Best Of
Re: Question about making a Foam Latex Oven
Hi Stephen,
You can use anything from toaster ovens, electric ranges, or even heat guns to make a homemade foam oven.
Here are some quick tips: Keep it well insulated so the heat does not dissipate. Line the inside with reflective heat-resistant material so the heat bounces around, a fan to circulate the air is a big help, monitor the temperature with a thermometer to make sure you don't over cook or under cook your foam, when you first build it, check the temperature in a few locations to watch for hot/cold spots, always keep a fire extinguisher next to it, and never leave it unattended.
Also keep in mind that the size/distribution/number of molds you place in an oven can impact its performance.
Here's a quick video of a homemade build:
https://www.youtube.com/watch?v=NL4b02hlojc
Here is another DIY example:
http://tripleacosplay.com/2011/12/24/foam-latex-bake-oven/
Foam running guide:
http://www.monstermakers.com/files/PDFs/MMFoaminstructions.pdf
Best of luck!
/Chris
You can use anything from toaster ovens, electric ranges, or even heat guns to make a homemade foam oven.
Here are some quick tips: Keep it well insulated so the heat does not dissipate. Line the inside with reflective heat-resistant material so the heat bounces around, a fan to circulate the air is a big help, monitor the temperature with a thermometer to make sure you don't over cook or under cook your foam, when you first build it, check the temperature in a few locations to watch for hot/cold spots, always keep a fire extinguisher next to it, and never leave it unattended.
Also keep in mind that the size/distribution/number of molds you place in an oven can impact its performance.
Here's a quick video of a homemade build:
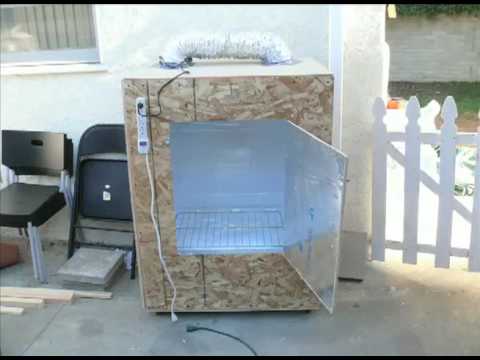
Here is another DIY example:
http://tripleacosplay.com/2011/12/24/foam-latex-bake-oven/
Foam running guide:
http://www.monstermakers.com/files/PDFs/MMFoaminstructions.pdf
Best of luck!
/Chris
The thing about a shark....
