.
• Teeth by Chris Lyons (FangsFX)
• Model was Kyle Whittington, who also made the flag prop.
• Application assistant - Riah Fielding-Walters
• Makeup done at The Prosthetics Event 2019
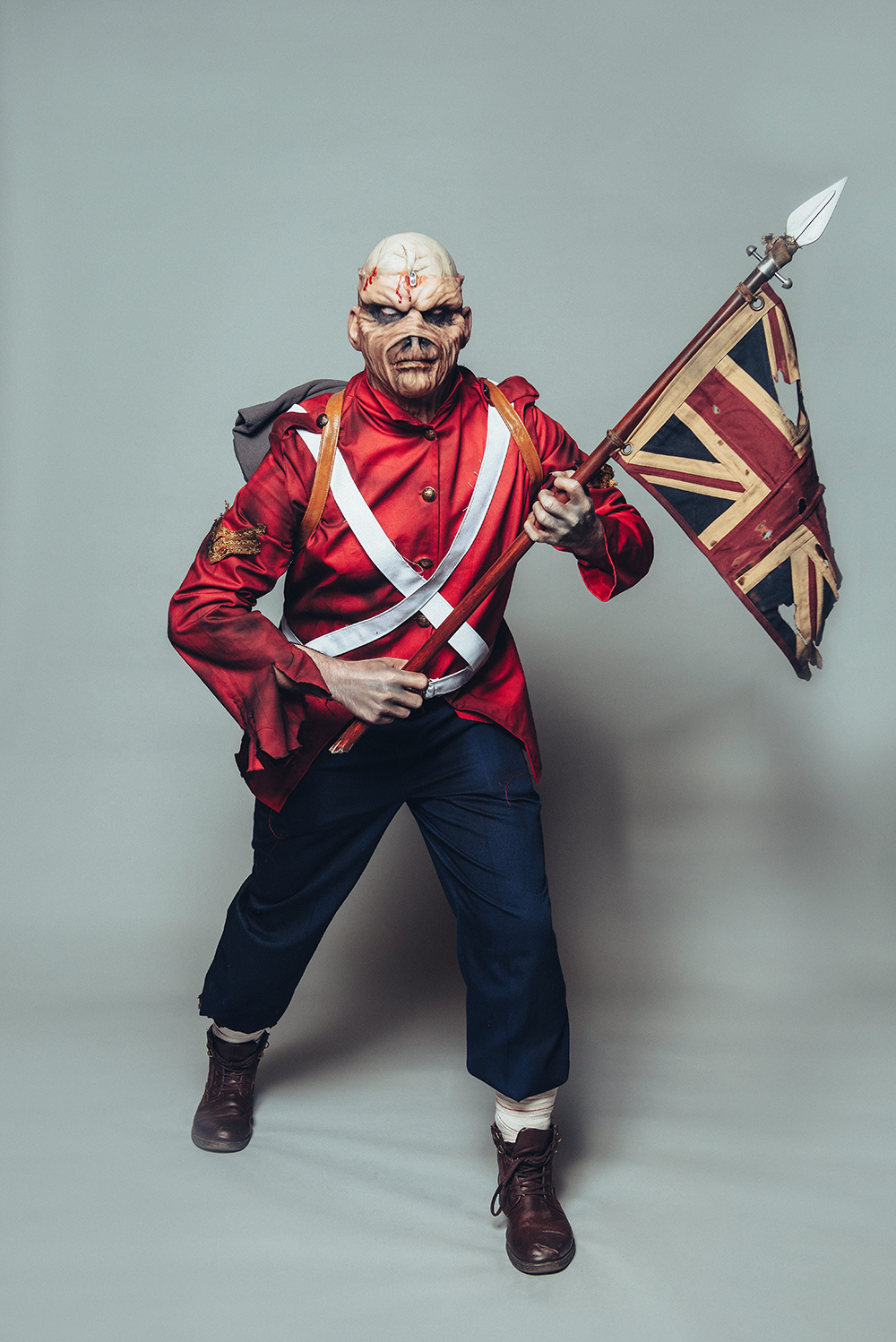
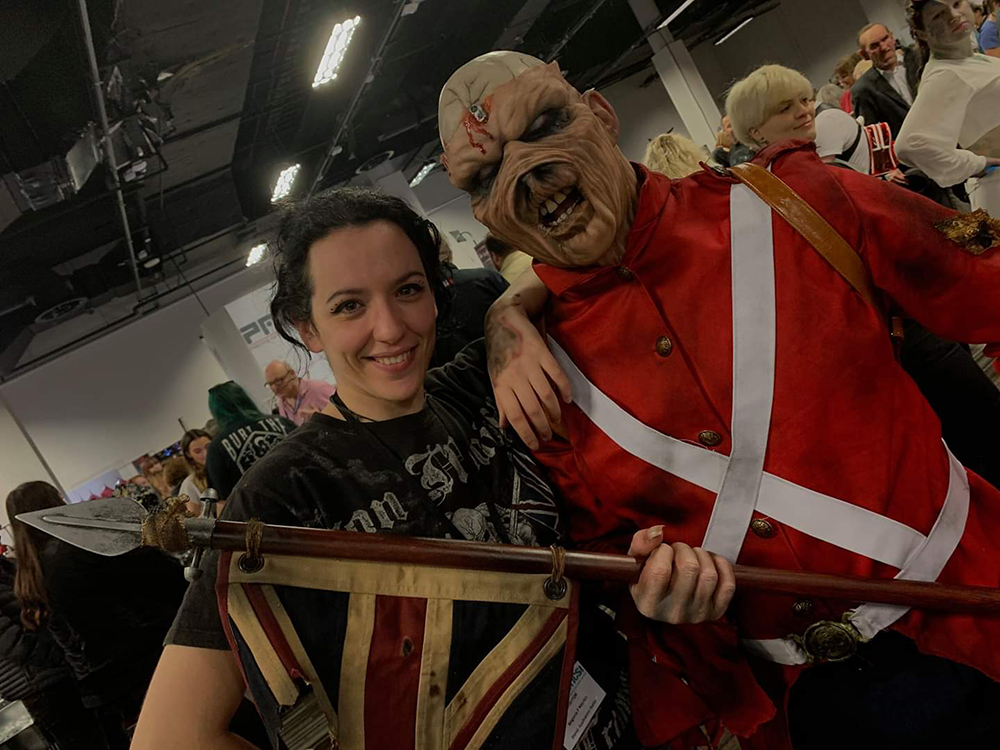
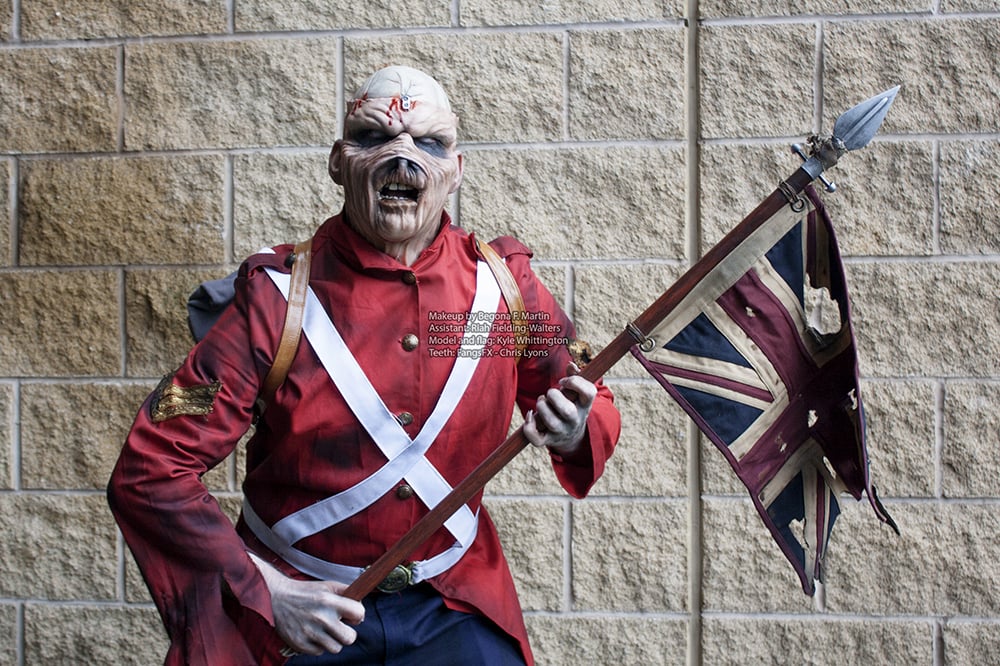
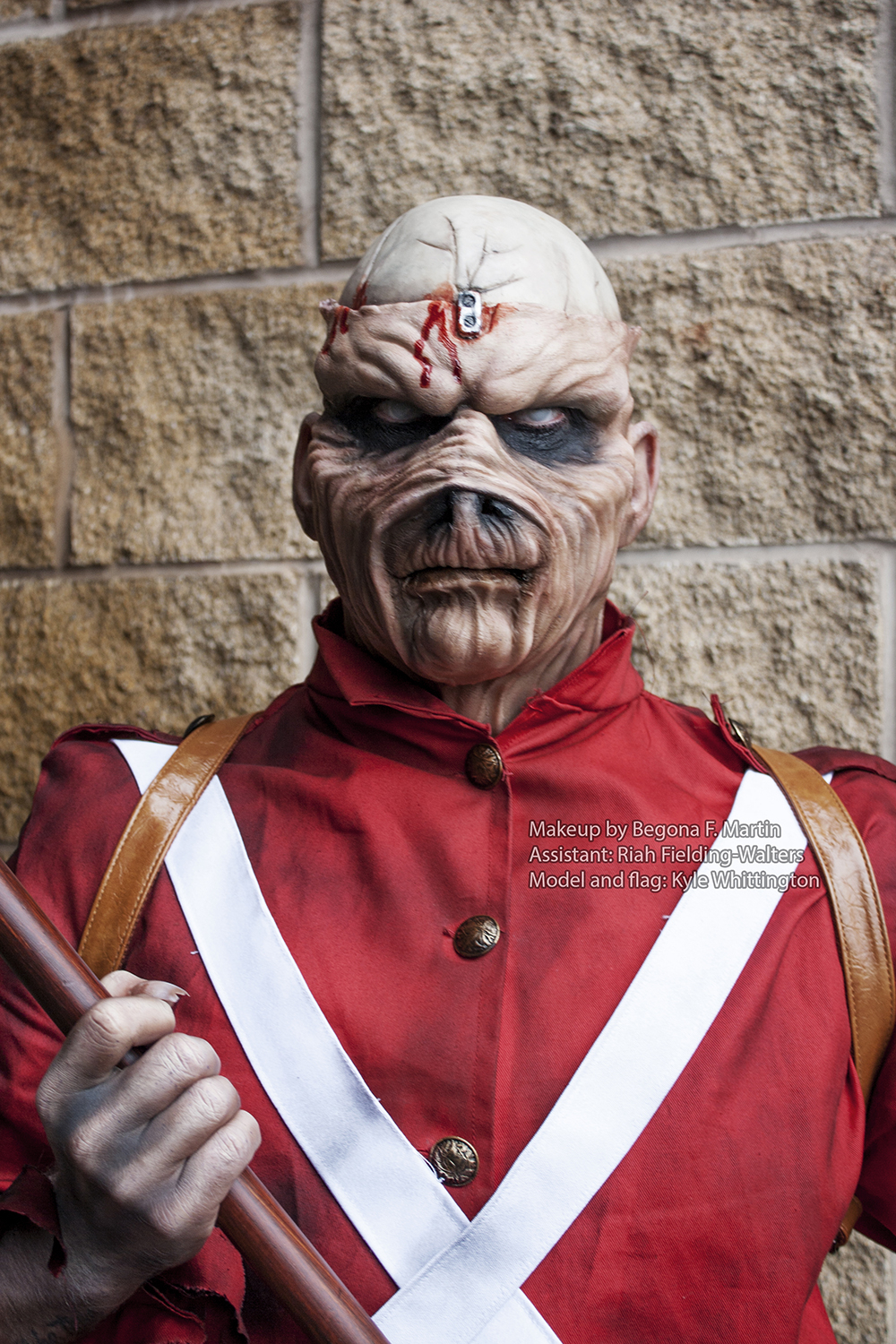
Yaoguai Demon
