Best Of
Re: Learning past 40, looking for new friends on new paths.
Hi Shane. I'm much in the same boat as you. Being nearly 39 I feel like I'm playing catch up after years of being an onlooker and admirer of practical fx just in the last year been learning how to sculpt, mold, cast and paint.
It's incredibly rewarding/ frustrating and so thankful for the stan winston school as a valuable resource to turn to when learning new disciplines.
I've got a good handle on making latex masks so about try try my first silicone creature project.
Best of luck on your journey and look forward to seeing your work
https://www.instagram.com/porkpiesamurai/
It's incredibly rewarding/ frustrating and so thankful for the stan winston school as a valuable resource to turn to when learning new disciplines.
I've got a good handle on making latex masks so about try try my first silicone creature project.
Best of luck on your journey and look forward to seeing your work
https://www.instagram.com/porkpiesamurai/
Learning past 40, looking for new friends on new paths.
I just signed up for Courses, am staring with the basics of design. Over 30 years ago I was an 8 year old kid addicted to Horror, and Fangoria, I dreamt of working on creatures and movies. Spent my life on different paths but always kept my love of art and horror.
I am now ready to explore my capabilities and learn the craft of creature design and horror effects. I feel my 40 years of consuming horror, pop culture, and art can pay off finding me a place in the industry.
Im looking for friends and contacts to share the journey with, looking for adults like my self new to the industry, comment here if you are on a new path, what are you starting with? what brought you to this path and how long have you wanted to be here?