Shark's got lifeless eyes...like a doll's eyes...doesn't seem to be living...until he bites ya...and those eyes roll over white!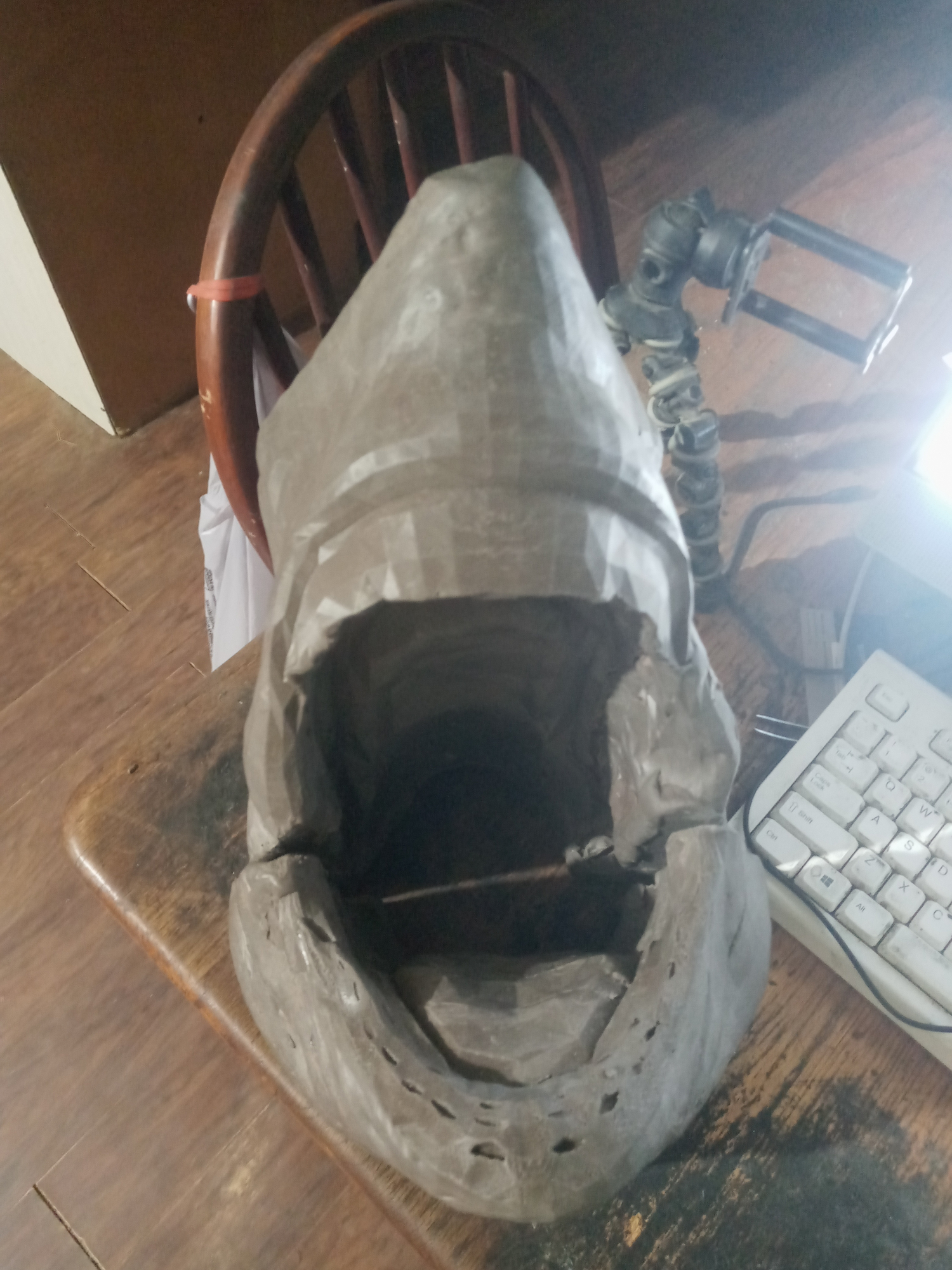
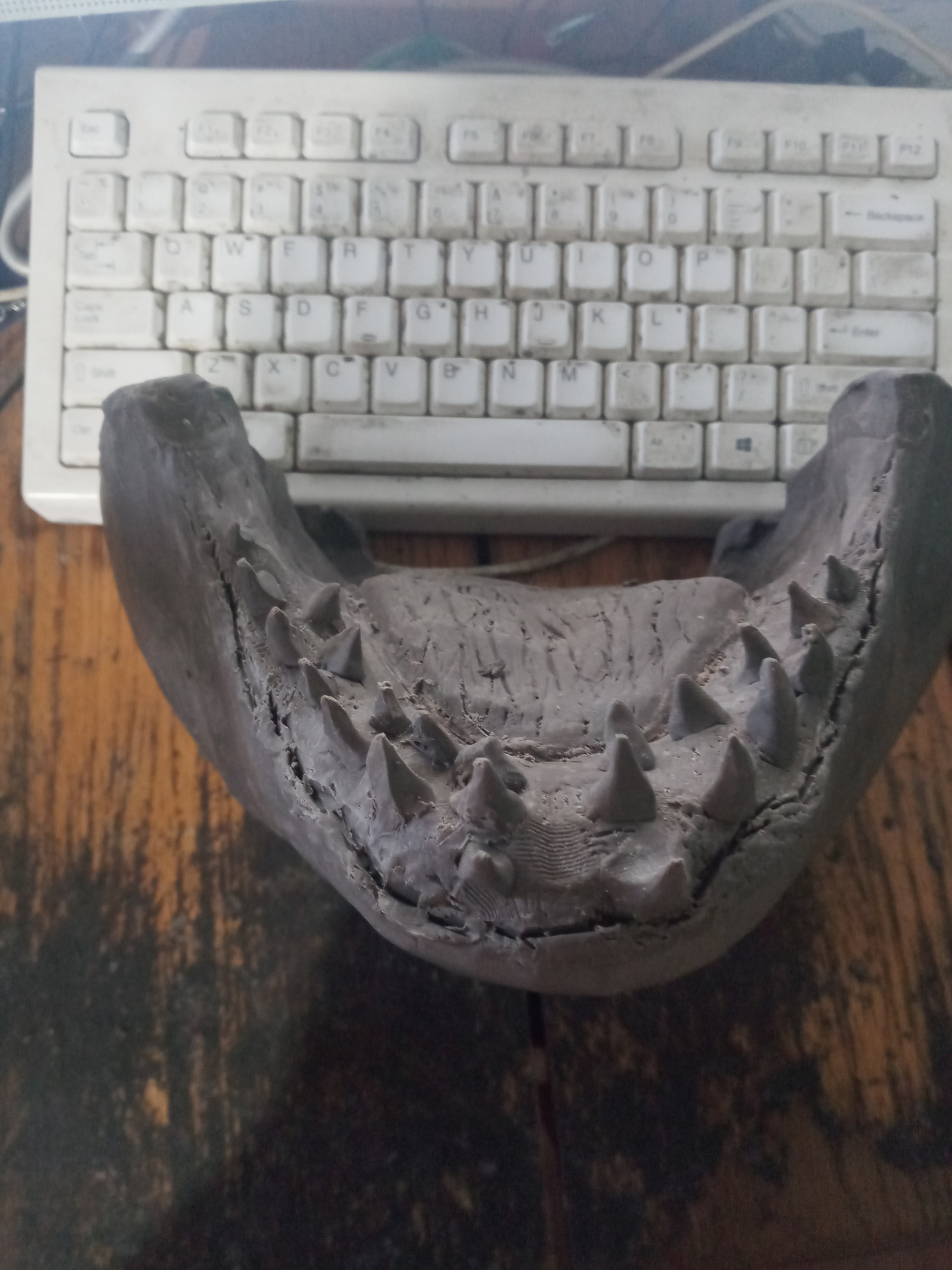
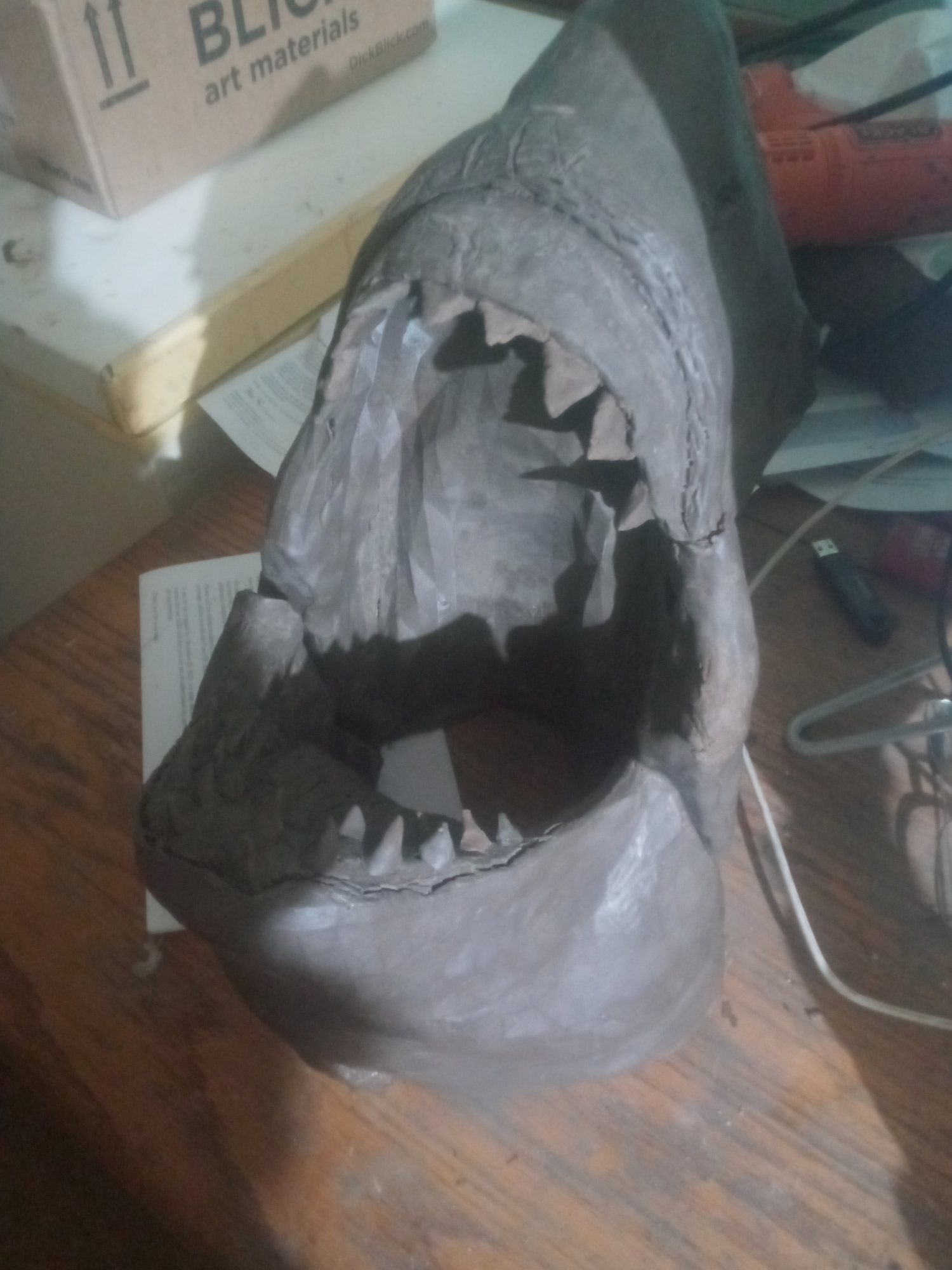
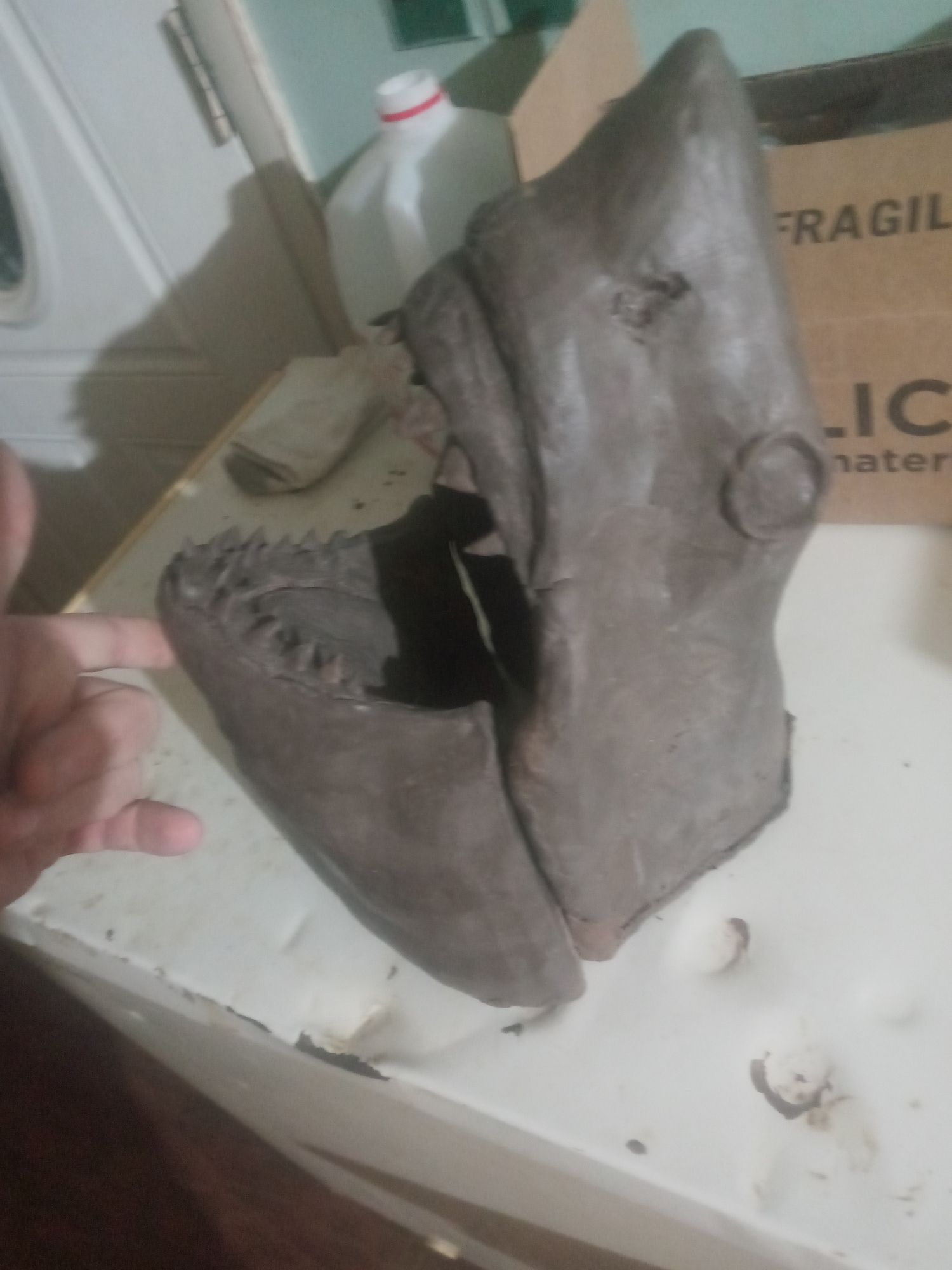
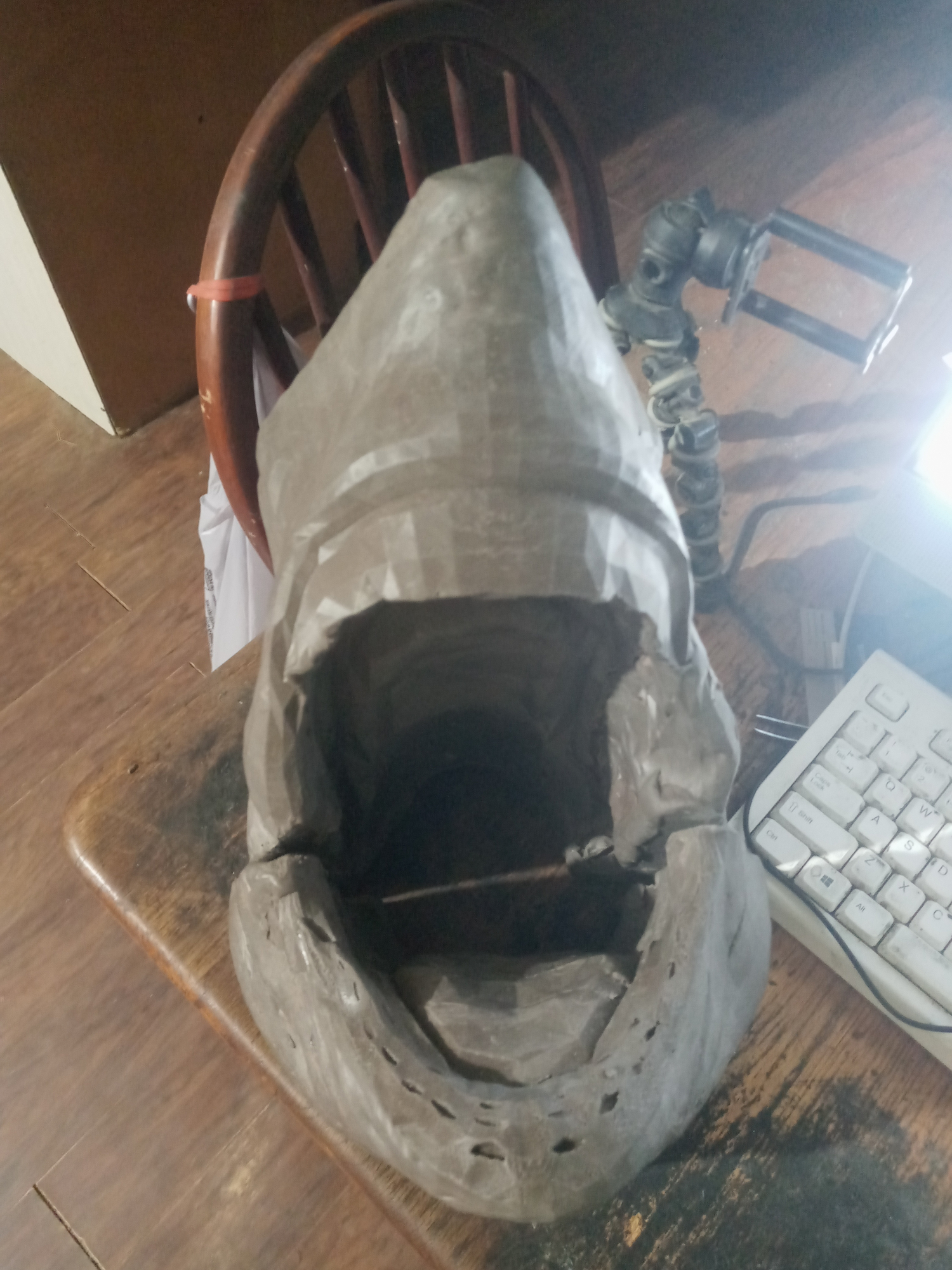
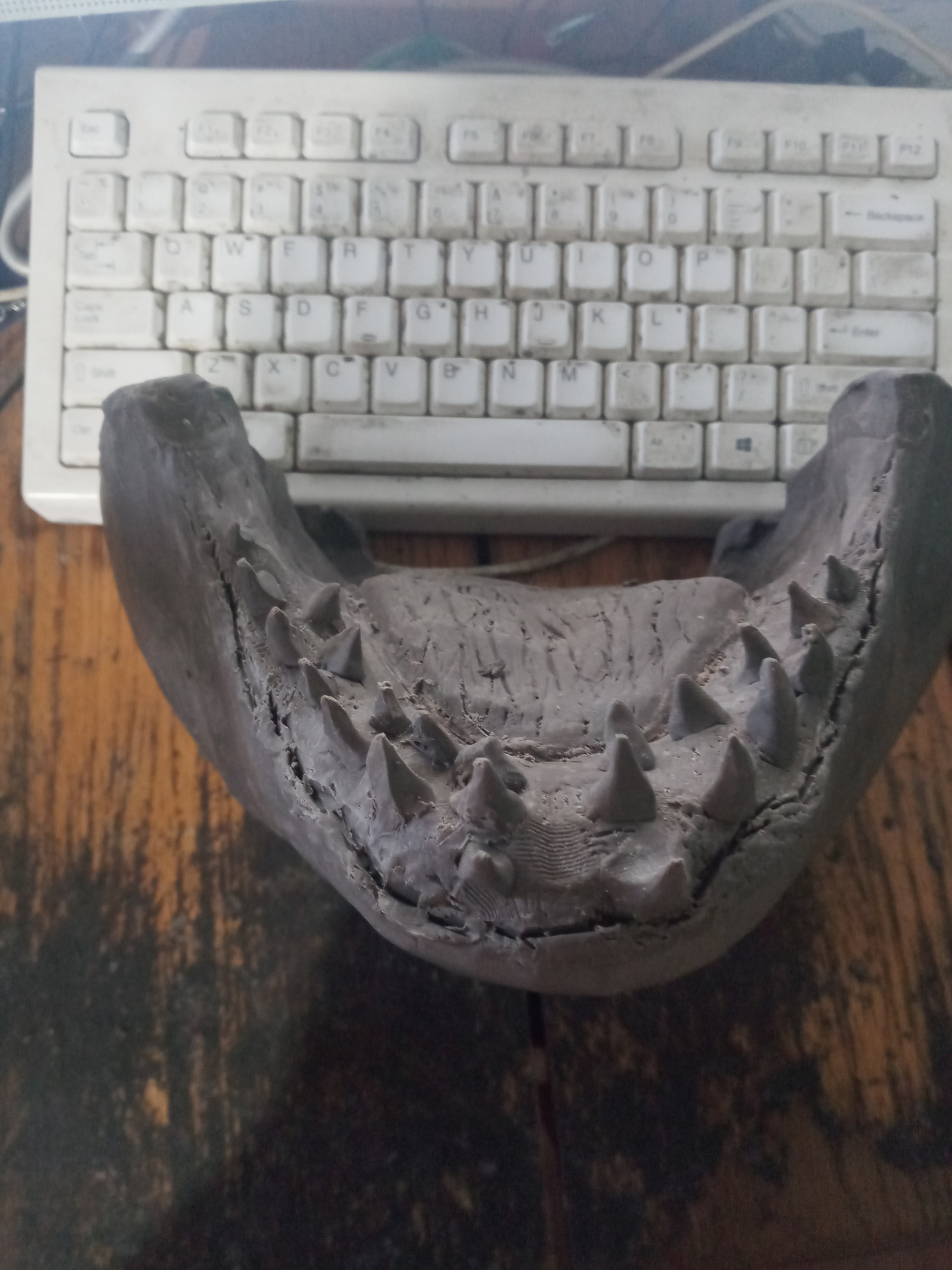
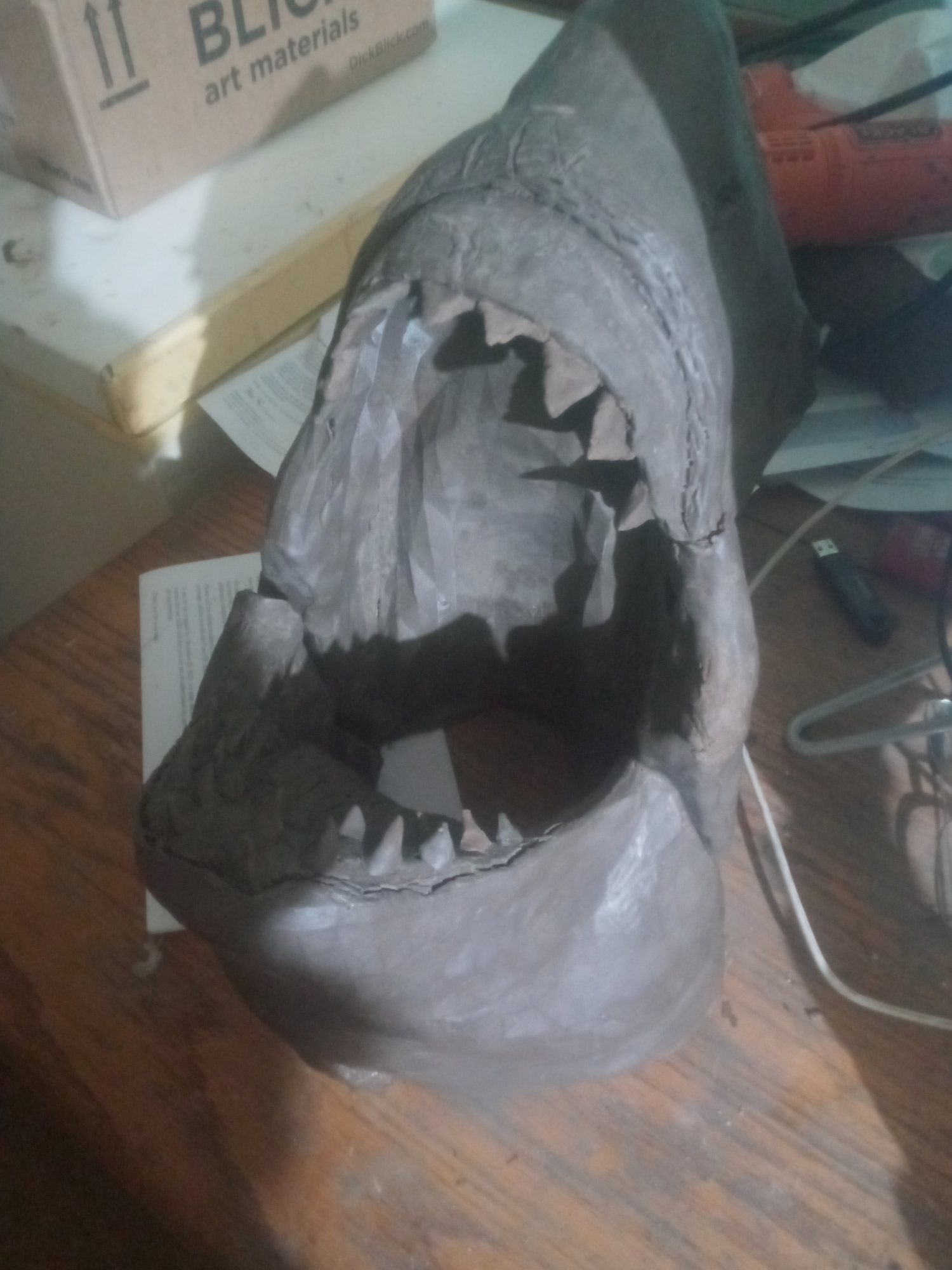
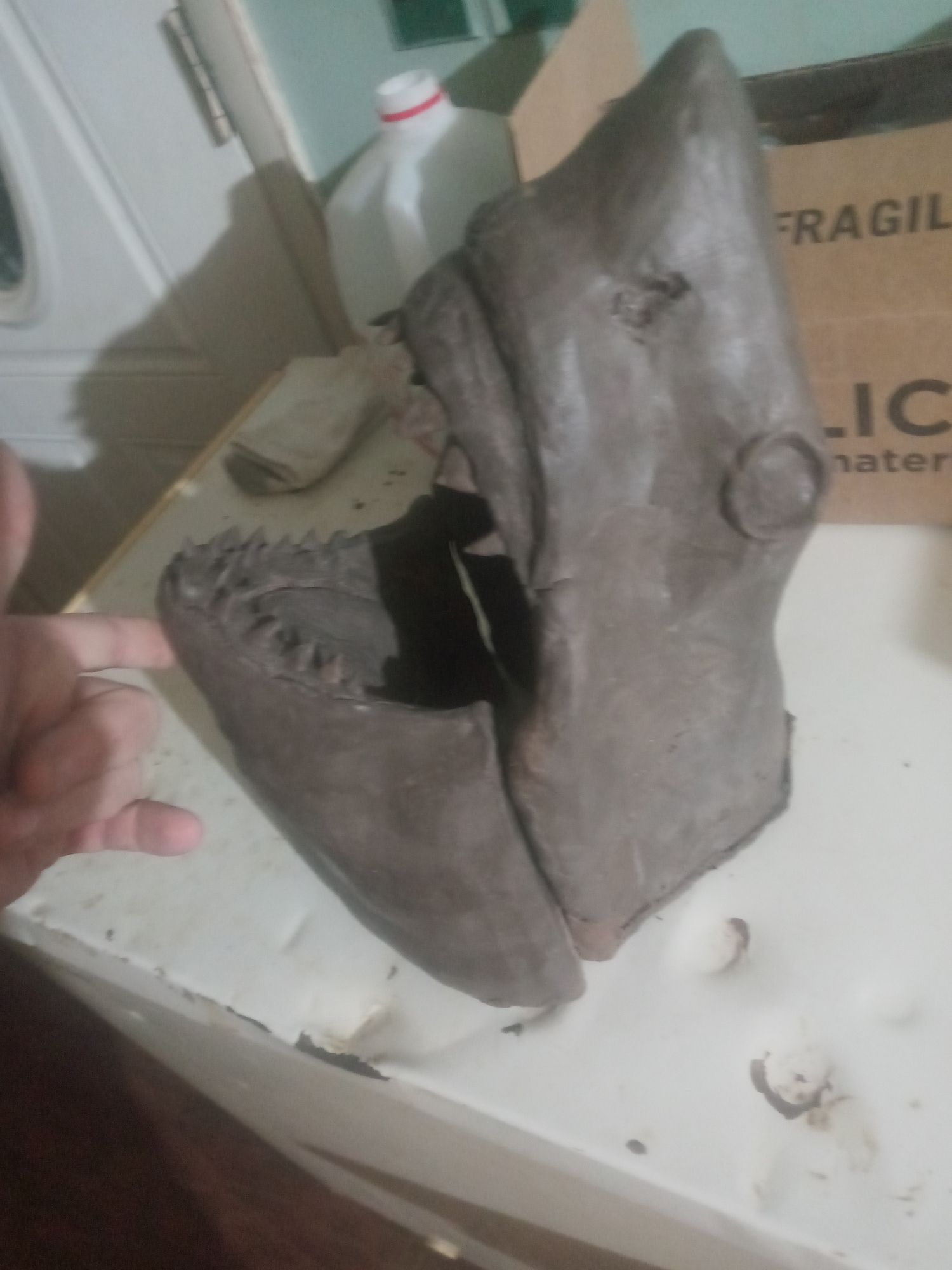
Re: Rubber-band-powered eye blink mechanism
First, here are some old photos of the mask framework before I added moving parts.
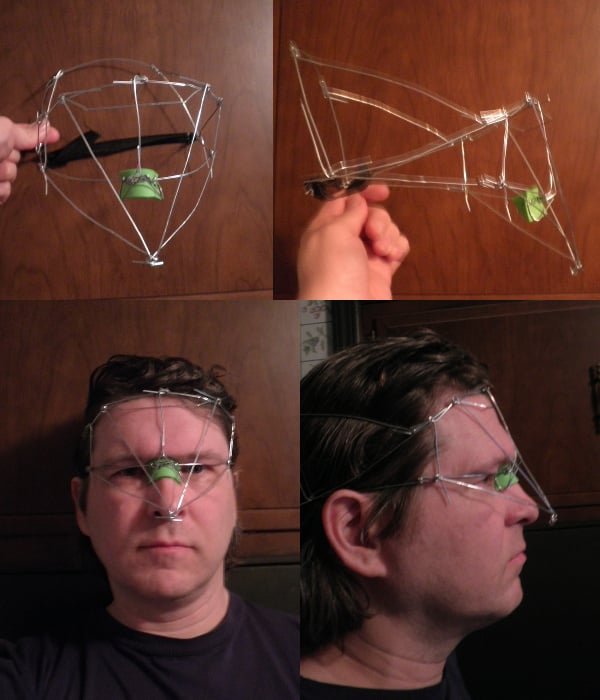
I figured out which parts of my face move the least: my hairline, and the bridge of my nose. The black elastic in the back has to pull the framework tight against those places to prevent the mask from slipping. If the mask is too loose, wrinkling my nose will simply move the whole mask. I sewed on a (green) piece of foam pad to keep the metal from digging into my skin.
You'll see that there is a sort of pyramid formed by 4 lines that meet in front of the tip of my nose: 2 lines from above the forehead, 2 from beside my eyes. Those two lower lines are the axes of rotation for the two main moving parts.
The two main moving parts are basically L-shaped pieces of metal. The "corner" of the L rests against the side of my nose. The "foot" of the L wraps around the axis to form a hinge. The top of the L connects to the eyelid mechanism.
These drawings are not necessarily accurate to what I ended up constructing, but they illustrate the general method.
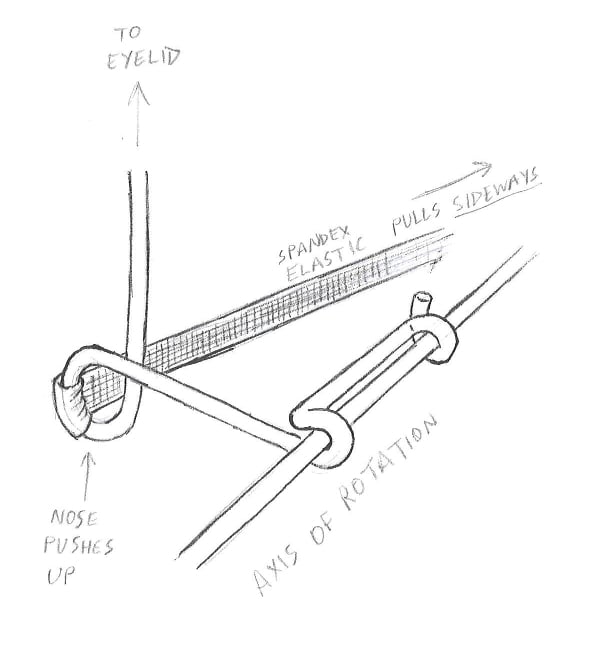
Notice that the elastic pulls sideways. (To keep the hinge from sliding sideways along the axis, I wrapped more metal around the axis to form a barrier next to the hinge.) The elastic is anchored to a point lower than the axis, so that when my nose pushes up on the corner of the L, the elastic gets very slightly stretched. It has just enough tension to pull the L back down when I relax my nose. Too much tension would prevent my nose from pushing it at all.