Makeup & prosthetics by myself Begoña F. Martín
Teeth by Chris Lyons (FangsFX)
Model Jason Ludwig
Photos by myself and Ben Bentley
.
I got to demo this humanoid Yaoguai (Chinese demon) inspired character.
Sculpted, run, and applied by me using Plastiline clay, run in Platsil gel10, encapsulated using IPA cap plastic from. Horns also made be.
Airbrushed with endura paints, also painted using skin illustrators and Neil Materials palettes.
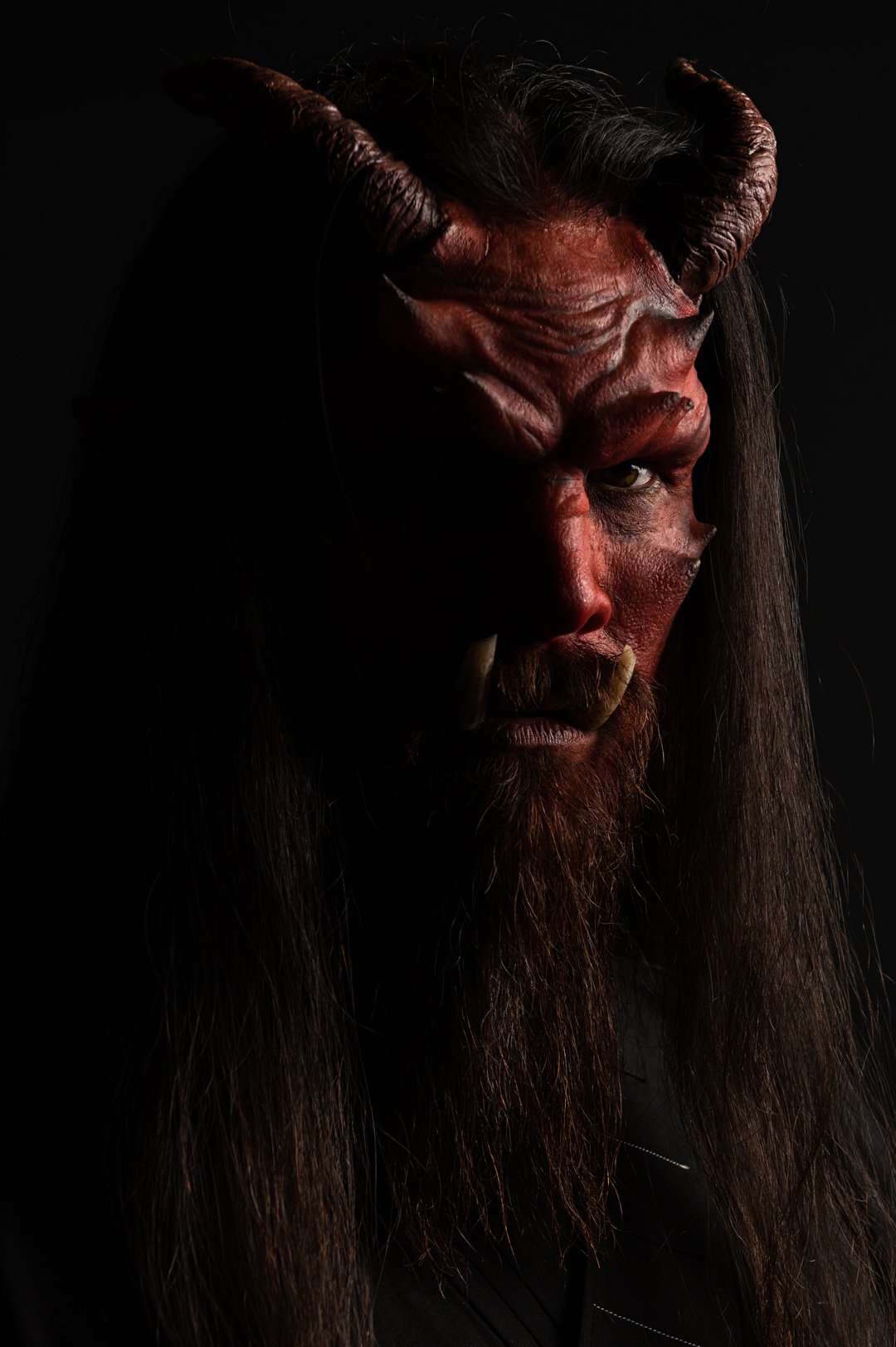
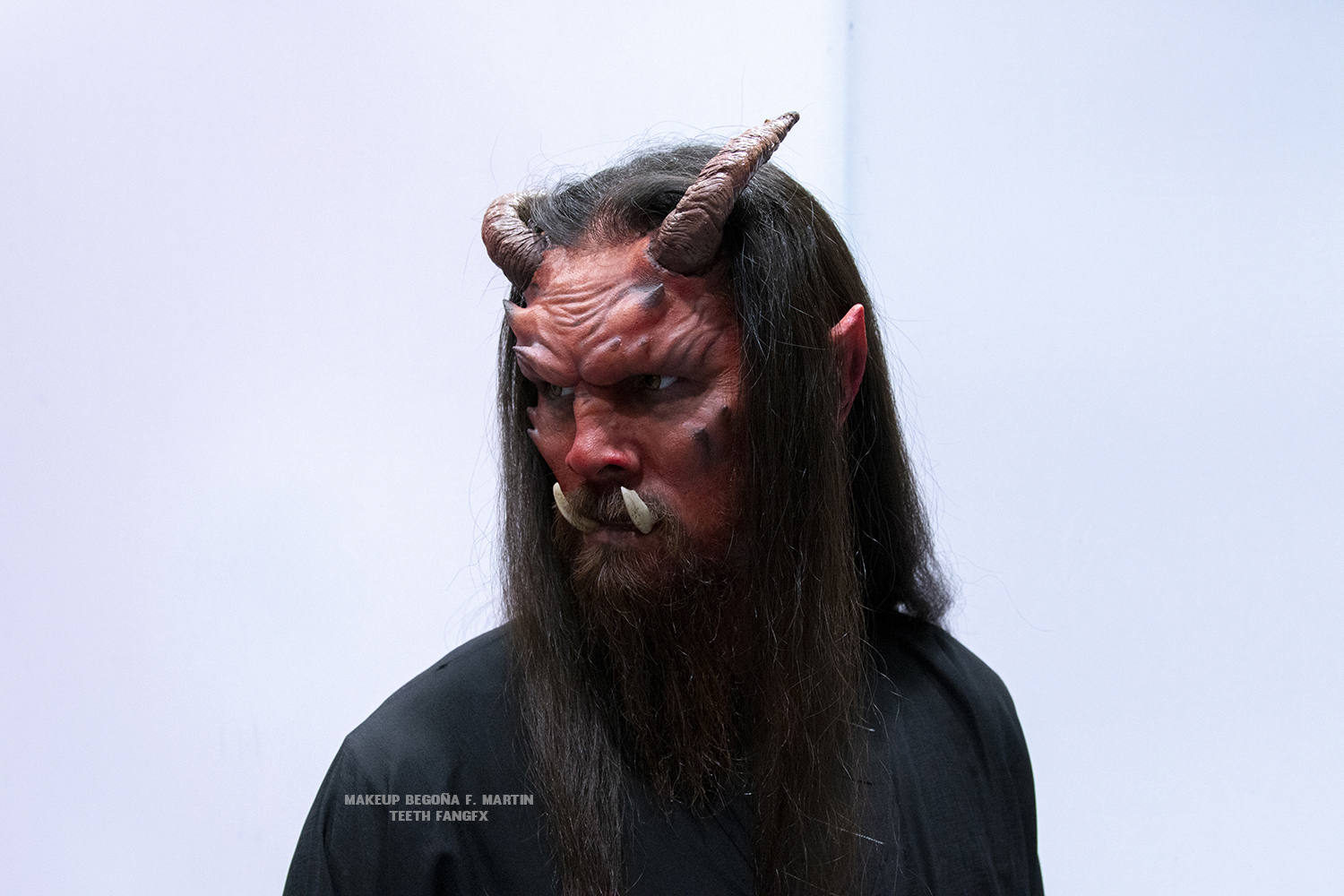
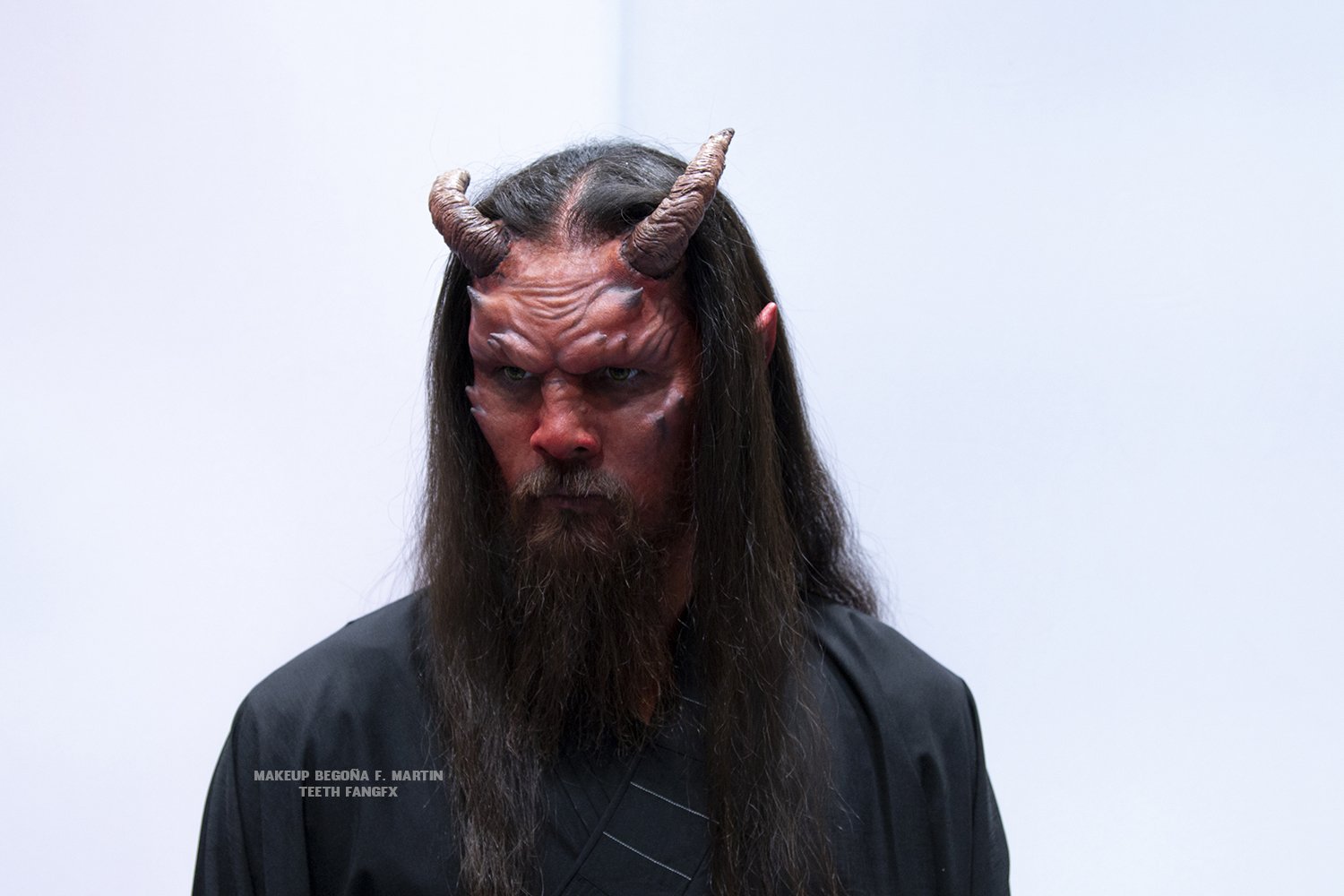