I am now ready to explore my capabilities and learn the craft of creature design and horror effects. I feel my 40 years of consuming horror, pop culture, and art can pay off finding me a place in the industry.
Im looking for friends and contacts to share the journey with, looking for adults like my self new to the industry, comment here if you are on a new path, what are you starting with? what brought you to this path and how long have you wanted to be here?
Bib Fortuna -Latex Bust
Heres my finished Bib Fortuna latex piece. Sculpted in Wed and cast in latex, painted with my trusty Iwata cm-sb with Tim Gores bloodline. Fourth Seal eyes (which I had some trouble getting inside the eye) and dental acrylic teeth.
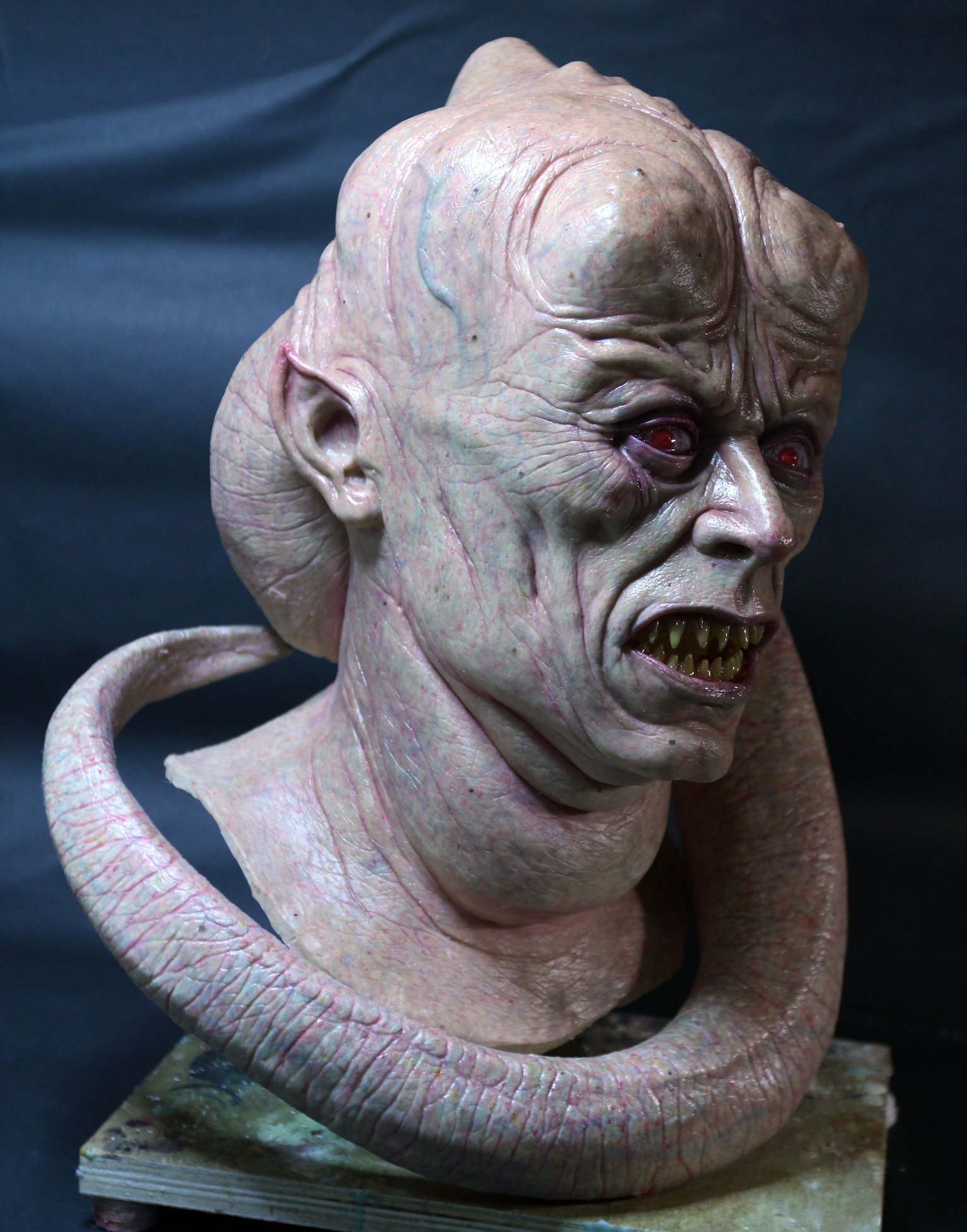
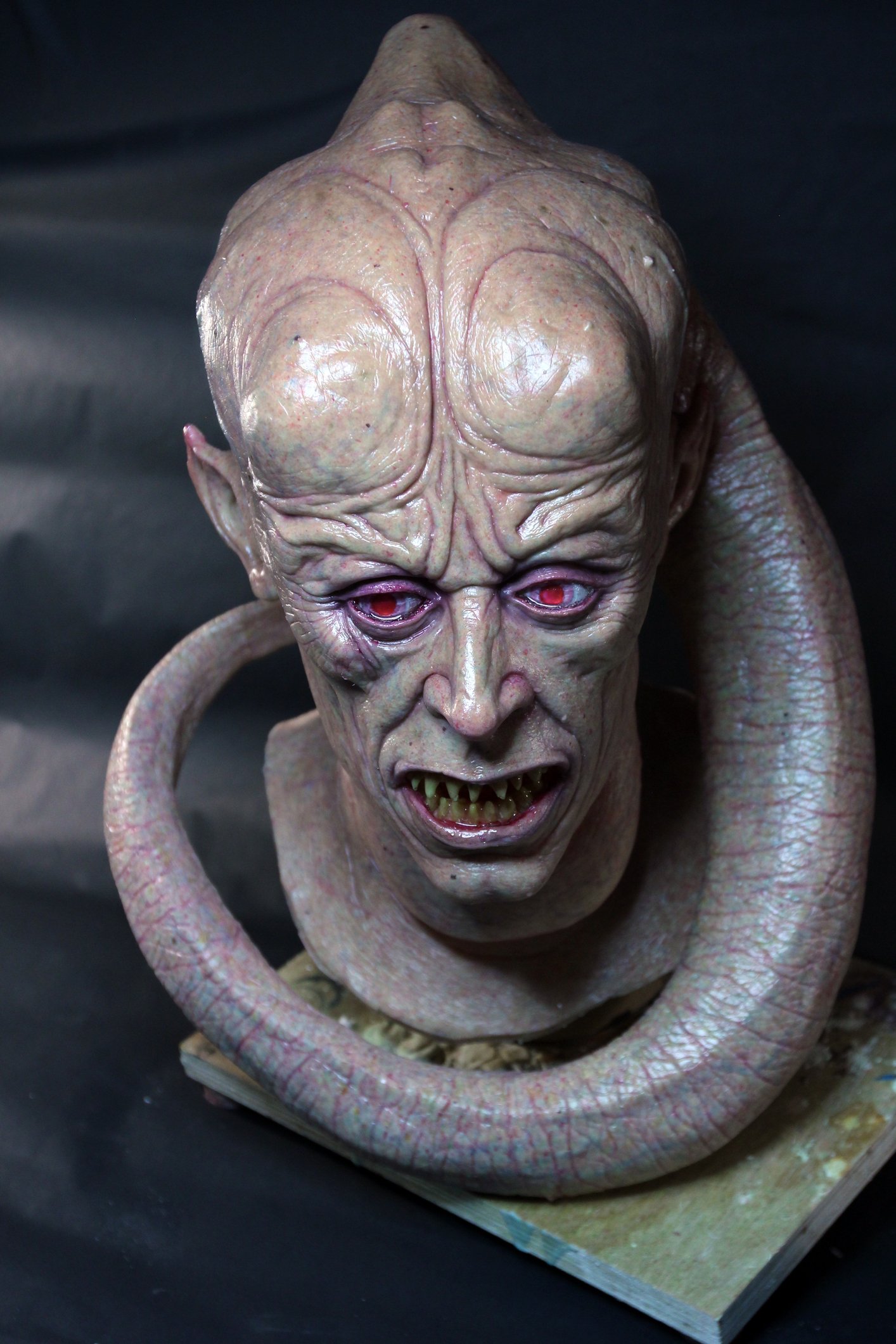
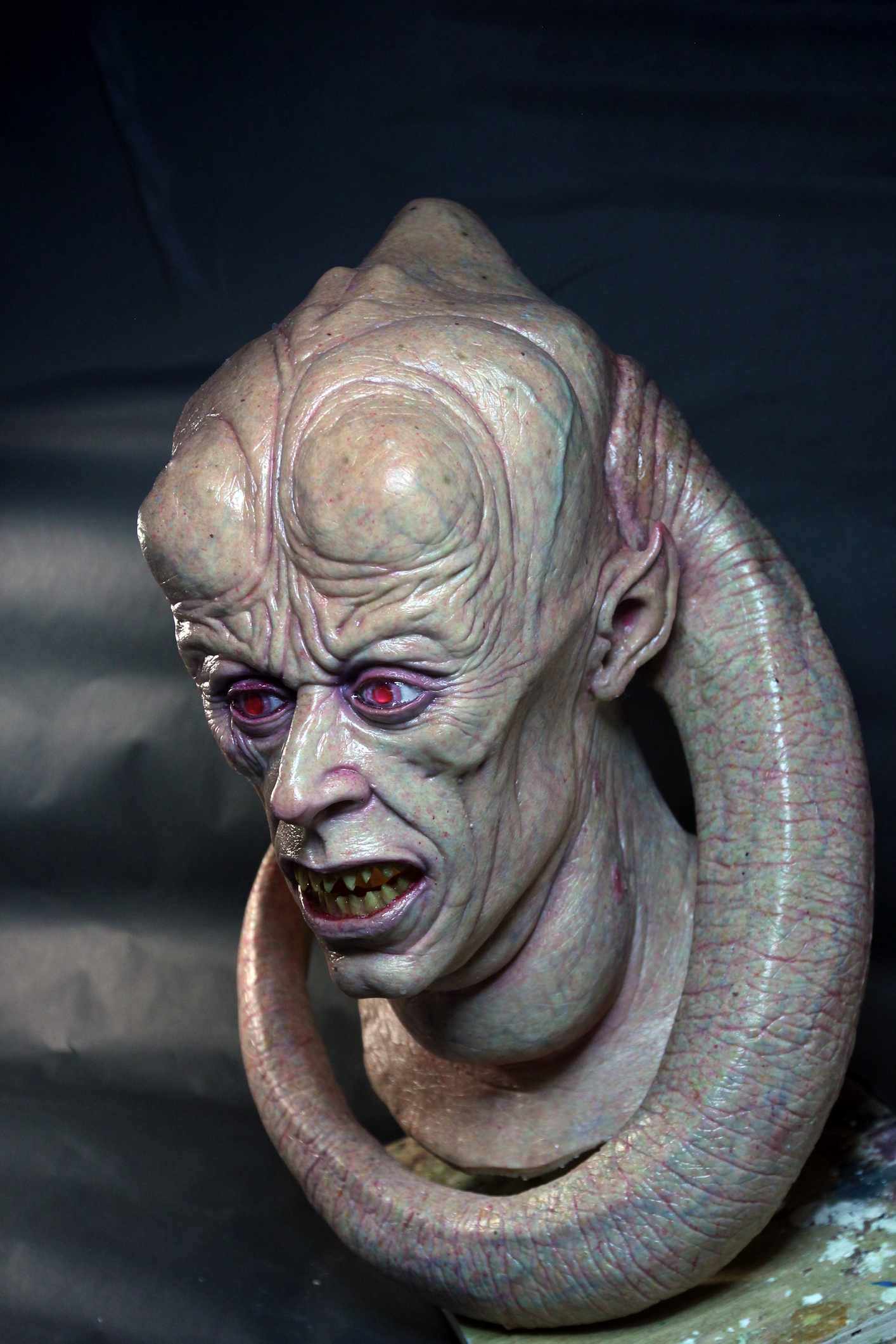
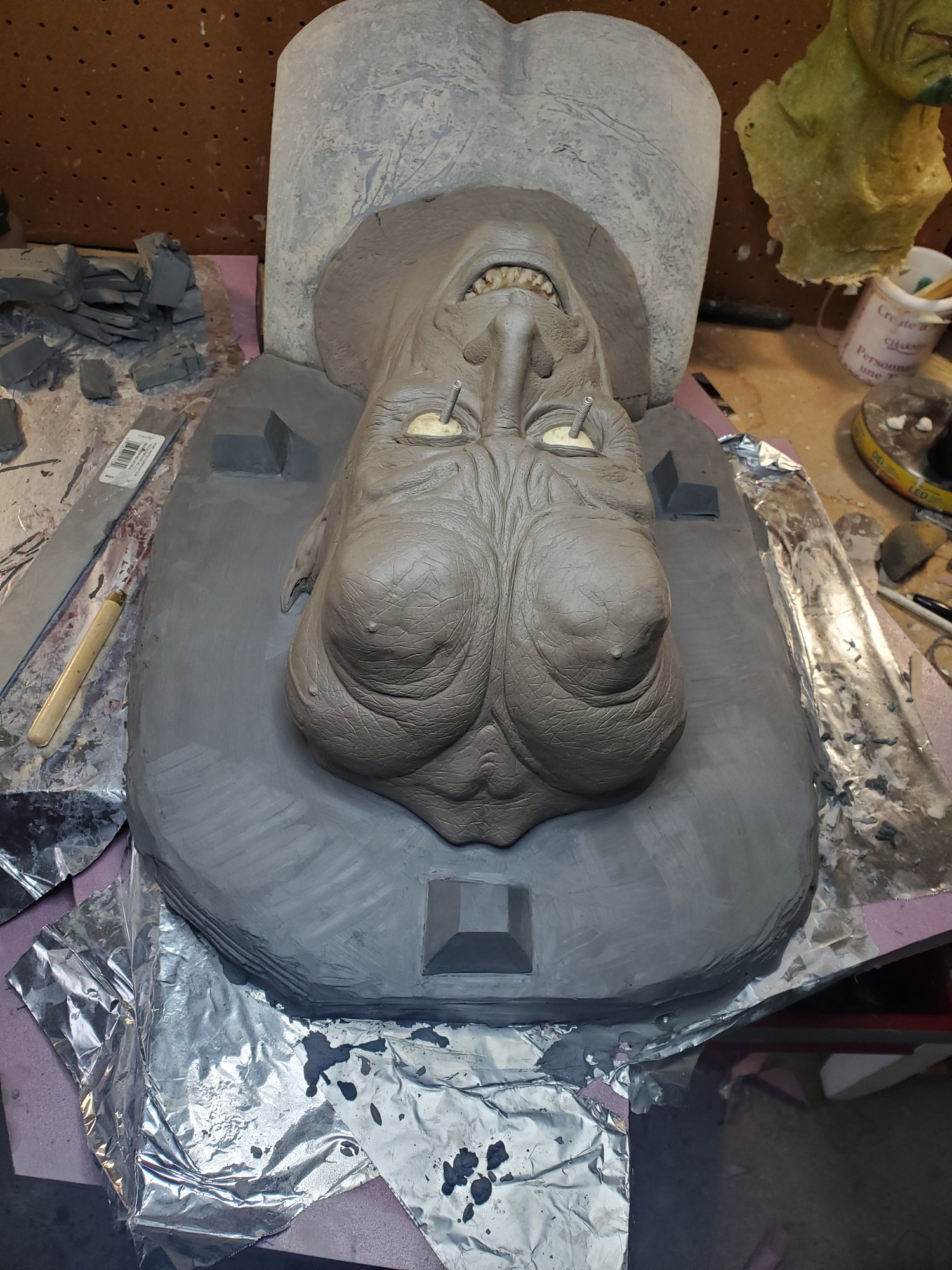

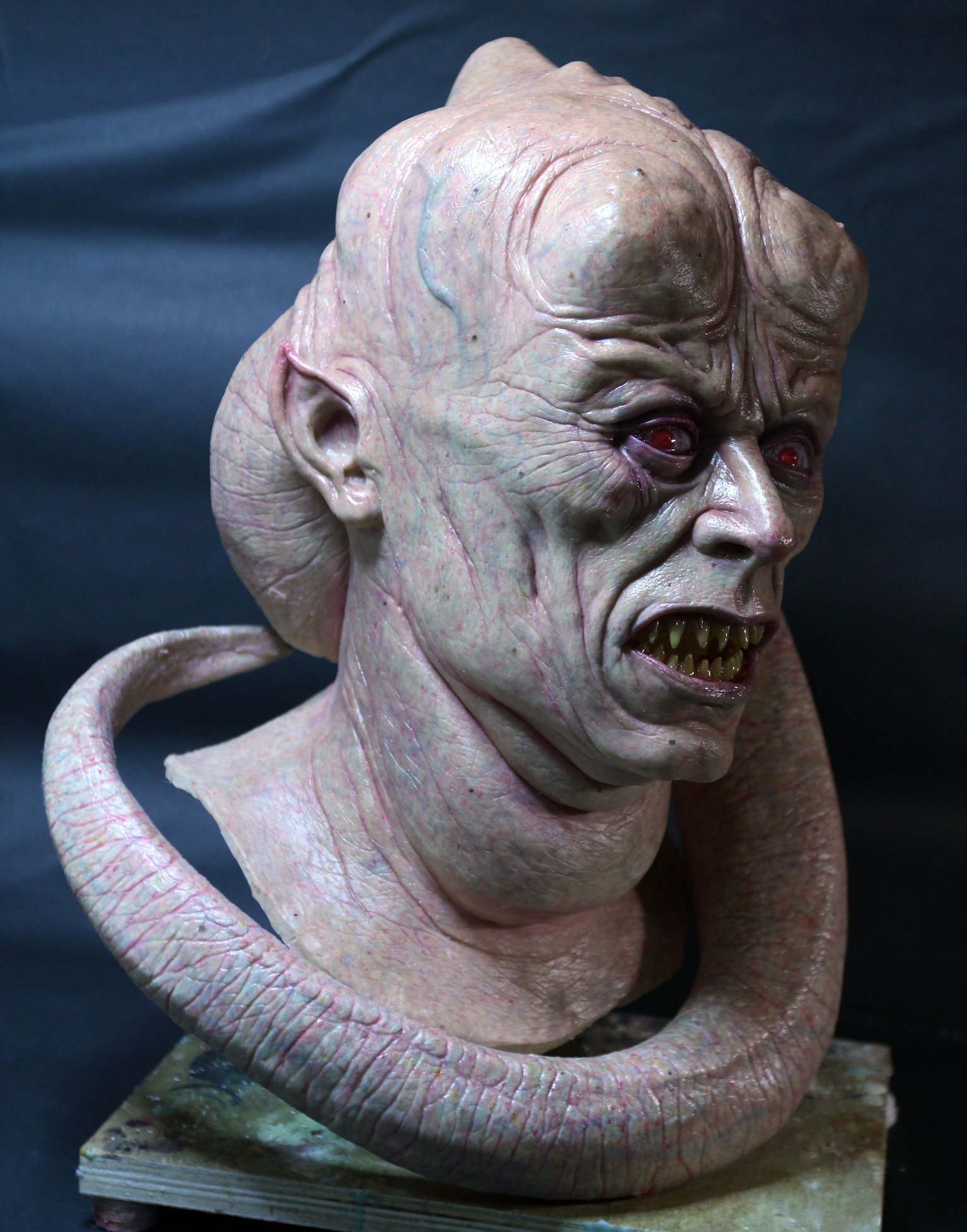
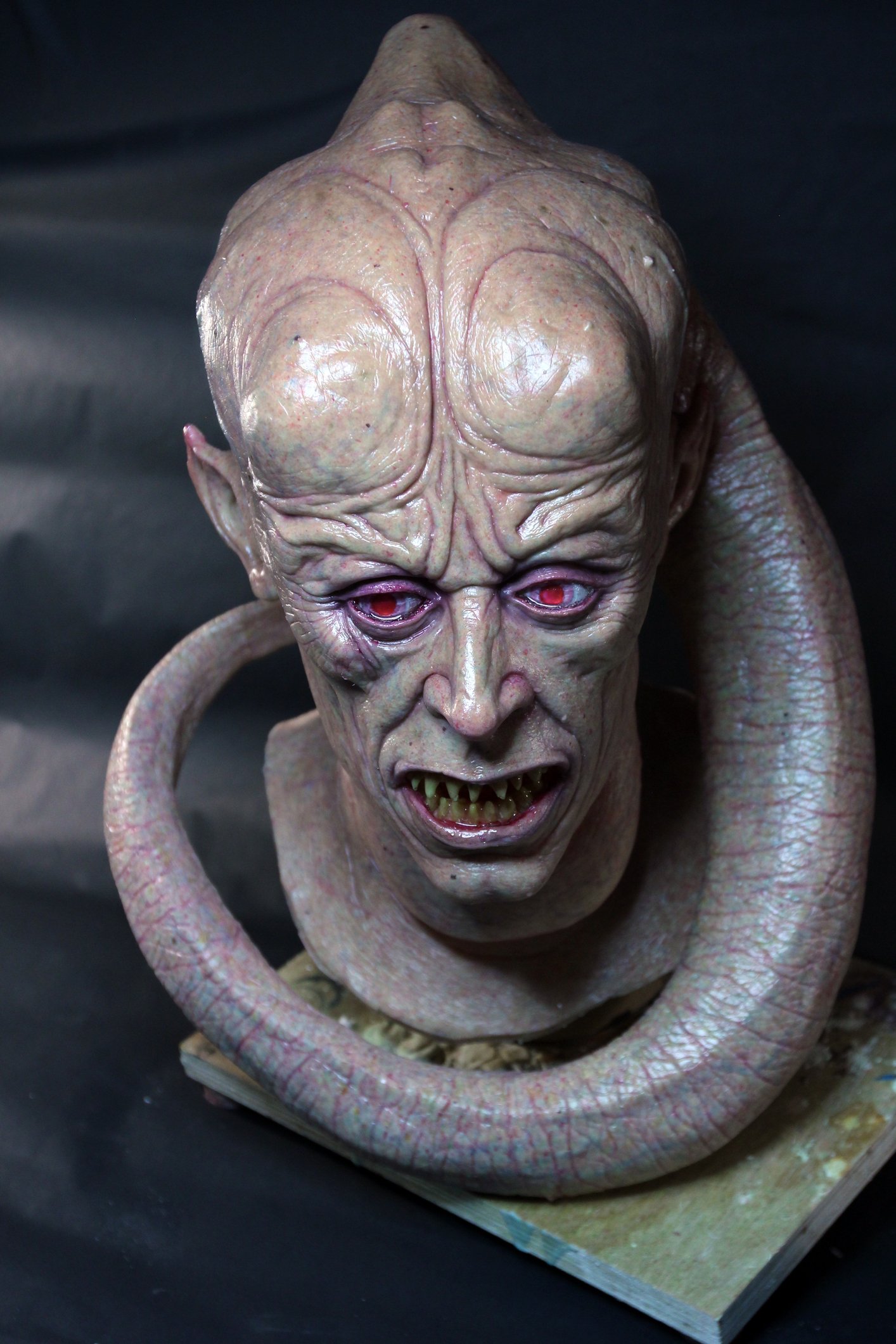
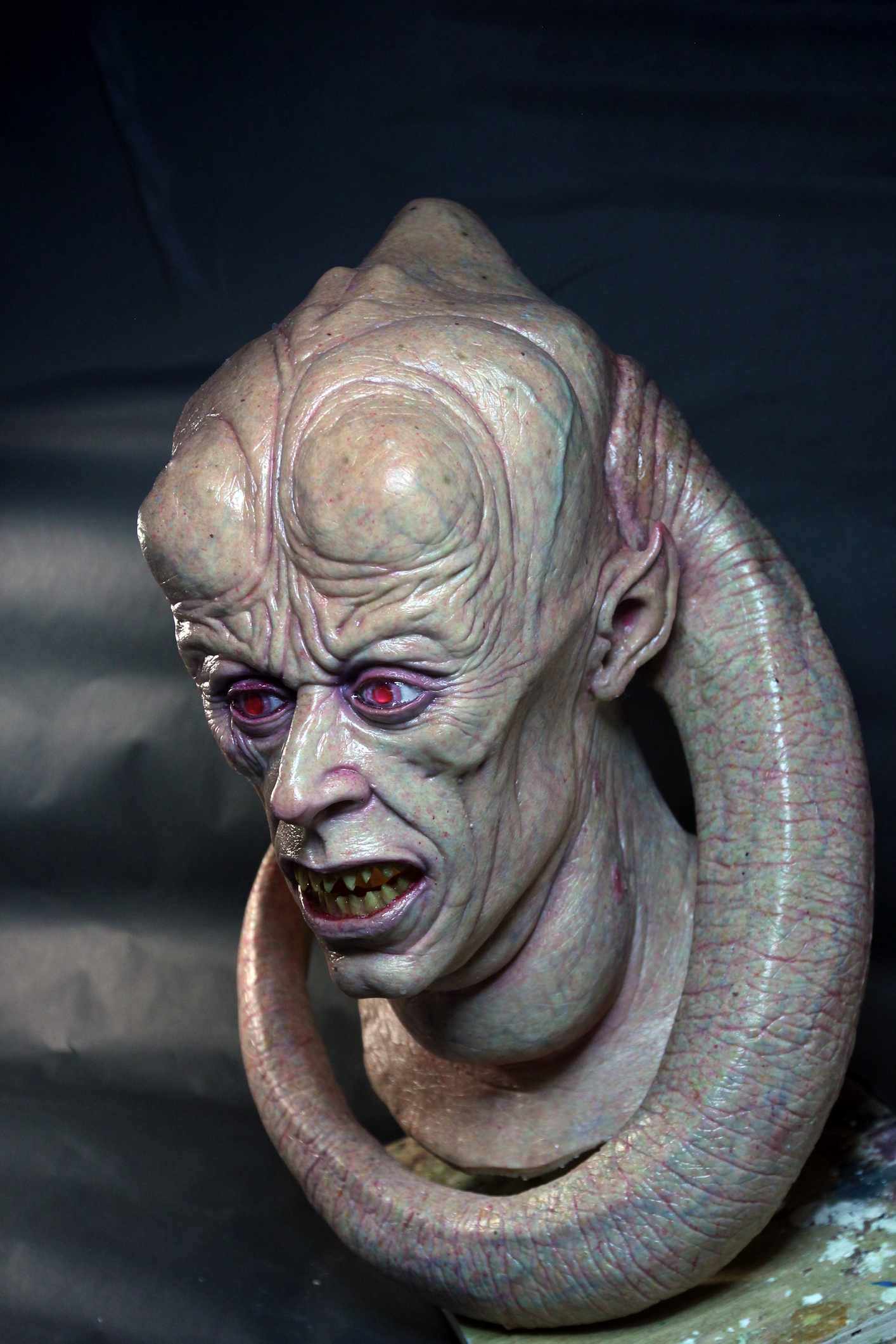
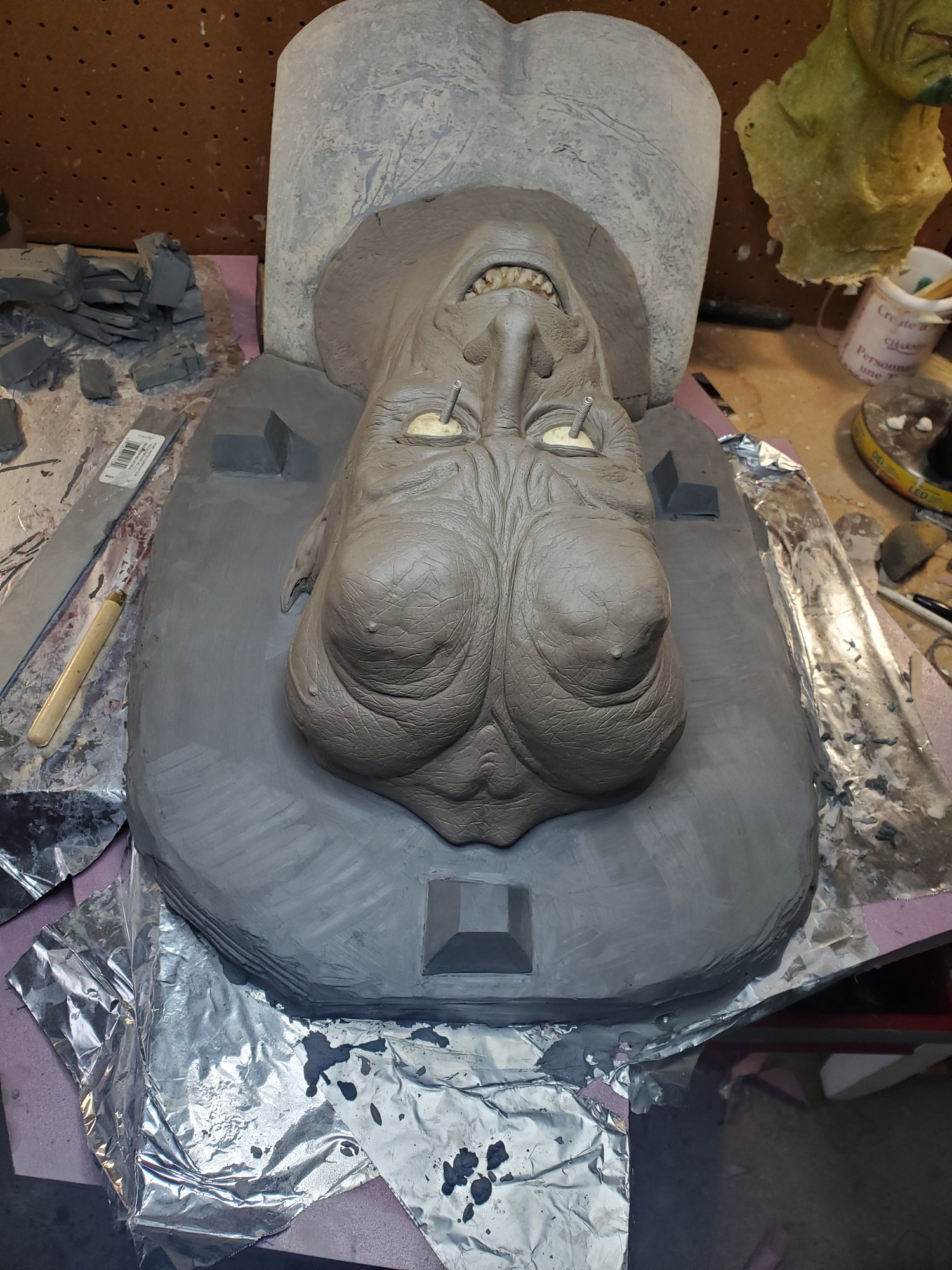

Re: Sculpting Head Core in Silicon Mask Making Part 2: Finishing the Epoxy & Fiberglass Mold
Hi Brian,
I was able to find one location in the UK that sells an armature/core for silicone mask making.
https://www.neillsmaterials.co.uk/product/silicone-mask-armature/
The price looks reasonable, considering the expense of making your own. With a bit more searching you may be able to find others.
We don't have a course on silicone mask cores at the moment. The silicone mask-making course does cover a lot of information about the core, so with a bit of research, you should be able to make your own from a lifecast. I don't know of any resources that cover the full design and construction of a silicone mask core. But with a bit of google/youtube research, and possibly watching this course again, you should be able to design and build your own.
The basic process (as I might approach it) is as follows:
Hope that helps!
/Chris
I was able to find one location in the UK that sells an armature/core for silicone mask making.
https://www.neillsmaterials.co.uk/product/silicone-mask-armature/
The price looks reasonable, considering the expense of making your own. With a bit more searching you may be able to find others.