Because the foot of the L is anchored to the axis, the L doesn't move in a straight line: it tries to rotate. When my nose pushes up on the corner of the L, the top of the L doesn't move straight up; it tilts away from my face. The taller the L, the more horizontal the motion.
Here's what happens at the top of the L:
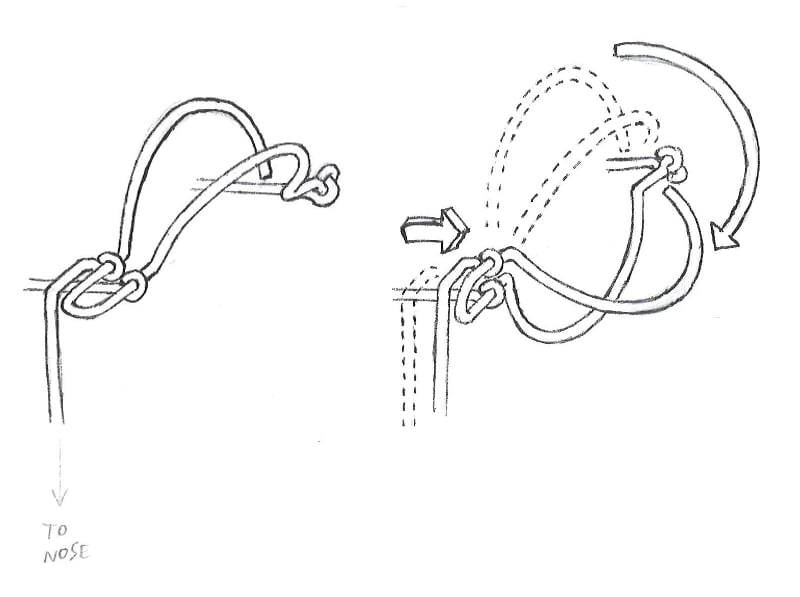
The eyelid is a moving part held in place by two "hooks" that allow it to swivel. The hooks are the ends of a paper clip that has been twist-tied to a small plastic needlepoint grid, which in turn is twist-tied to the metal framework. The grids roughly cover the front edges of my temples, which is where I wanted the eyes to be placed. The twist-ties made it easy to reposition the eyelid assembly on the needlepoint grid until I found an arrangement that looked "right" before installing the L-shaped pieces.
The top of the L hooks the eyelid piece at a point close to the eyelid's center of rotation. This turns a small horizontal movement into a large rotation, so the eyelid flips over when the L tilts forward.
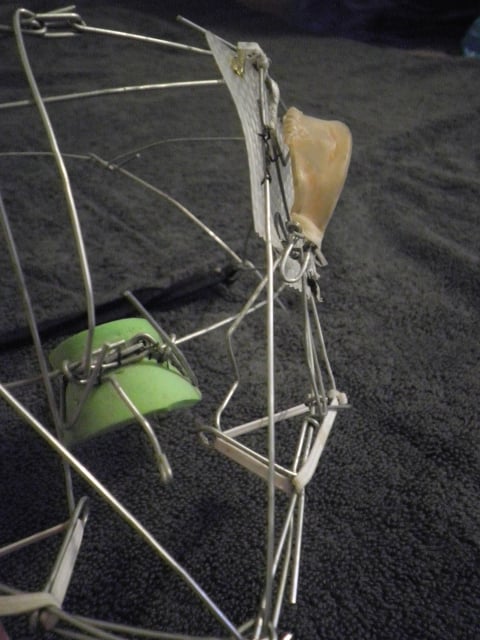
This is a photo of the finished left eyelid mechanism, with an attempt at a latex skin on the eyelid. The vertical part of the L piece is not a straight line; it has some angles in it, to prevent it from bumping into other parts when it moves.
It's a very finicky mechanism. I wanted to eventually put foam flesh on the mask with a layer of liquid latex skin. The problem is, the proper functioning of the mechanism relies on the overall shape of the framework. Every time I try to add something to the framework, a bit of distortion takes place. That distortion hinders the movement, so I have to make adjustments. "Adjustment" means bending the metal. And of course, if you bend a paper clip too many times, it snaps. After having to replace broken pieces several times, I got frustrated and gave up.
So there are some kinks to work out, but I think this is a good proof-of-concept. Maybe someone else, with more resources and better time management skills, can take this idea further.