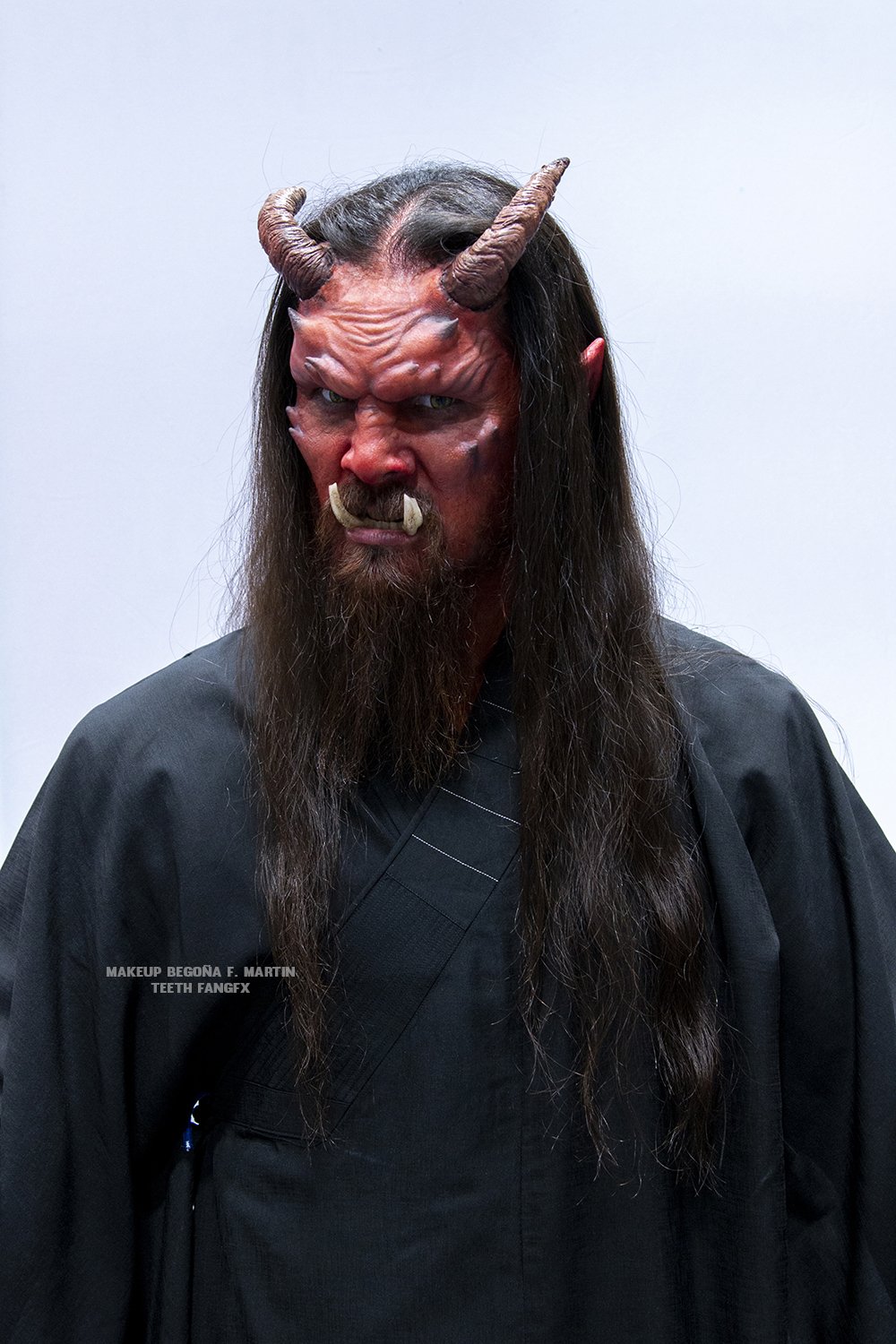
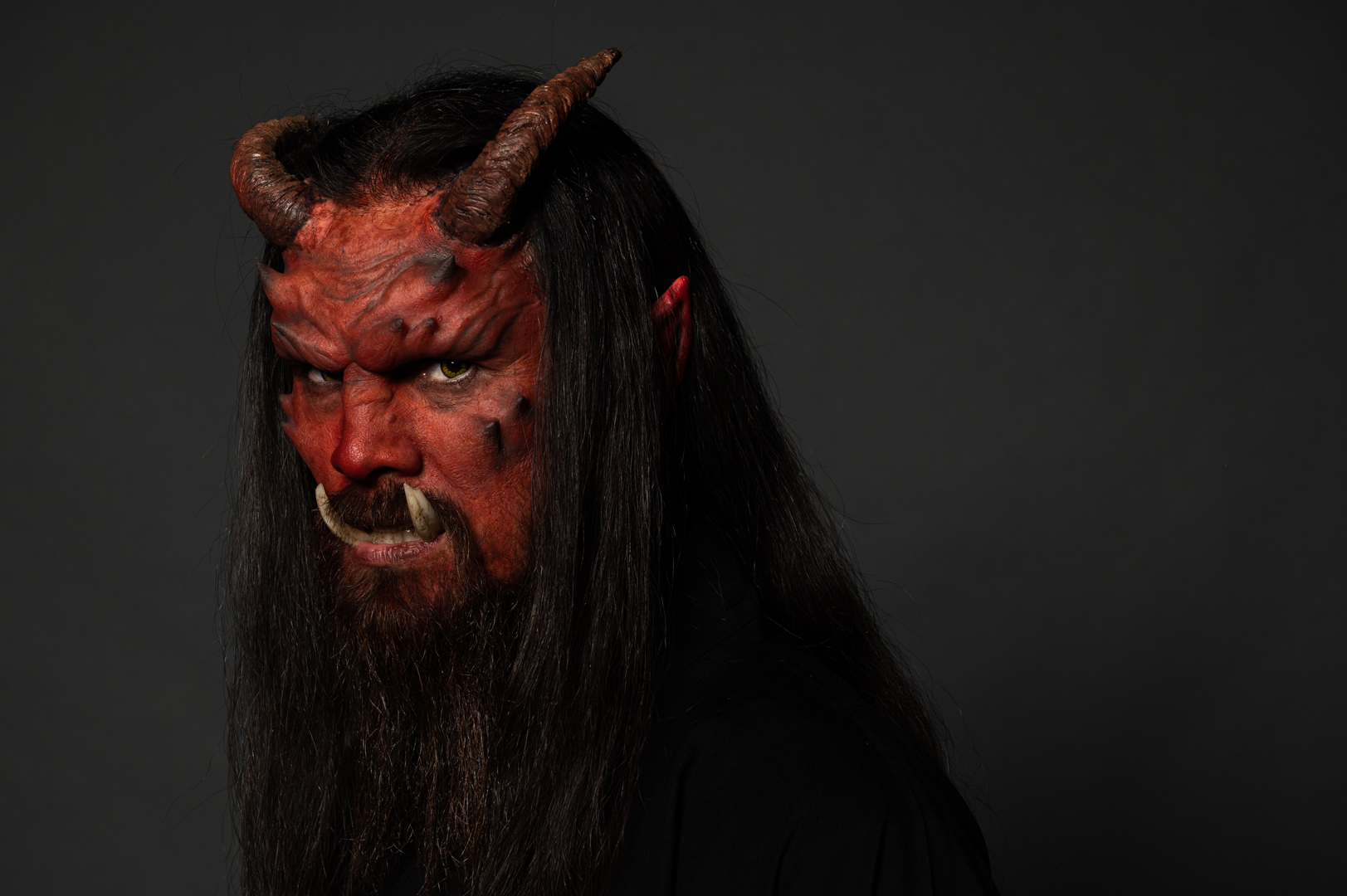
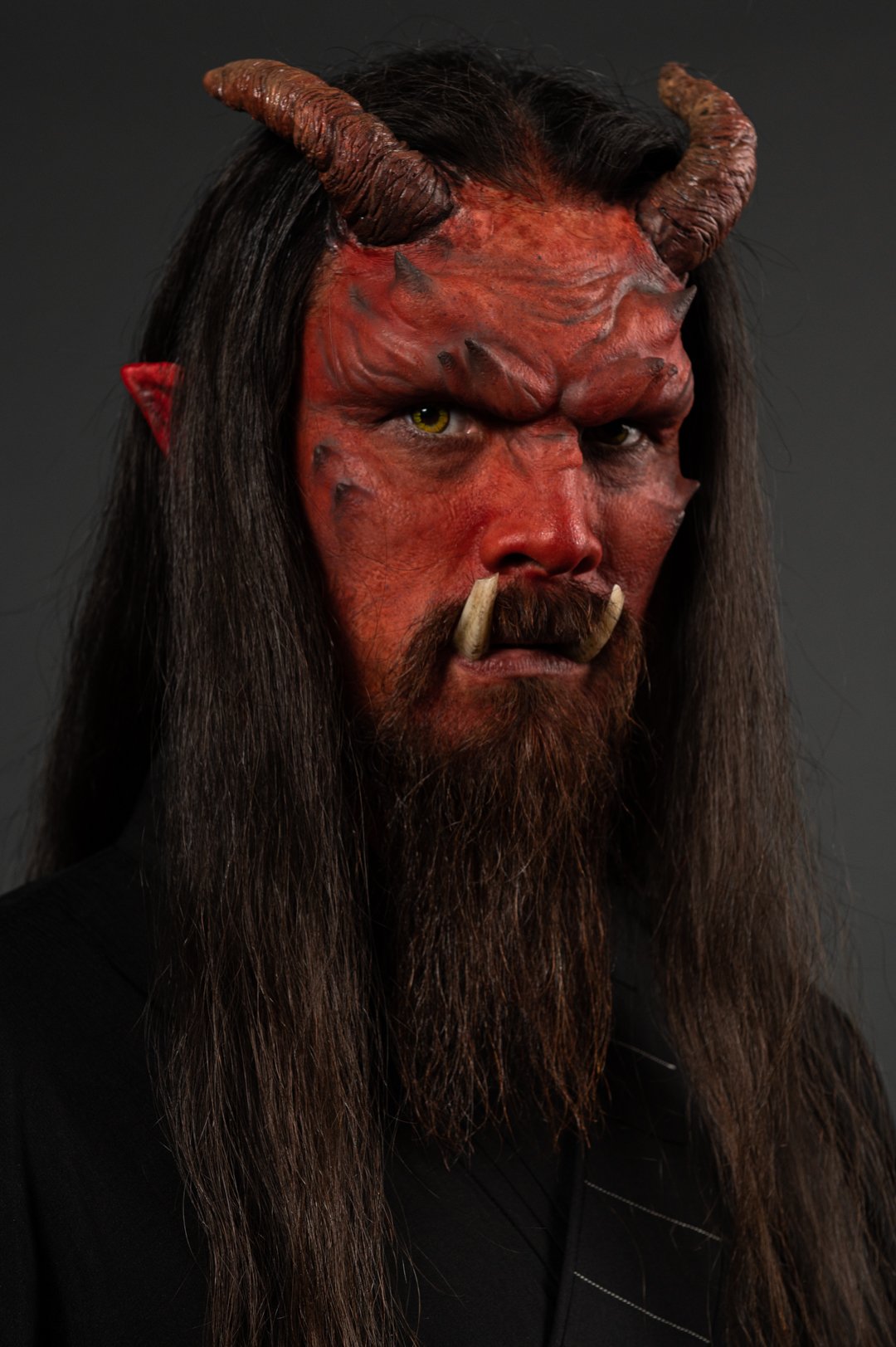
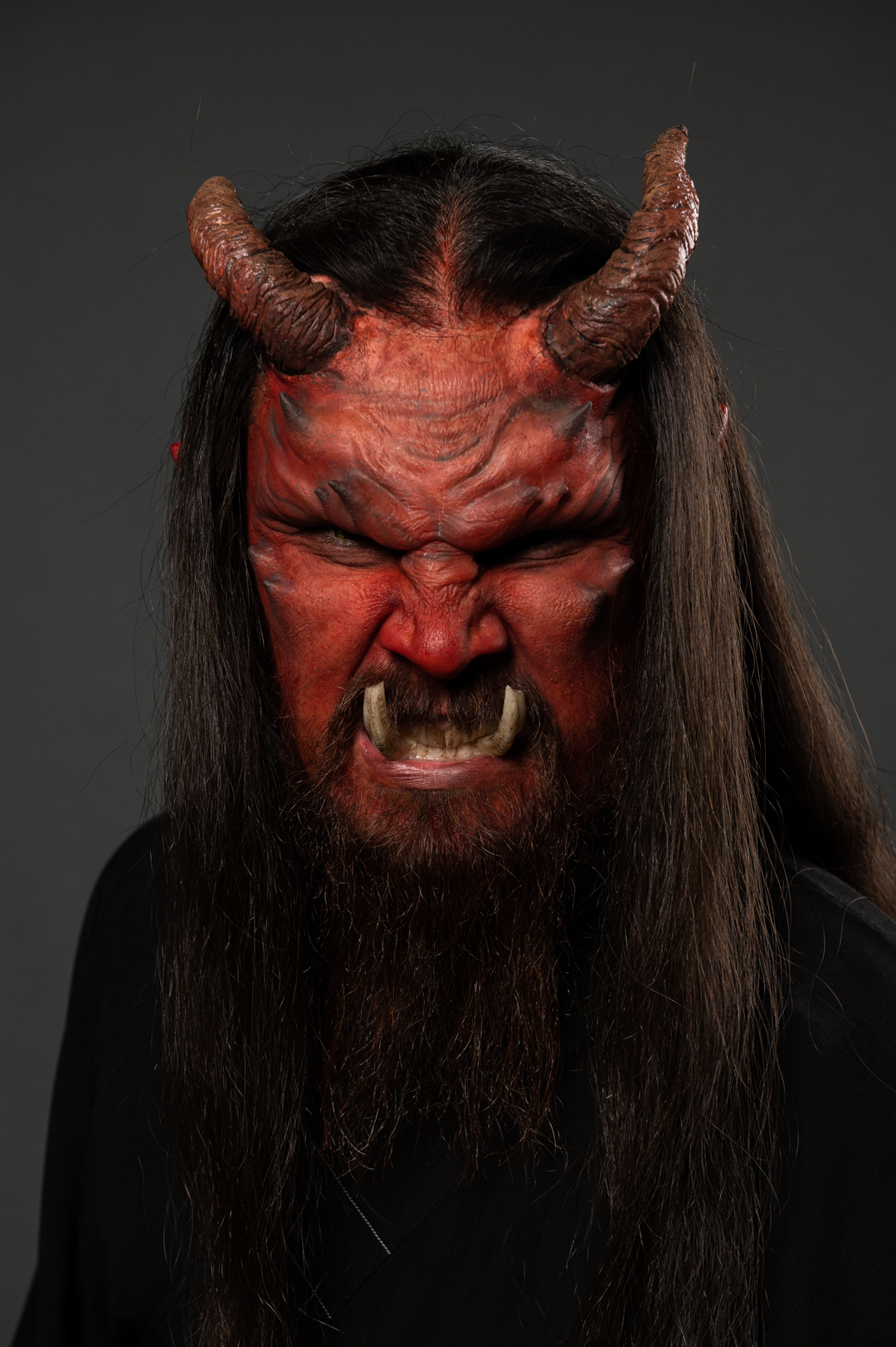
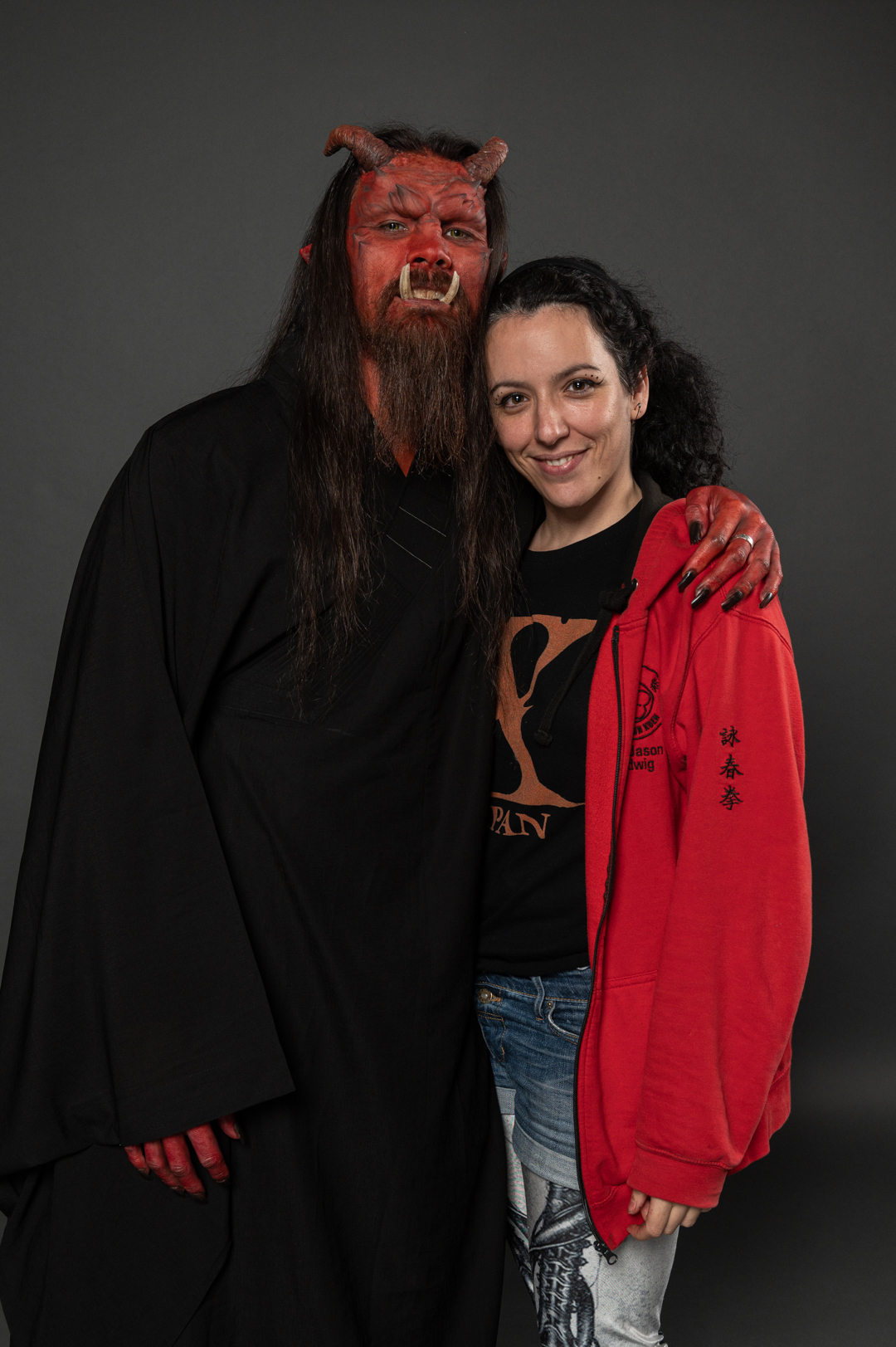