We don't have a course on silicone mask cores at the moment. The silicone mask-making course does cover a lot of information about the core, so with a bit of research, you should be able to make your own from a lifecast. I don't know of any resources that cover the full design and construction of a silicone mask core. But with a bit of google/youtube research, and possibly watching this course again, you should be able to design and build your own.
The basic process (as I might approach it) is as follows:
- Make a silicone or alginate life cast from the shoulders up, with a plaster bandage shell.
- Pour melted clay into the mold to create a positive bust
- Simplify/remove the ears, leaving a small mound where the ears were to provide some space for the wearer's ears.
- Smooth out and simplify the surface, and remove clay in areas where you want the fit to be snugger.
- Simplify the area around the eyes so your final mask can blend properly
- Sculpt the mouth in a slightly open position with a small shallow cavity between the lips
- Sculpt in some keys and a flange so the core could socket into and be centered/supported by the final outer mold
- Mold and cast in epoxy and fiberglass.
Hope that helps!
/Chris
Great opportunity for a Mask artist to create a wearable Zombie mask for special TV series promo
Hi..I'm looking for an artist able to create a wearable zombie mask that will be used by an artist to promote a new TV series. The challenges is that I need it by July 21st in Miami. Mask must be real, unique, not overloaded.
If you are interested, please contact me at guifanelli@msn.com
Thank you
If you are interested, please contact me at guifanelli@msn.com
Thank you
Re: Horns
This depends a bit on the size, shape, and weight of the horns. Smaller and lighter horns can be glued on, and you can even paint a bit of latex around the base to help seal/blend them in. A glue like E6000 should do the trick.
Heavier horns may require more support, and for that, you can either have a small plate under the mask they attach to, a headband-like plate for both horns, or a full plate over the top of the head on the inside. I would use a couple of small bolts through the plate to lock into each horn (you can set a couple of threaded inserts into each horn) so it can't twist, then hold the plate in place with some adhesive like E6000 if you want it to be more of a permanent addition.
The plate can be thick vacuum-formed plastic, fiberglass, thermoplastic, etc.
If the horns don't match the mask well, as you mentioned it's a mix and match situation, you may be able to use latex and cotton or tissue paper to make a paper mache sculpting material to add small details around the horn. It can be pigmented by mixing in acrylic paints. Then paint/finish as desired.
Hope that helps!
/Chris
Heavier horns may require more support, and for that, you can either have a small plate under the mask they attach to, a headband-like plate for both horns, or a full plate over the top of the head on the inside. I would use a couple of small bolts through the plate to lock into each horn (you can set a couple of threaded inserts into each horn) so it can't twist, then hold the plate in place with some adhesive like E6000 if you want it to be more of a permanent addition.
The plate can be thick vacuum-formed plastic, fiberglass, thermoplastic, etc.
If the horns don't match the mask well, as you mentioned it's a mix and match situation, you may be able to use latex and cotton or tissue paper to make a paper mache sculpting material to add small details around the horn. It can be pigmented by mixing in acrylic paints. Then paint/finish as desired.
Hope that helps!
/Chris
Re: Dragon Skin Help
Here is the official product page for Dragon Skin. Smooth-On is great about providing detailed documentation on all their materials.
https://www.smooth-on.com/products/dragon-skin-10-medium/
Technical sheet: https://www.smooth-on.com/tb/files/DRAGON_SKIN_SERIES_TB.pdf
While they do not have specific layer times listed for Dragon Skin Medium, they do mention times for Rebound 25: https://www.smooth-on.com/products/rebound-25/
"Let the first coat dry for 60 minutes at room temperature until it becomes “tacky” before adding the next coat. “Tacky” is defined as sticky to the touch, but does not come off onto your gloved finger. Once “tacky”, you are ready to apply the next layer. Tack-time can be reduced with mild heat (hair dryer or heat gun). Repeat until the necessary mold thickness is achieved."
Since they are both platinum cure silicones with roughly the same pot life and cure time you could use the data for Rebound 25 as a starting point.
/Chris
https://www.smooth-on.com/products/dragon-skin-10-medium/
Technical sheet: https://www.smooth-on.com/tb/files/DRAGON_SKIN_SERIES_TB.pdf
While they do not have specific layer times listed for Dragon Skin Medium, they do mention times for Rebound 25: https://www.smooth-on.com/products/rebound-25/
"Let the first coat dry for 60 minutes at room temperature until it becomes “tacky” before adding the next coat. “Tacky” is defined as sticky to the touch, but does not come off onto your gloved finger. Once “tacky”, you are ready to apply the next layer. Tack-time can be reduced with mild heat (hair dryer or heat gun). Repeat until the necessary mold thickness is achieved."
Since they are both platinum cure silicones with roughly the same pot life and cure time you could use the data for Rebound 25 as a starting point.
/Chris
Re: Dragon Skin Help
Just so you know..in doing layers with the Dragon Skin MEDIUM formula...the wait time between layers is about 30 minutes...and a couple of squirts of ThiVex thickner will make it good and peanut buttery thick to stay vertical if needed