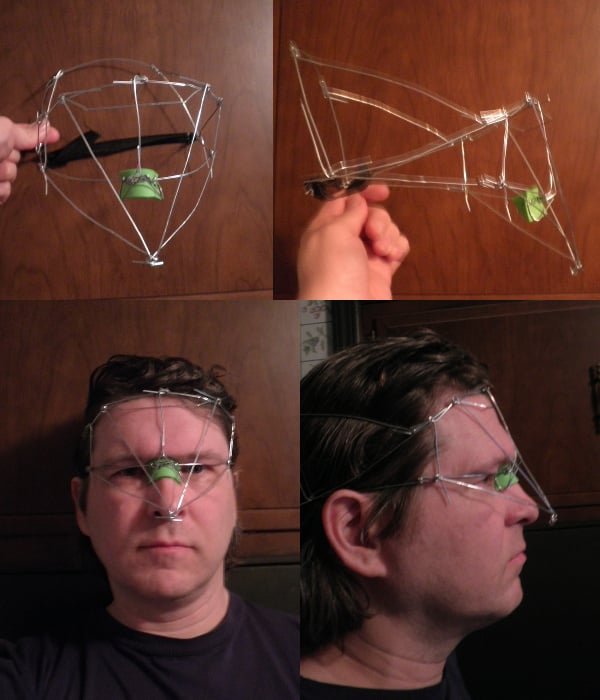
I figured out which parts of my face move the least: my hairline, and the bridge of my nose. The black elastic in the back has to pull the framework tight against those places to prevent the mask from slipping. If the mask is too loose, wrinkling my nose will simply move the whole mask. I sewed on a (green) piece of foam pad to keep the metal from digging into my skin.
You'll see that there is a sort of pyramid formed by 4 lines that meet in front of the tip of my nose: 2 lines from above the forehead, 2 from beside my eyes. Those two lower lines are the axes of rotation for the two main moving parts.
The two main moving parts are basically L-shaped pieces of metal. The "corner" of the L rests against the side of my nose. The "foot" of the L wraps around the axis to form a hinge. The top of the L connects to the eyelid mechanism.
These drawings are not necessarily accurate to what I ended up constructing, but they illustrate the general method.
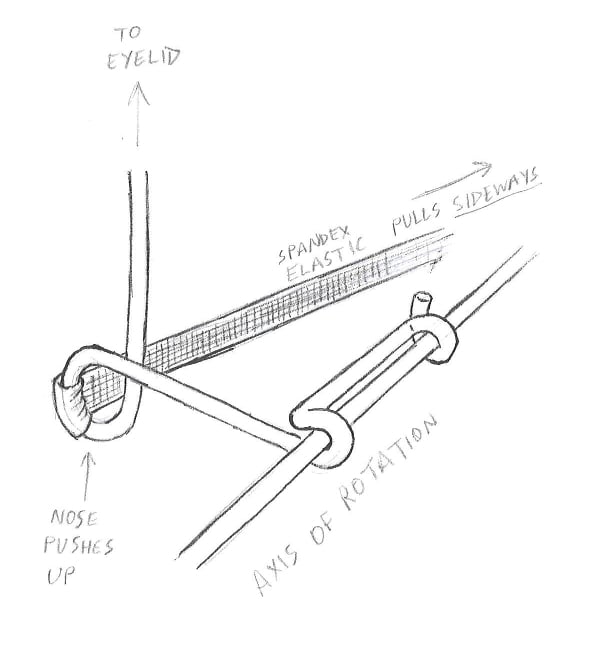
Notice that the elastic pulls sideways. (To keep the hinge from sliding sideways along the axis, I wrapped more metal around the axis to form a barrier next to the hinge.) The elastic is anchored to a point lower than the axis, so that when my nose pushes up on the corner of the L, the elastic gets very slightly stretched. It has just enough tension to pull the L back down when I relax my nose. Too much tension would prevent my nose from pushing it at all.
Because the foot of the L is anchored to the axis, the L doesn't move in a straight line: it tries to rotate. When my nose pushes up on the corner of the L, the top of the L doesn't move straight up; it tilts away from my face. The taller the L, the more horizontal the motion.
Here's what happens at the top of the L:
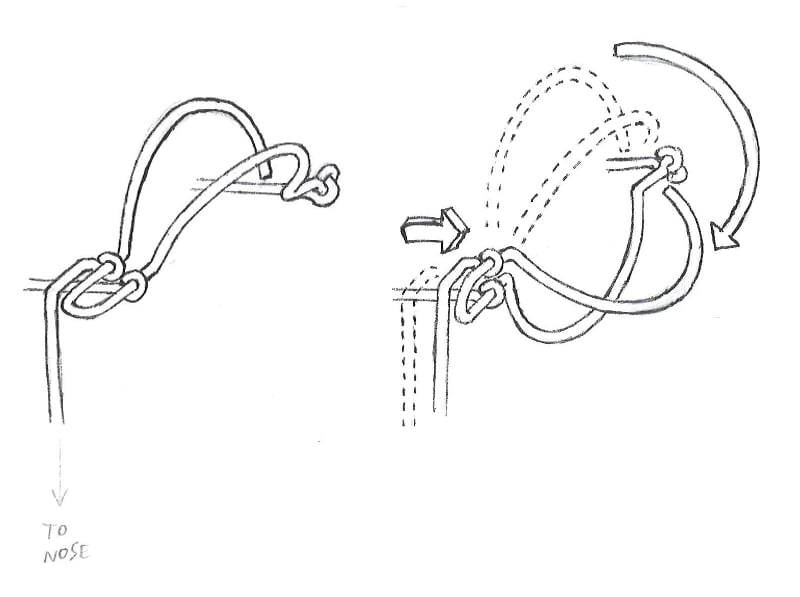
The eyelid is a moving part held in place by two "hooks" that allow it to swivel. The hooks are the ends of a paper clip that has been twist-tied to a small plastic needlepoint grid, which in turn is twist-tied to the metal framework. The grids roughly cover the front edges of my temples, which is where I wanted the eyes to be placed. The twist-ties made it easy to reposition the eyelid assembly on the needlepoint grid until I found an arrangement that looked "right" before installing the L-shaped pieces.
The top of the L hooks the eyelid piece at a point close to the eyelid's center of rotation. This turns a small horizontal movement into a large rotation, so the eyelid flips over when the L tilts forward.
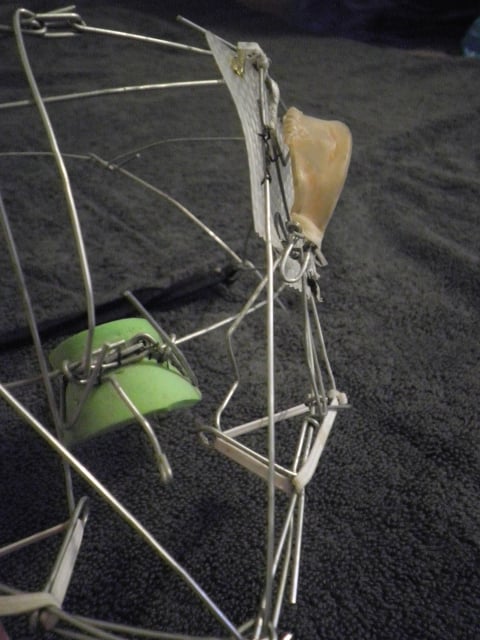
This is a photo of the finished left eyelid mechanism, with an attempt at a latex skin on the eyelid. The vertical part of the L piece is not a straight line; it has some angles in it, to prevent it from bumping into other parts when it moves.
It's a very finicky mechanism. I wanted to eventually put foam flesh on the mask with a layer of liquid latex skin. The problem is, the proper functioning of the mechanism relies on the overall shape of the framework. Every time I try to add something to the framework, a bit of distortion takes place. That distortion hinders the movement, so I have to make adjustments. "Adjustment" means bending the metal. And of course, if you bend a paper clip too many times, it snaps. After having to replace broken pieces several times, I got frustrated and gave up.
So there are some kinks to work out, but I think this is a good proof-of-concept. Maybe someone else, with more resources and better time management skills, can take this idea further.
Rubber-band-powered eye blink mechanism
I hope you'll have a look at this odd experiment from an amateur.
I've made two simple animatronic masks in the past, both for classes I was taking. One was at a small special fx shop in Manhattan, and the other at the Art Institute of Pittsburgh. I no longer have access to the materials and equipment I used back then. (Some of which are poisonous chemicals I probably wouldn't be allowed to have in my apartment anyway.) So I'm always looking for cheap and easily available substitutes.
A few years ago I was watching a video in which a fursuiter was being interviewed for a local TV newscast. He was showing off his home-made costume, which was pretty impressive. It had the typical hollow mascot head, and as he showed the interior, I could see, squinting at the low-resolution video, that it was supported by some kind of metal framework. I thought, "this is homemade? Who can do metalwork at home?" Then the guy humblebrags, "So as you can see, I made this out of paper clips..."
Brilliant!
So I bought a box of paper clips. Don't laugh! It seemed the perfect cheap substitute for a fiberglass shell or vacu-formed plastic. The metal is easily pliable, but holds its shape when you are done shaping it.
I conceived of a face-hugging metal framework, upon which a mask could be built. My jaw would be uncovered, so the character could talk. I wanted to put the eyes near the sides of the head, to achieve an alien/animal look. And, I wanted the eyes to blink. I came up with a clever mechanism for this.
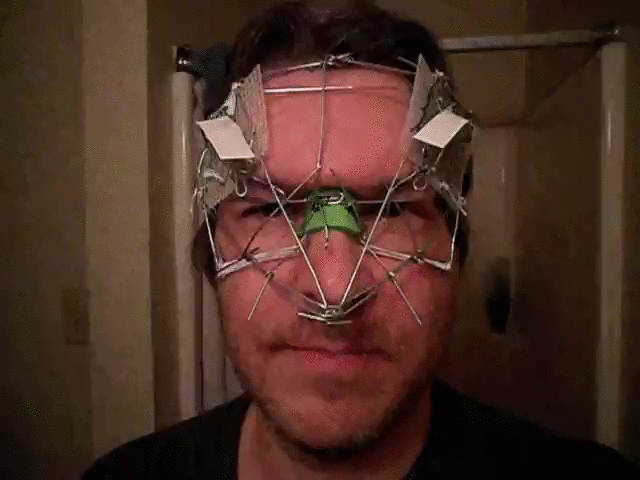
I taped strips of paper to the eyelids so that it's easier to see them move in the video. The eyes blink when I scrunch up my nose. There are no motors or batteries; just a couple of rubber bands. The eyelids are not connected to each other, so each one can wink independently.
Details to follow.
I've made two simple animatronic masks in the past, both for classes I was taking. One was at a small special fx shop in Manhattan, and the other at the Art Institute of Pittsburgh. I no longer have access to the materials and equipment I used back then. (Some of which are poisonous chemicals I probably wouldn't be allowed to have in my apartment anyway.) So I'm always looking for cheap and easily available substitutes.
A few years ago I was watching a video in which a fursuiter was being interviewed for a local TV newscast. He was showing off his home-made costume, which was pretty impressive. It had the typical hollow mascot head, and as he showed the interior, I could see, squinting at the low-resolution video, that it was supported by some kind of metal framework. I thought, "this is homemade? Who can do metalwork at home?" Then the guy humblebrags, "So as you can see, I made this out of paper clips..."
Brilliant!
So I bought a box of paper clips. Don't laugh! It seemed the perfect cheap substitute for a fiberglass shell or vacu-formed plastic. The metal is easily pliable, but holds its shape when you are done shaping it.
I conceived of a face-hugging metal framework, upon which a mask could be built. My jaw would be uncovered, so the character could talk. I wanted to put the eyes near the sides of the head, to achieve an alien/animal look. And, I wanted the eyes to blink. I came up with a clever mechanism for this.
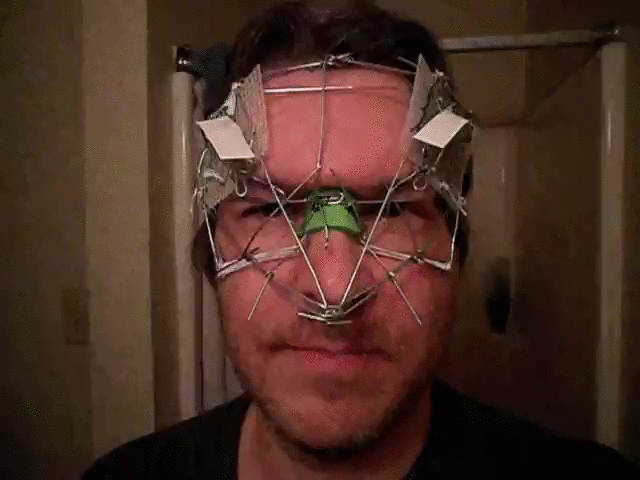
I taped strips of paper to the eyelids so that it's easier to see them move in the video. The eyes blink when I scrunch up my nose. There are no motors or batteries; just a couple of rubber bands. The eyelids are not connected to each other, so each one can wink independently.
Details to follow.
Dang that Monster Clay!
So....after a lot of research and trial and error, I've finally isolated the problem. My Monster Clay (soft hardness, brown, Lot #122118) apparently has some sulfur impurity. Cutting a fresh chunk out of it, my platinum based silicone products simply refuse to cure on it. Rebound 25 is still gooey after days on it. So....I'm giving all my monster clay to a friend's kids.
What's REALLY frustrating is that I have to consider all my tools to have been contaminated, too. While I'm confident I can clean my metal tools, I think all the other stuff, like wooden carving tools, etc., are all suspect.
Drat!
Nothing really to report...just venting!
What's REALLY frustrating is that I have to consider all my tools to have been contaminated, too. While I'm confident I can clean my metal tools, I think all the other stuff, like wooden carving tools, etc., are all suspect.