Off With His Head
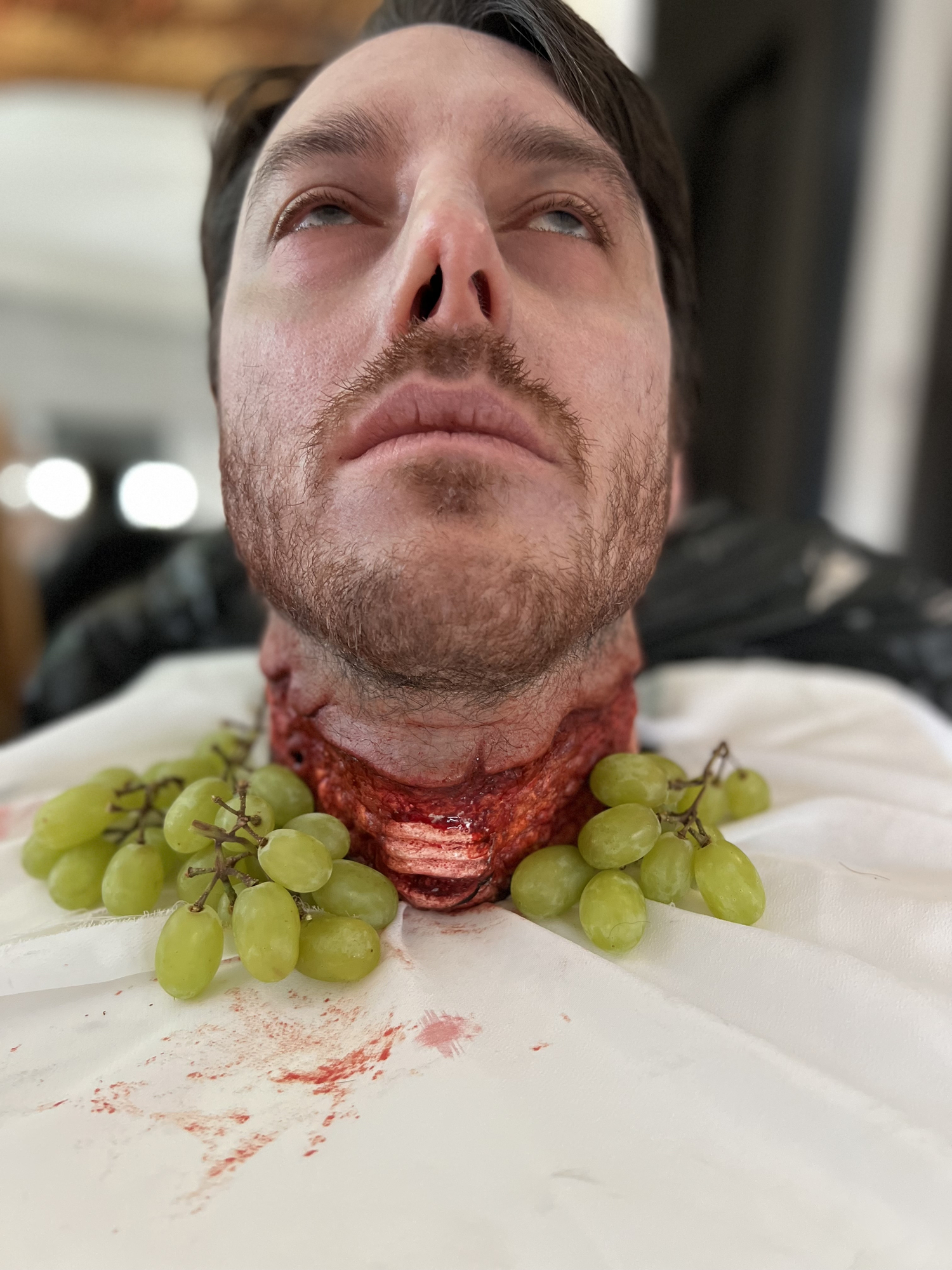
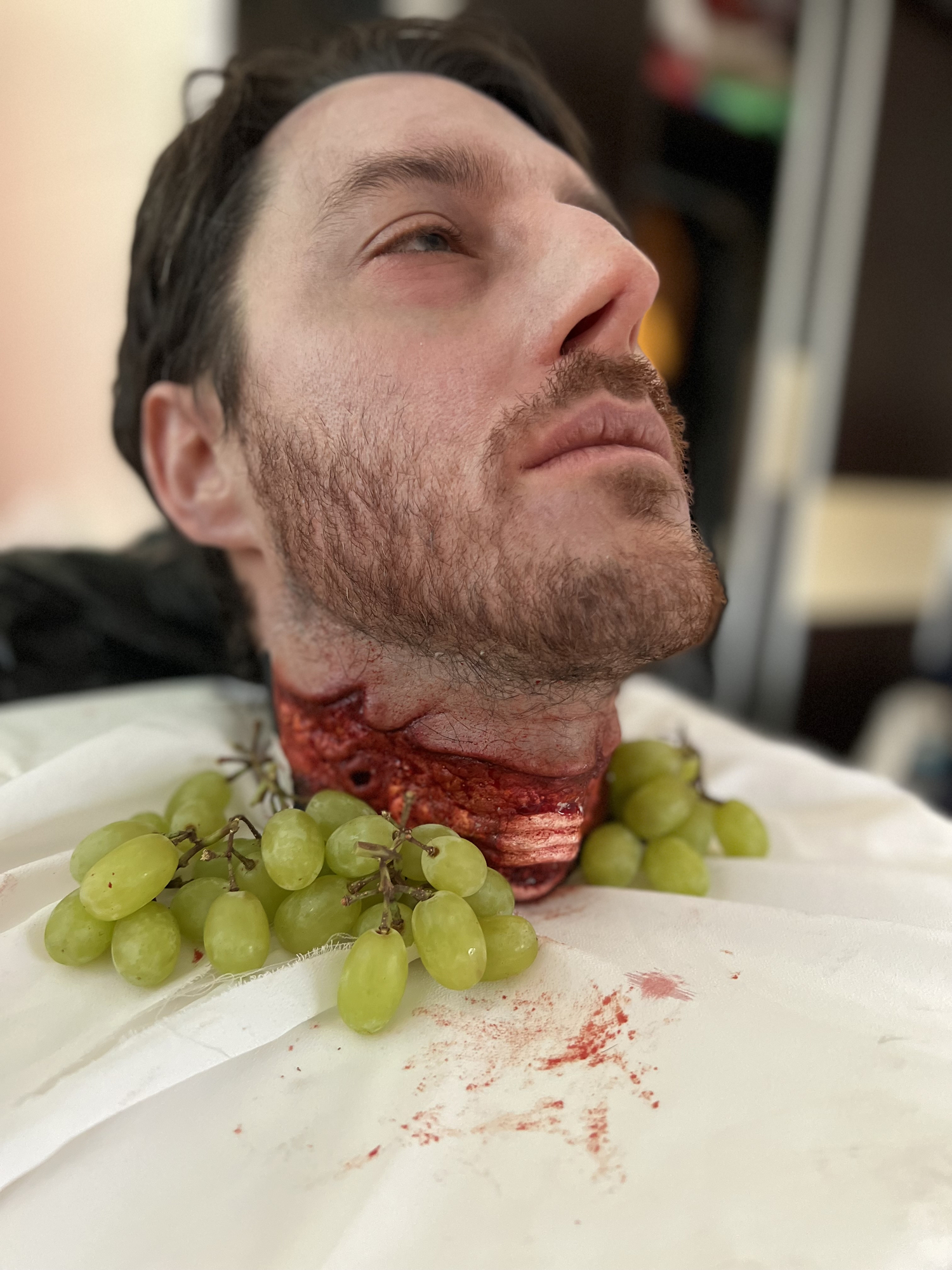
Off with his head, a silicone neck prosthetic to create an illusion off a decapitated head served on a plate / table.
Punk Rock Demon Sfx Character
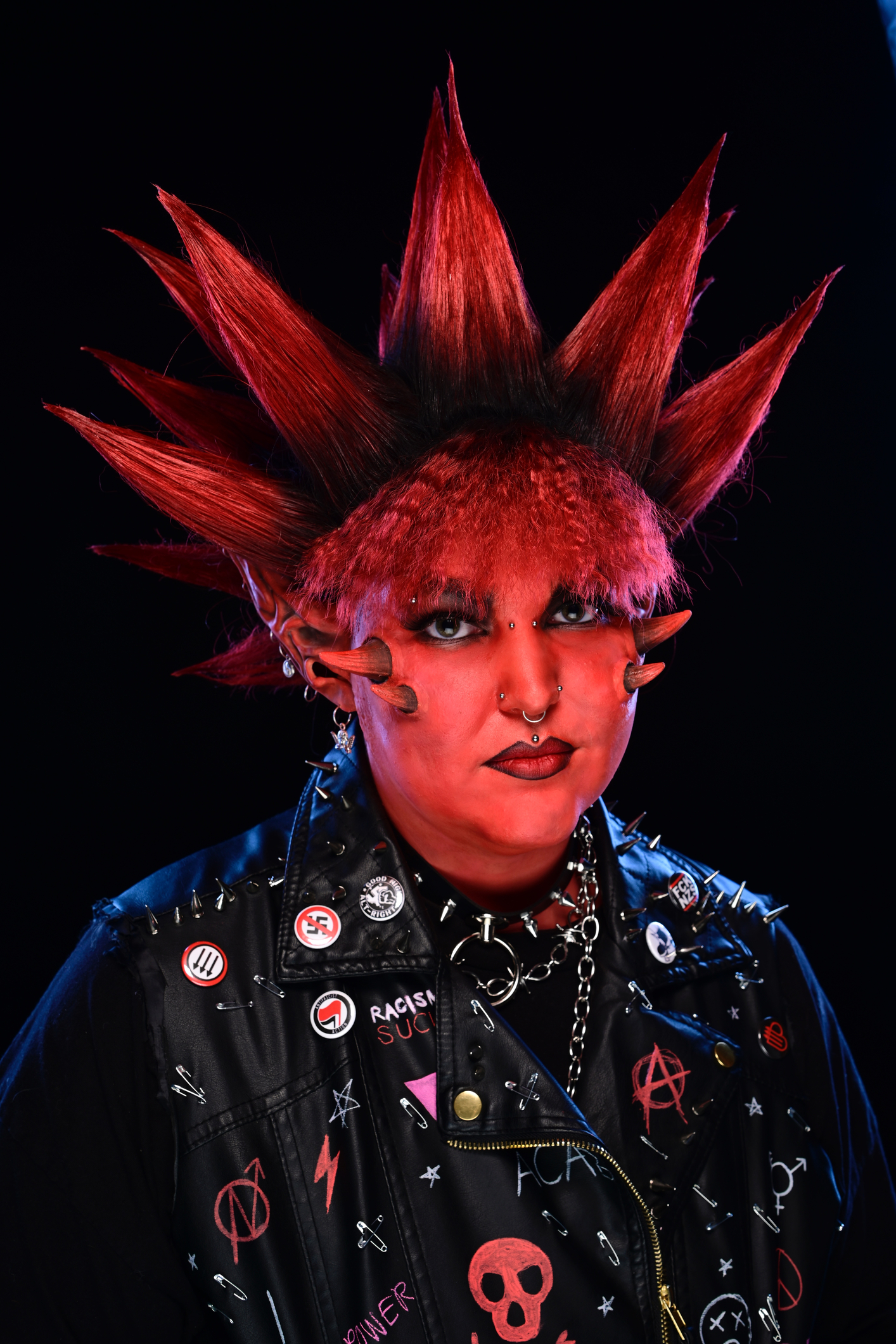
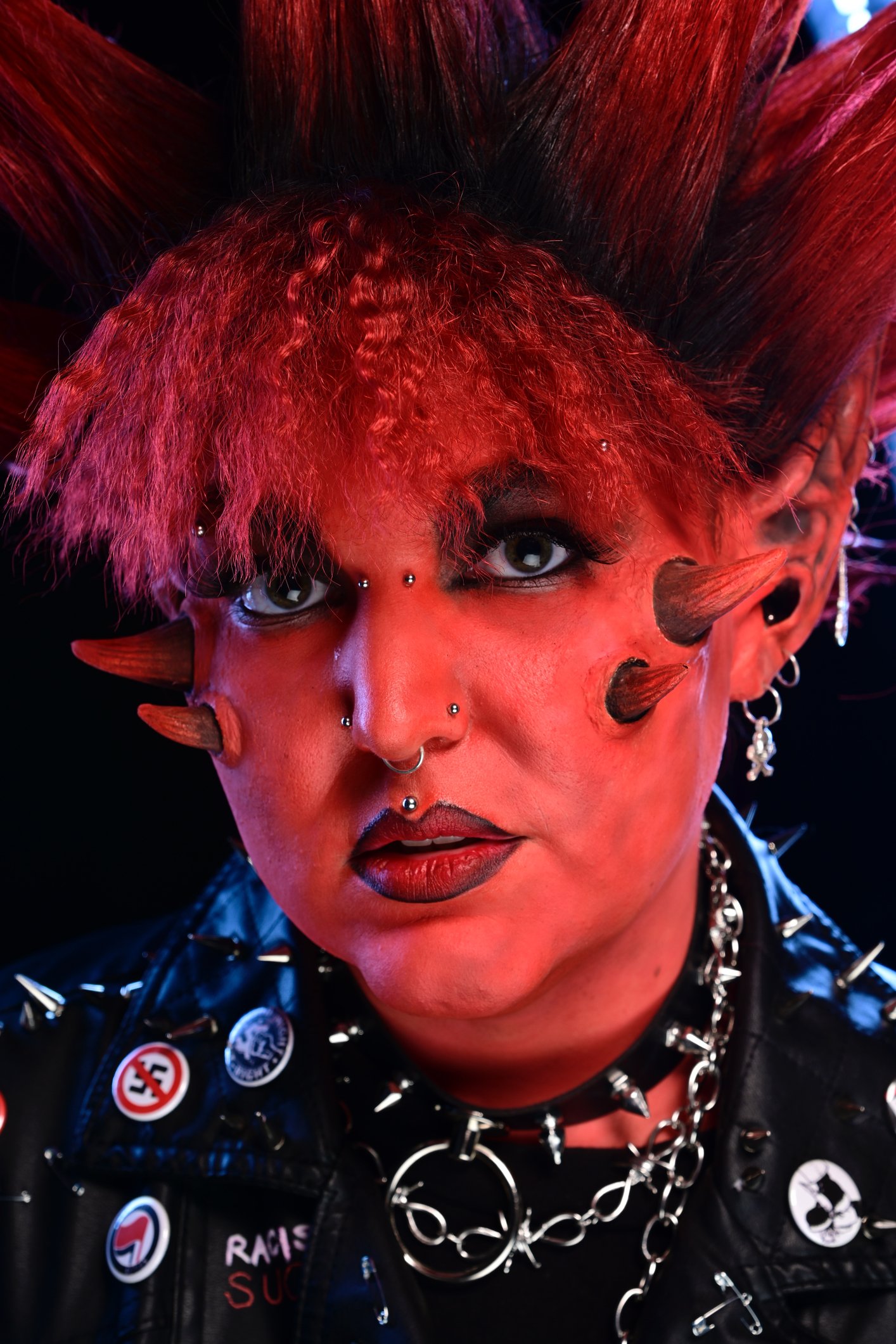
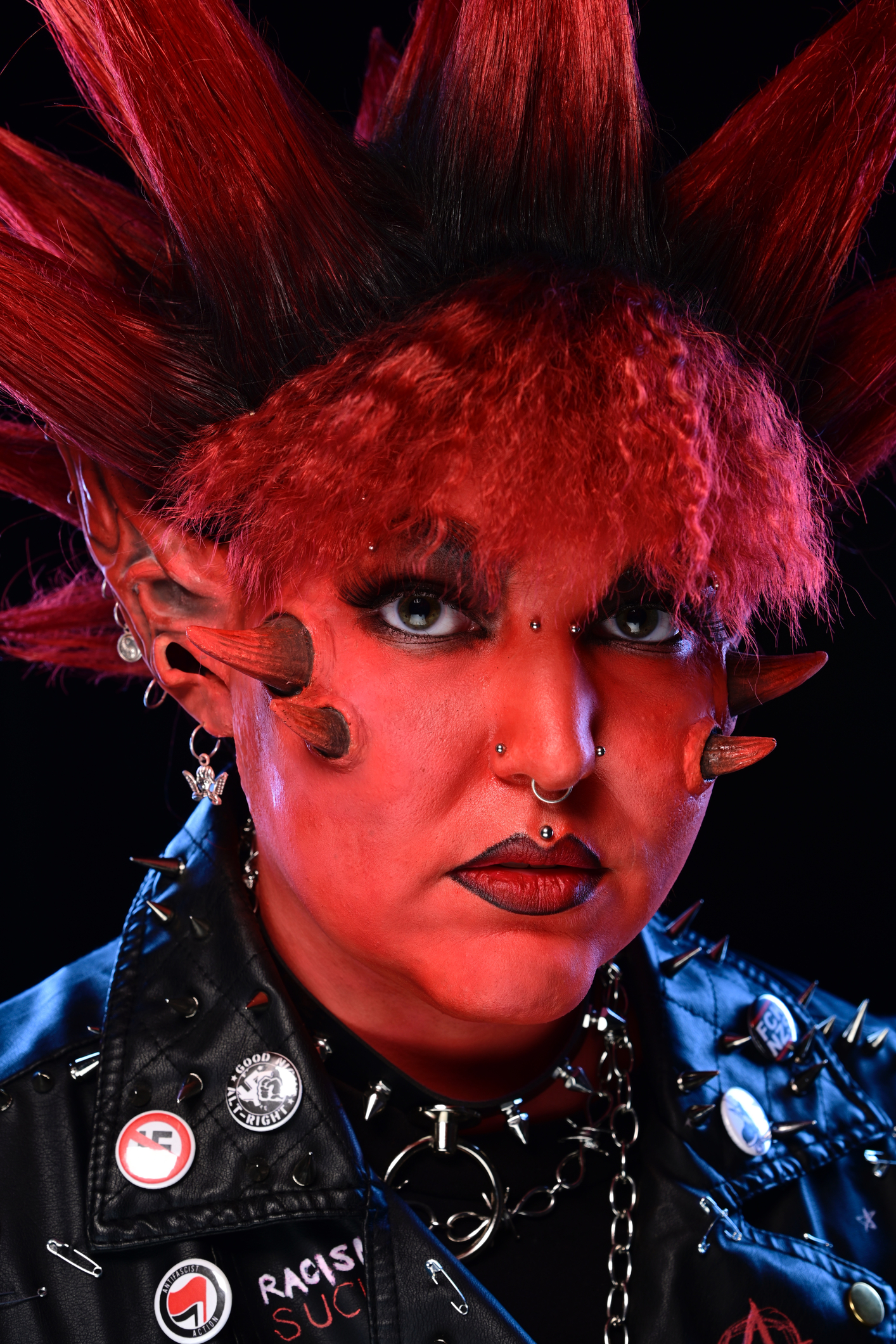