Drat!
Nothing really to report...just venting!
Re: Learning with ADHD??
Hi, I was super happy for the free week when I sign in, the week passed and I never use it becouse I started cleaning a special room for creation, I was súper sad, I started my first month and now is almost finished and now the deadline is making me rush to make the courses, but they are so many couses that make me feel in heaven as an artist but overwhelmd as a person with aDHD, in the end I love this fantastic school, sorry for the grammar I speak spanish and my text tingy is changing my words aaaaaaaaaaahhhh
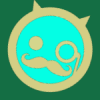
1
Character Makeup Contest 2019 - High Priestess
HIGH PRIESTESS
FOREHEAD AND BRAIN - SILICONE
CROWN - WORBLA
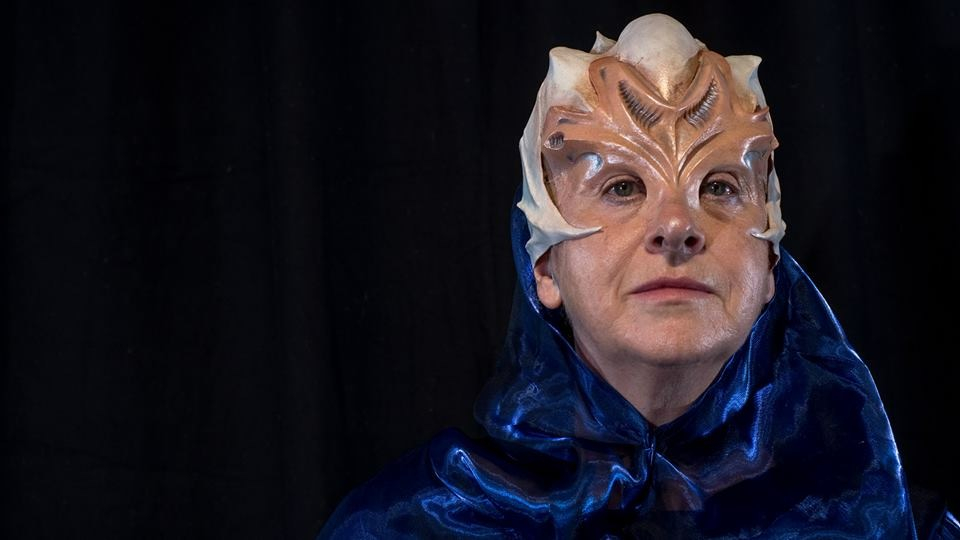
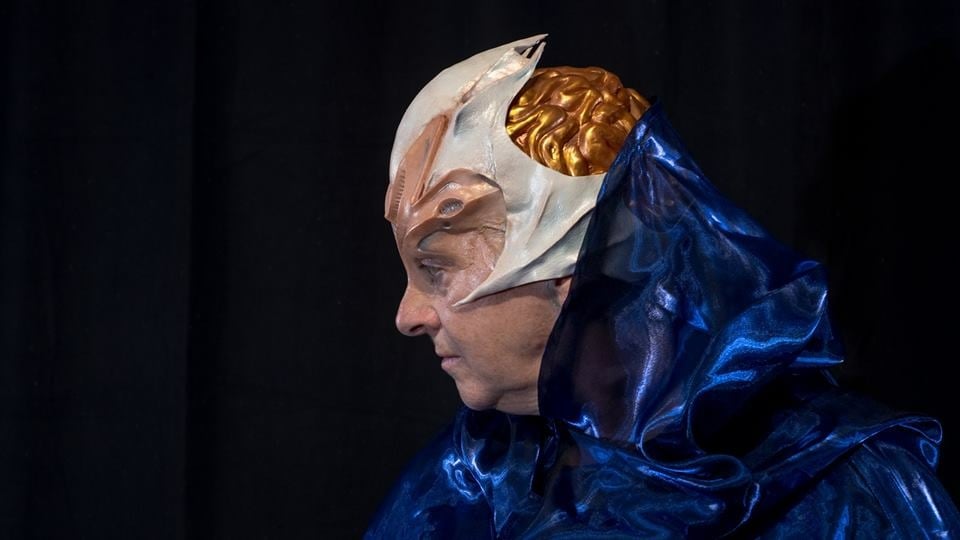
FOREHEAD AND BRAIN - SILICONE
CROWN - WORBLA
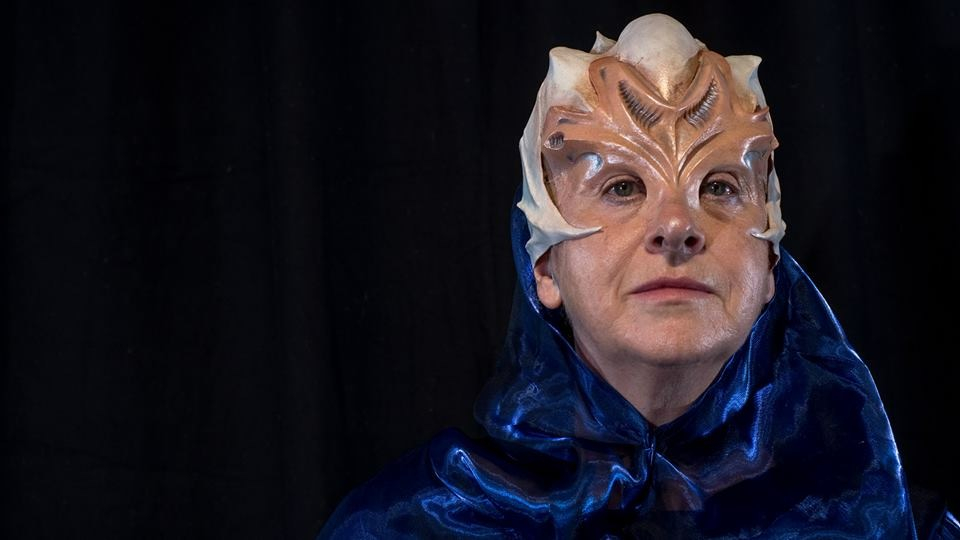
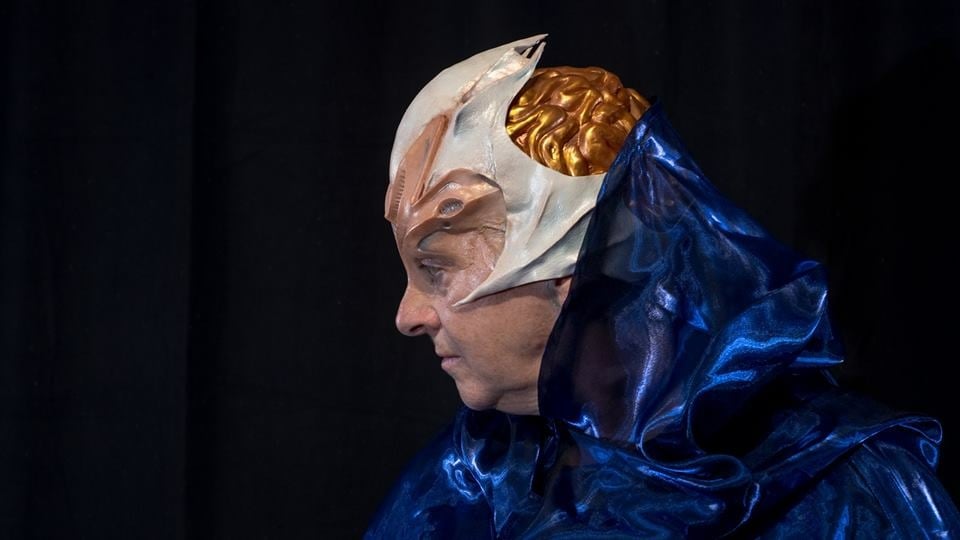
Giant Hamster on Holidays
My 15-year-old daughter created this costume for herself for Halloween.
The top of the head has a little horn and a removable brain. She used a foam camping mat for the inside structure. It's glued and sown together.
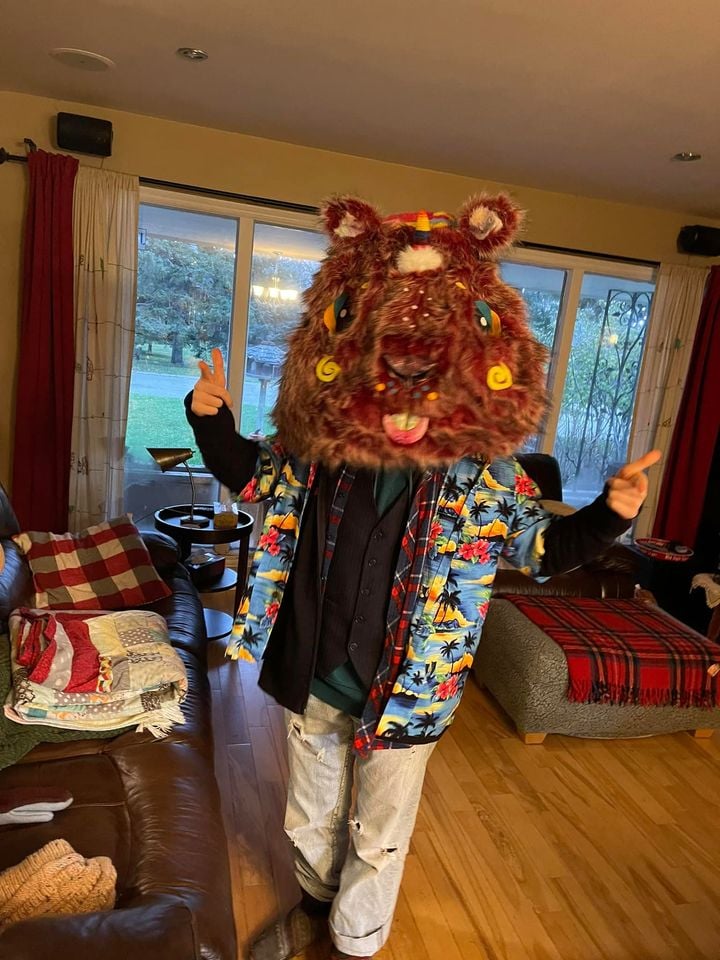
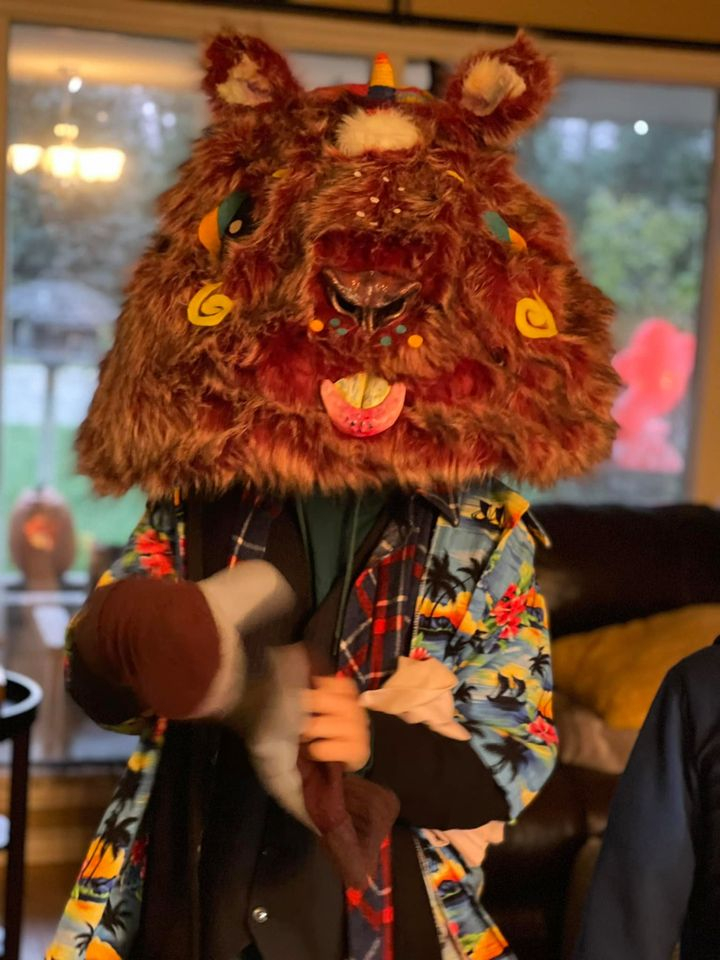
The top of the head has a little horn and a removable brain. She used a foam camping mat for the inside structure. It's glued and sown together.
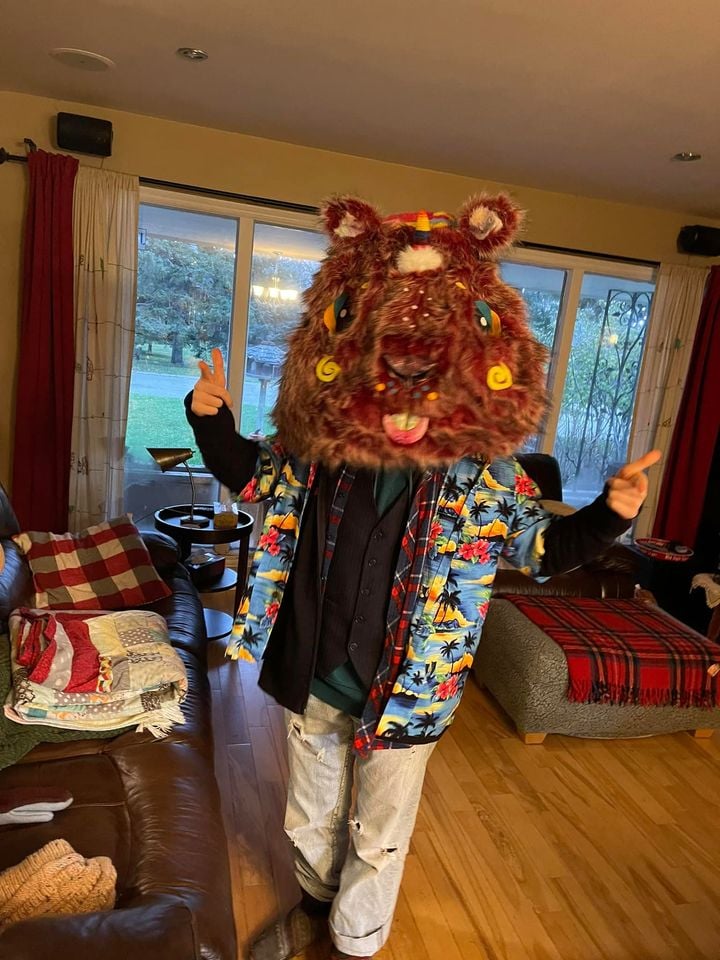
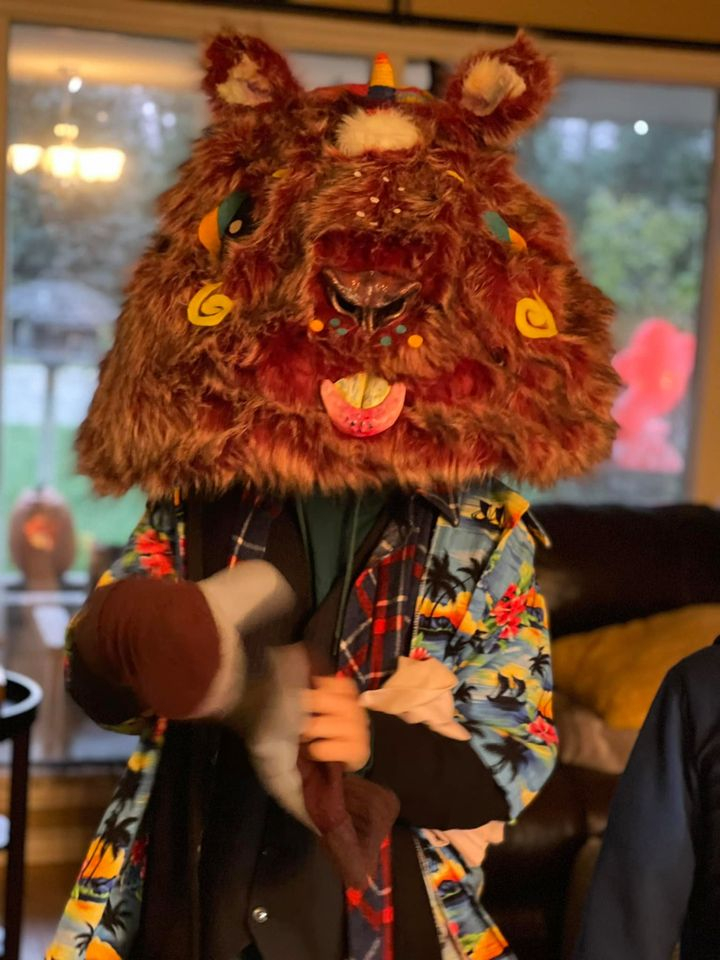
My Rick Baker style Wolfman
Finally finishing up my Rick Baker Wolfman. Been a long process. This is only one of three sculpts-into-mask I've ever done.
Finally found a modacrylic wig that I can modify fairly easy. Next step is gluing and punching hair around the face. This is going to be a display piece.
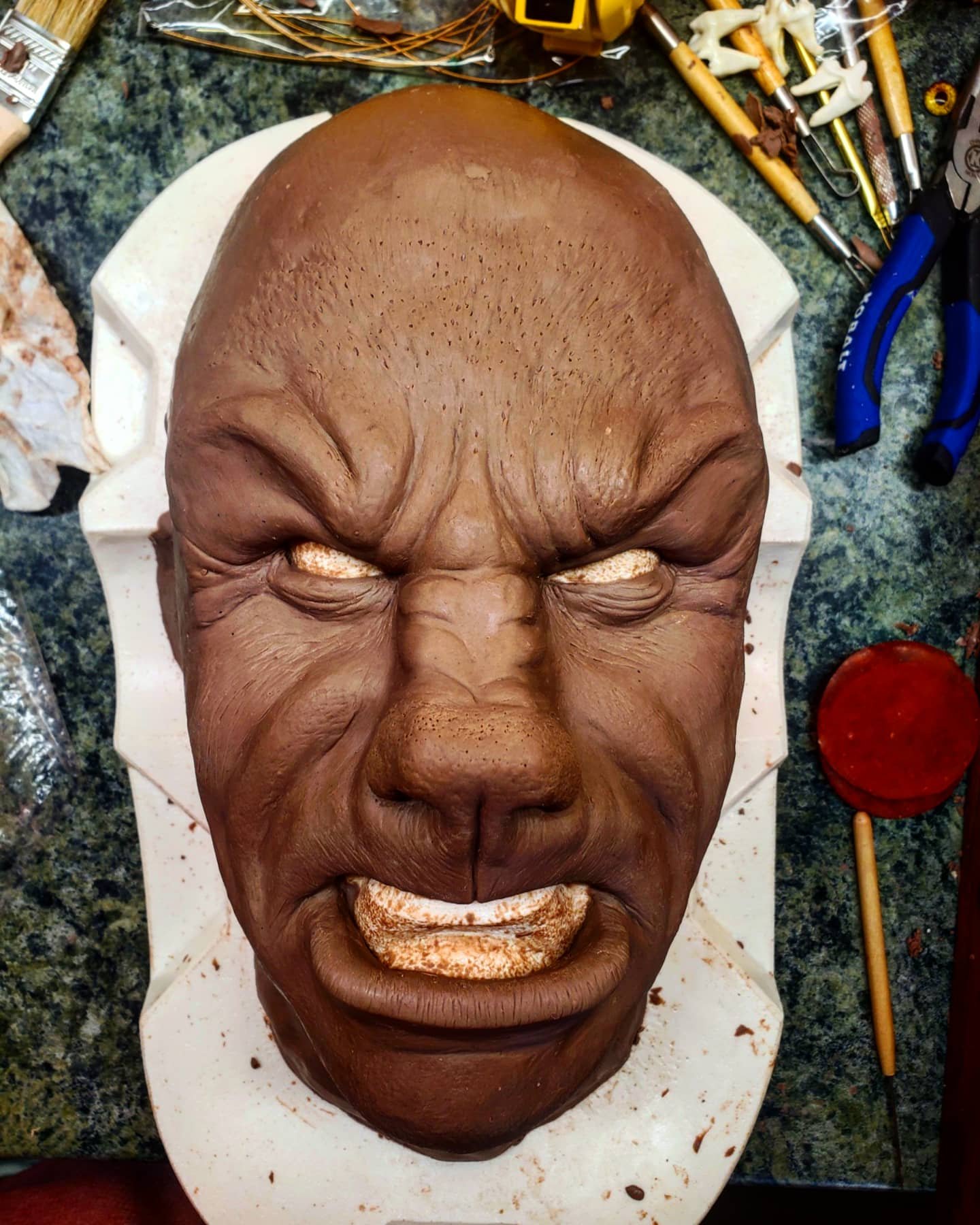
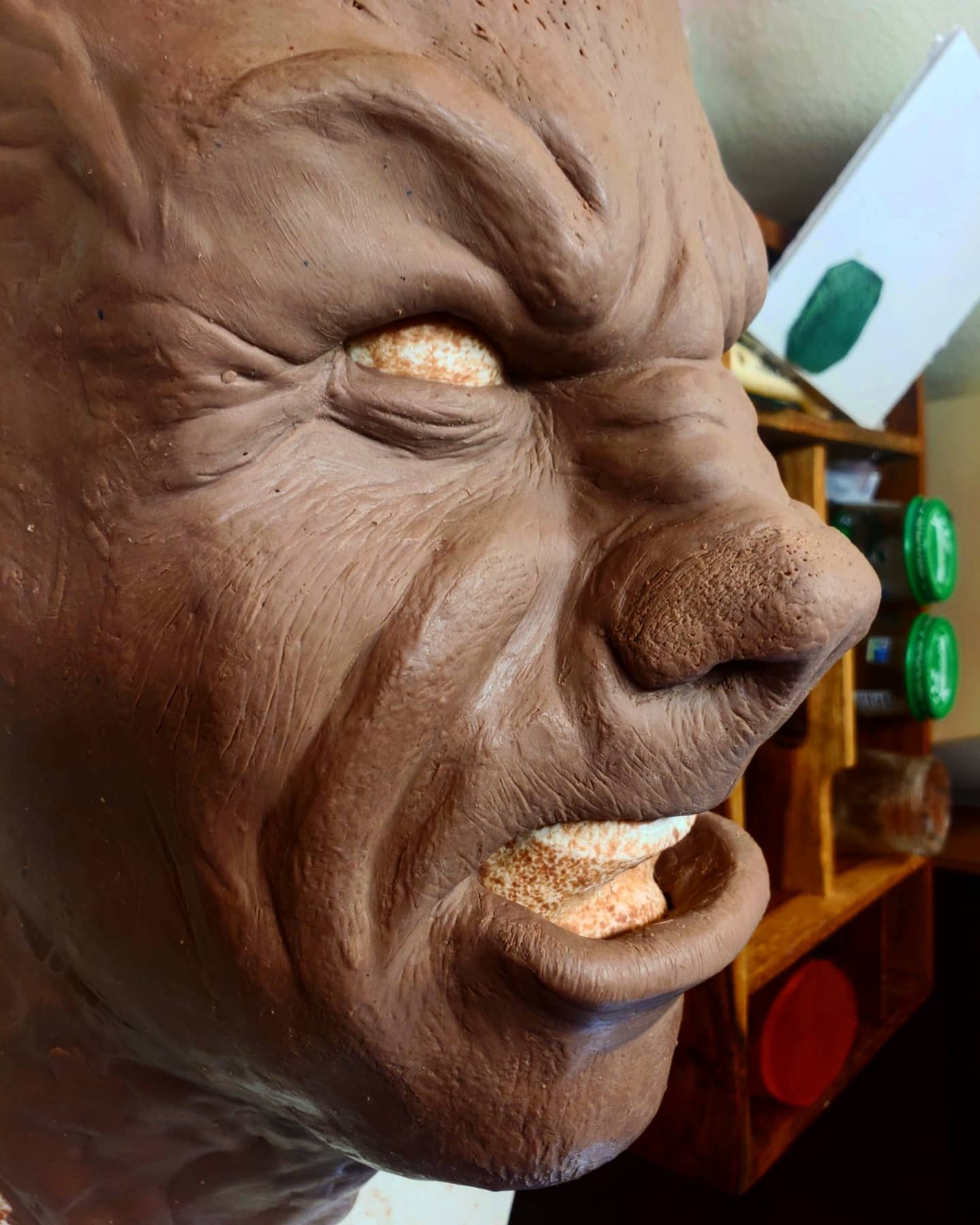
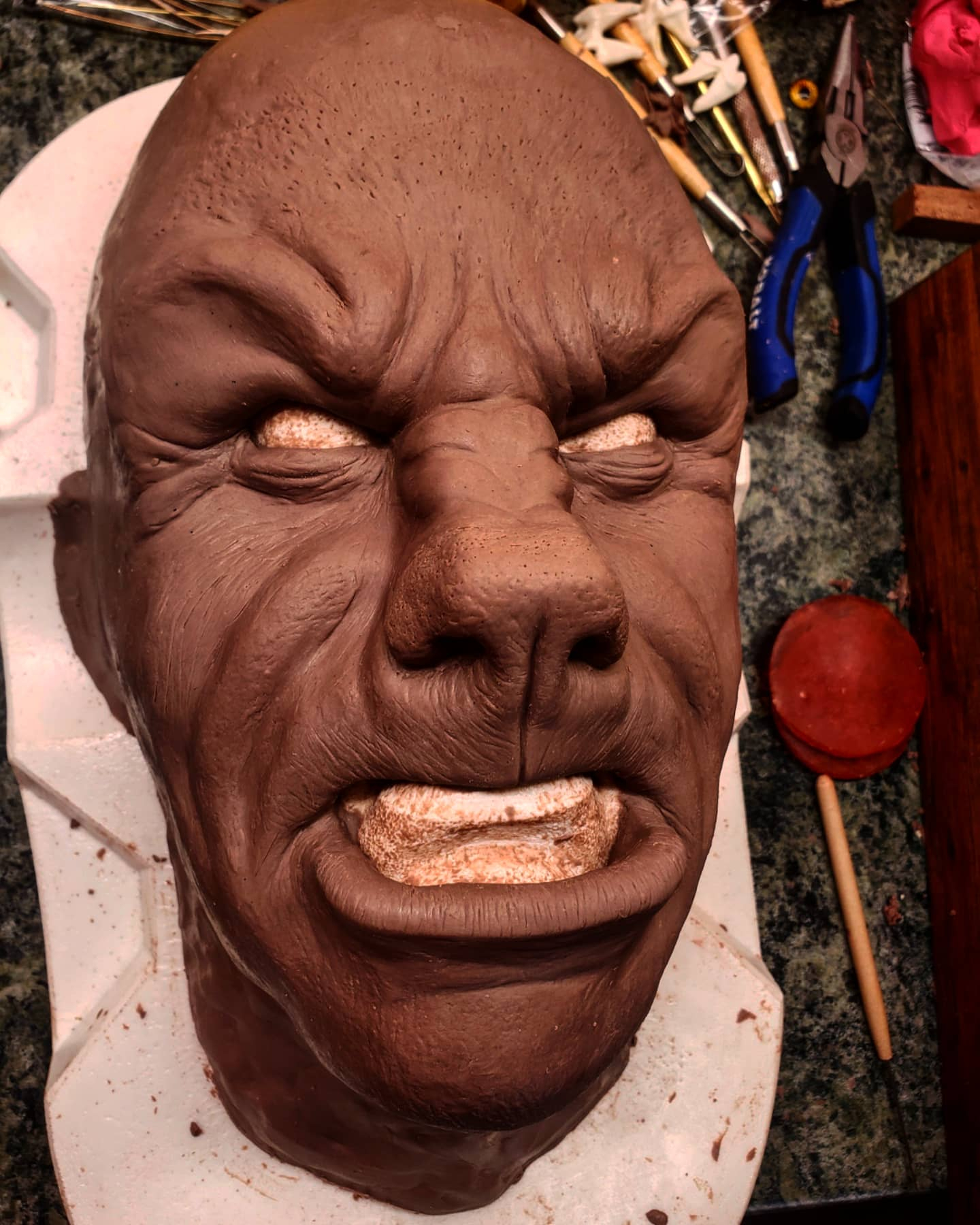
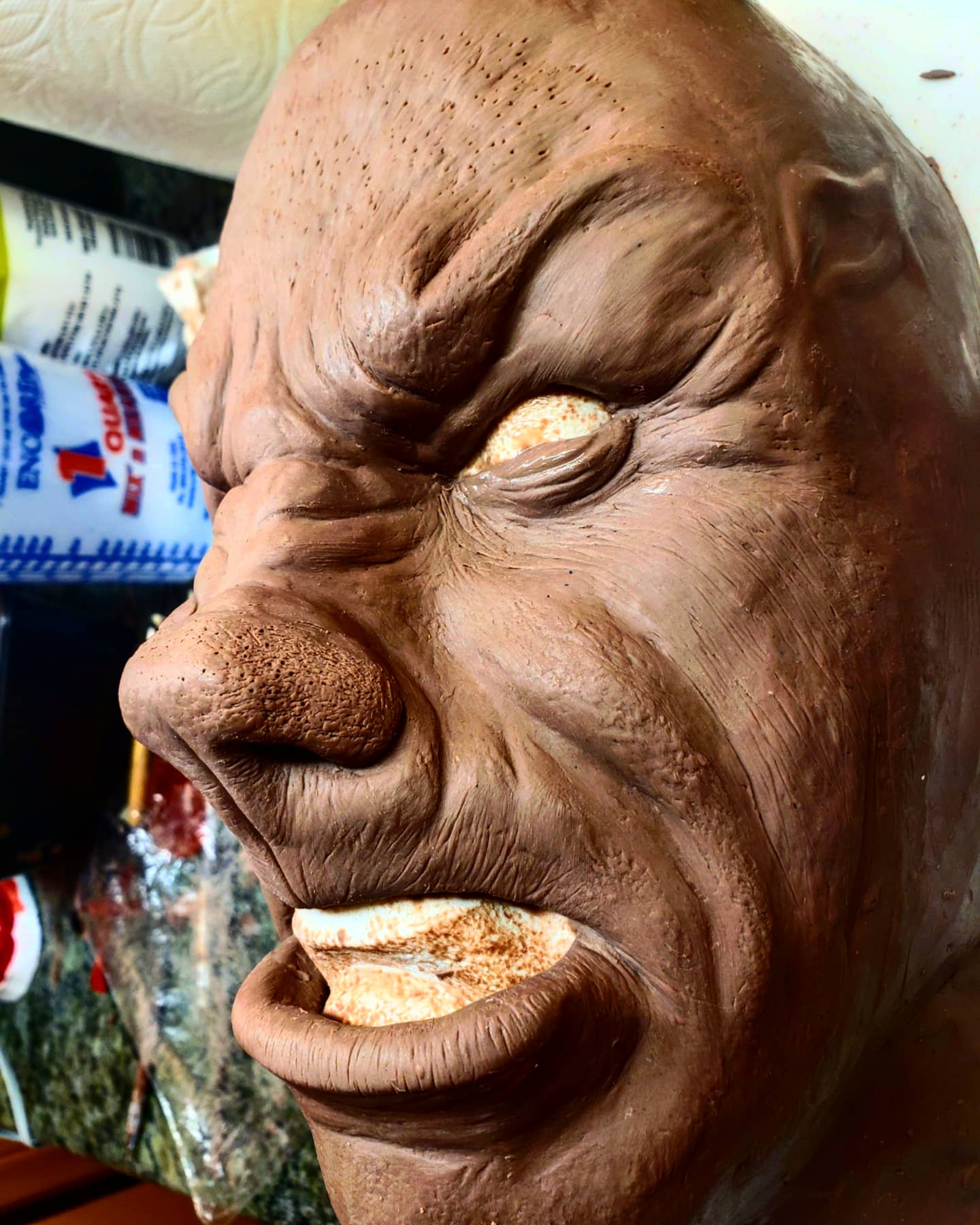
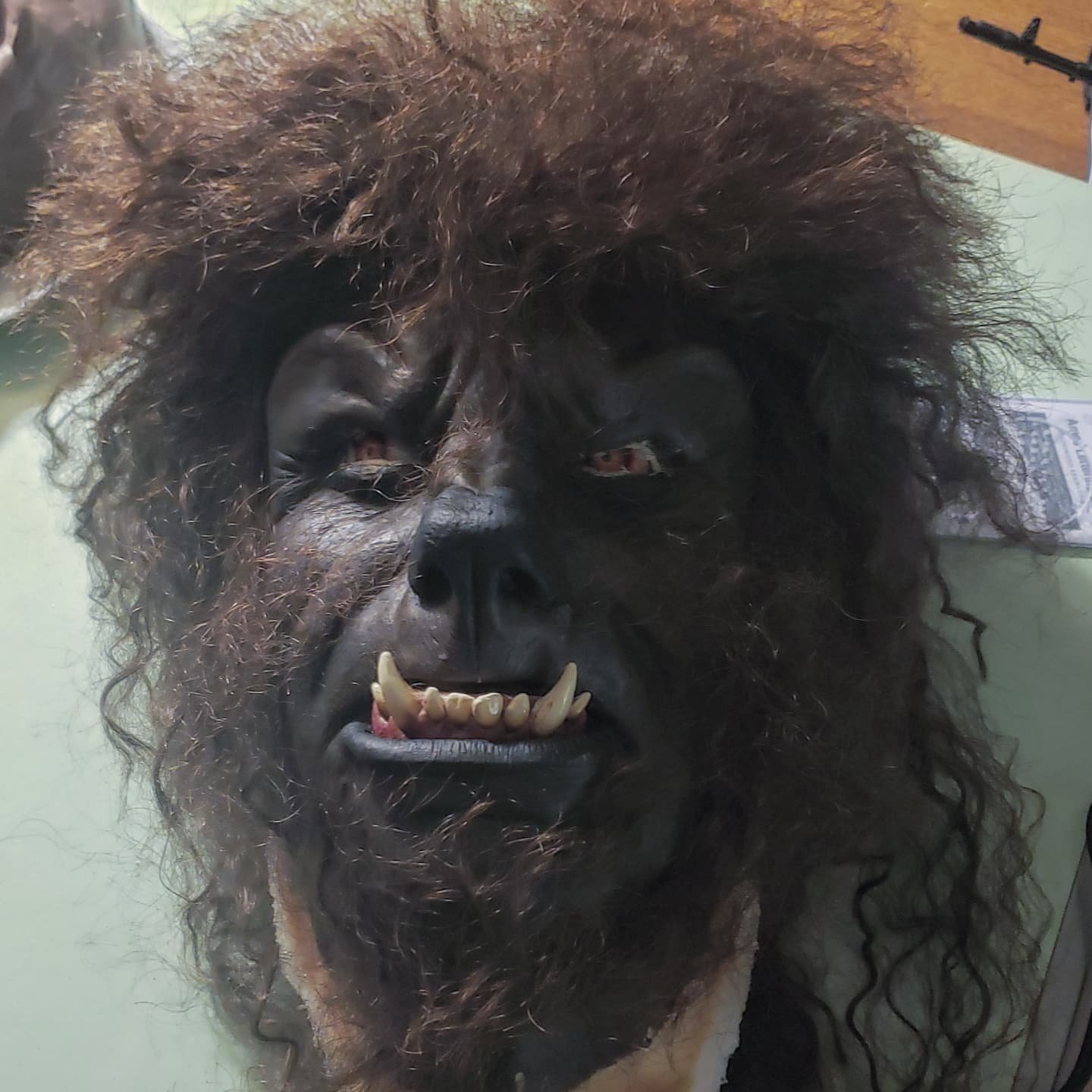
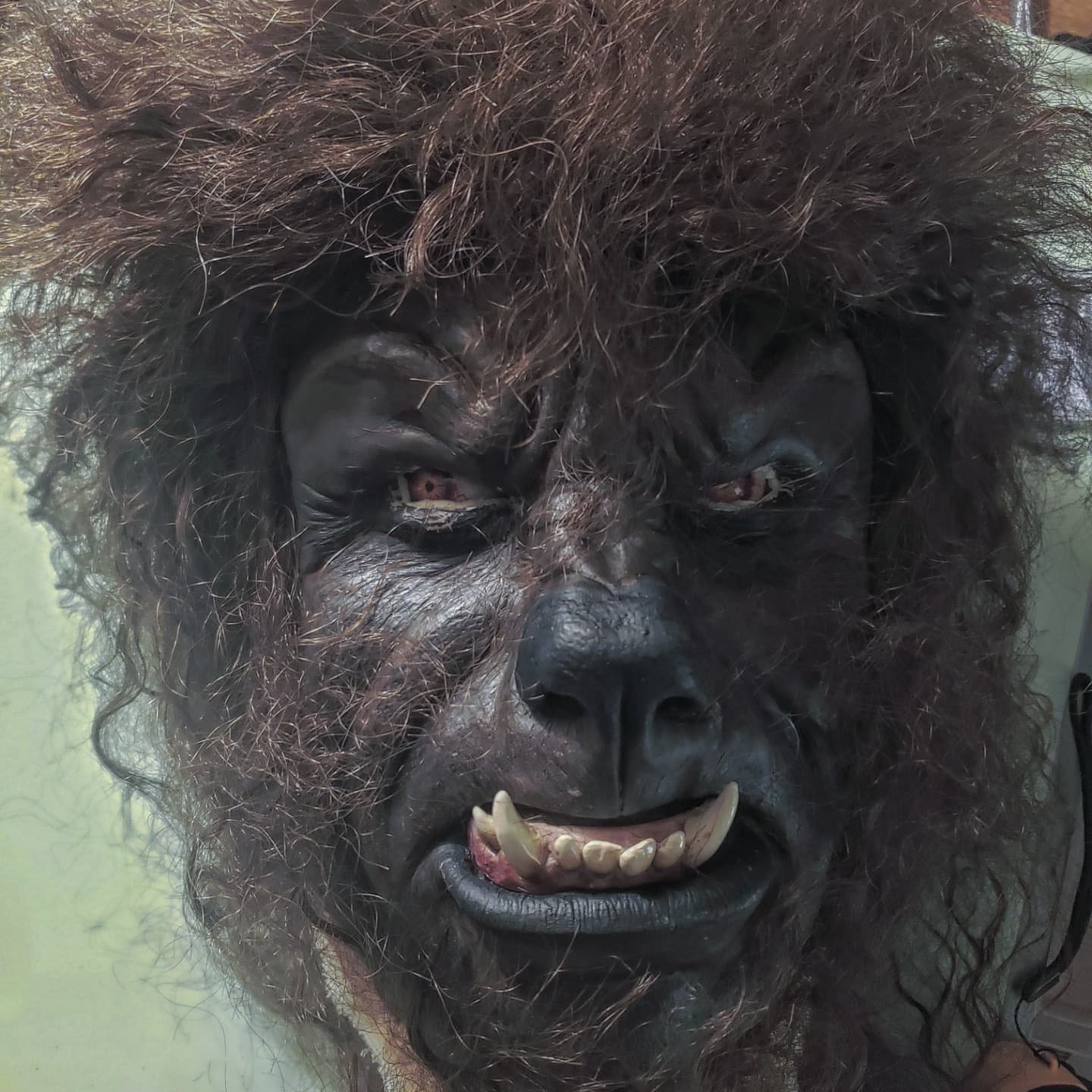
Finally found a modacrylic wig that I can modify fairly easy. Next step is gluing and punching hair around the face. This is going to be a display piece.
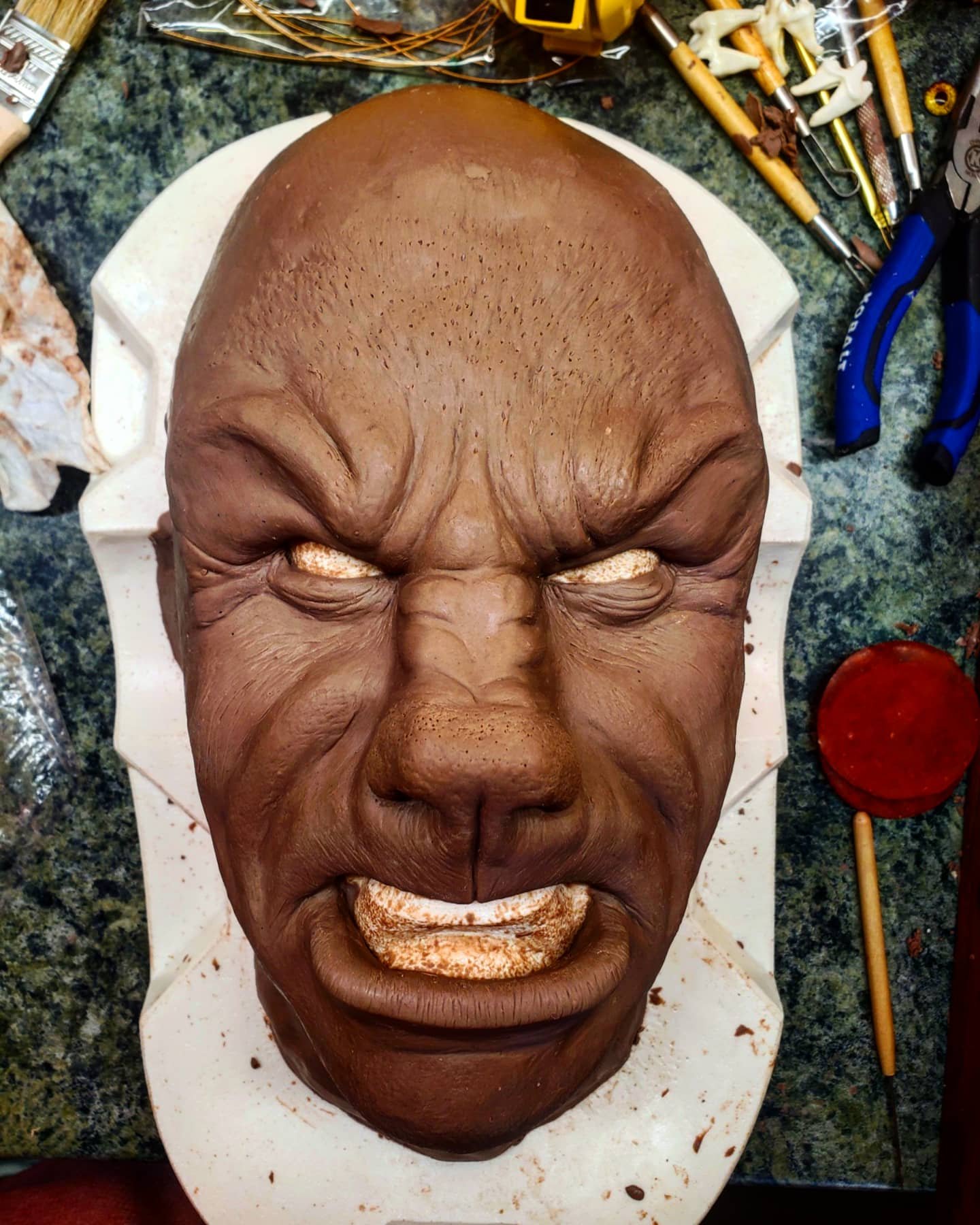
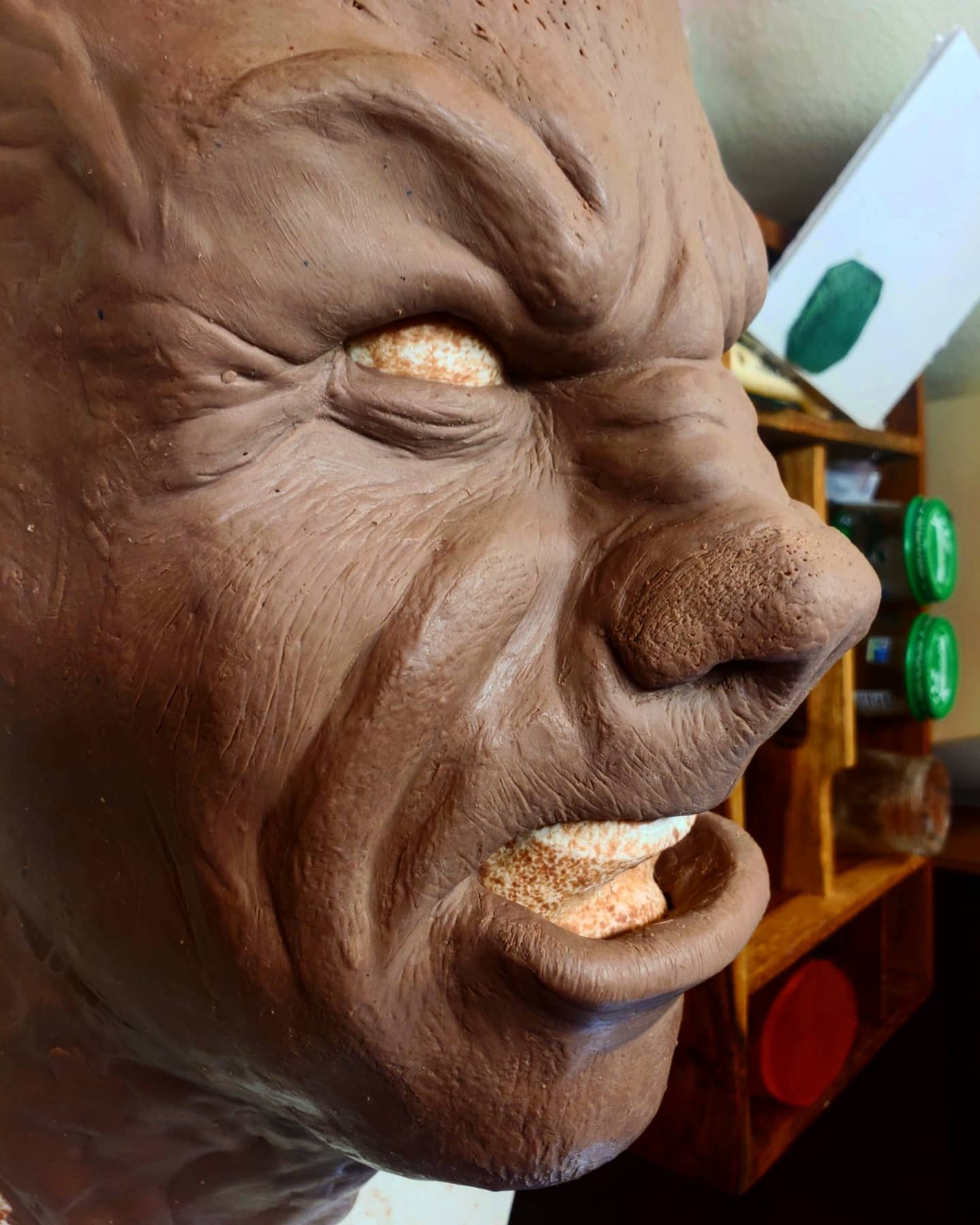
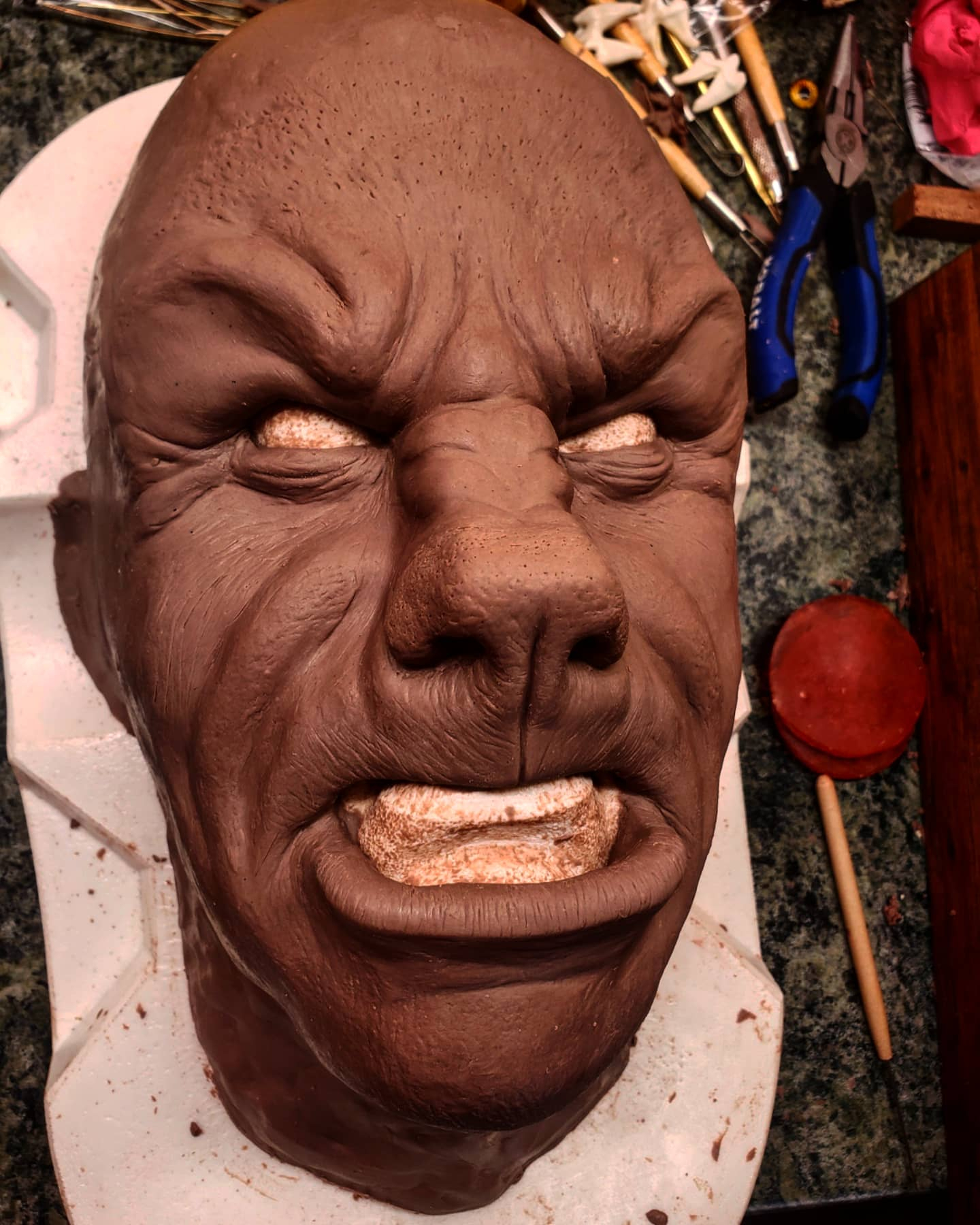
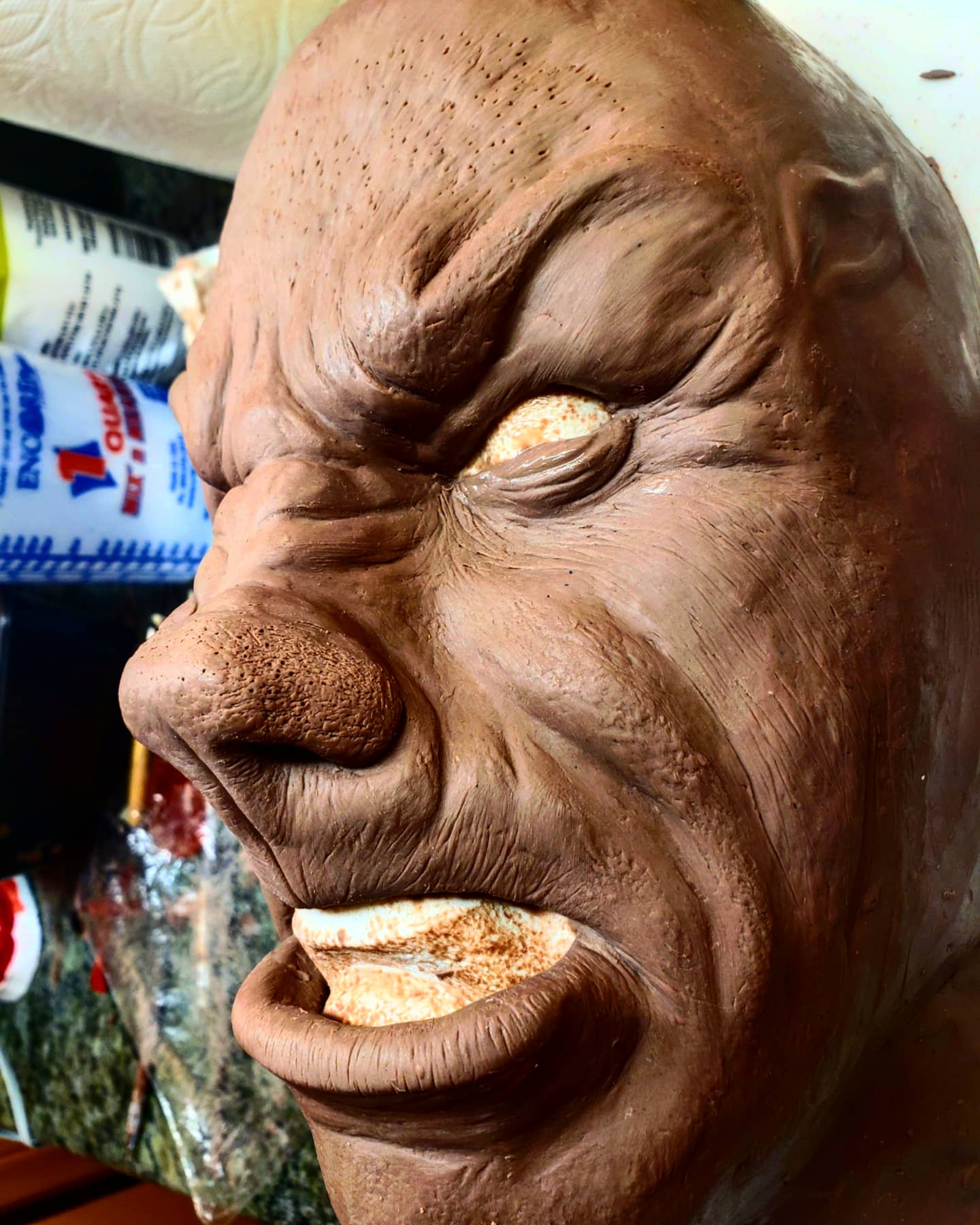
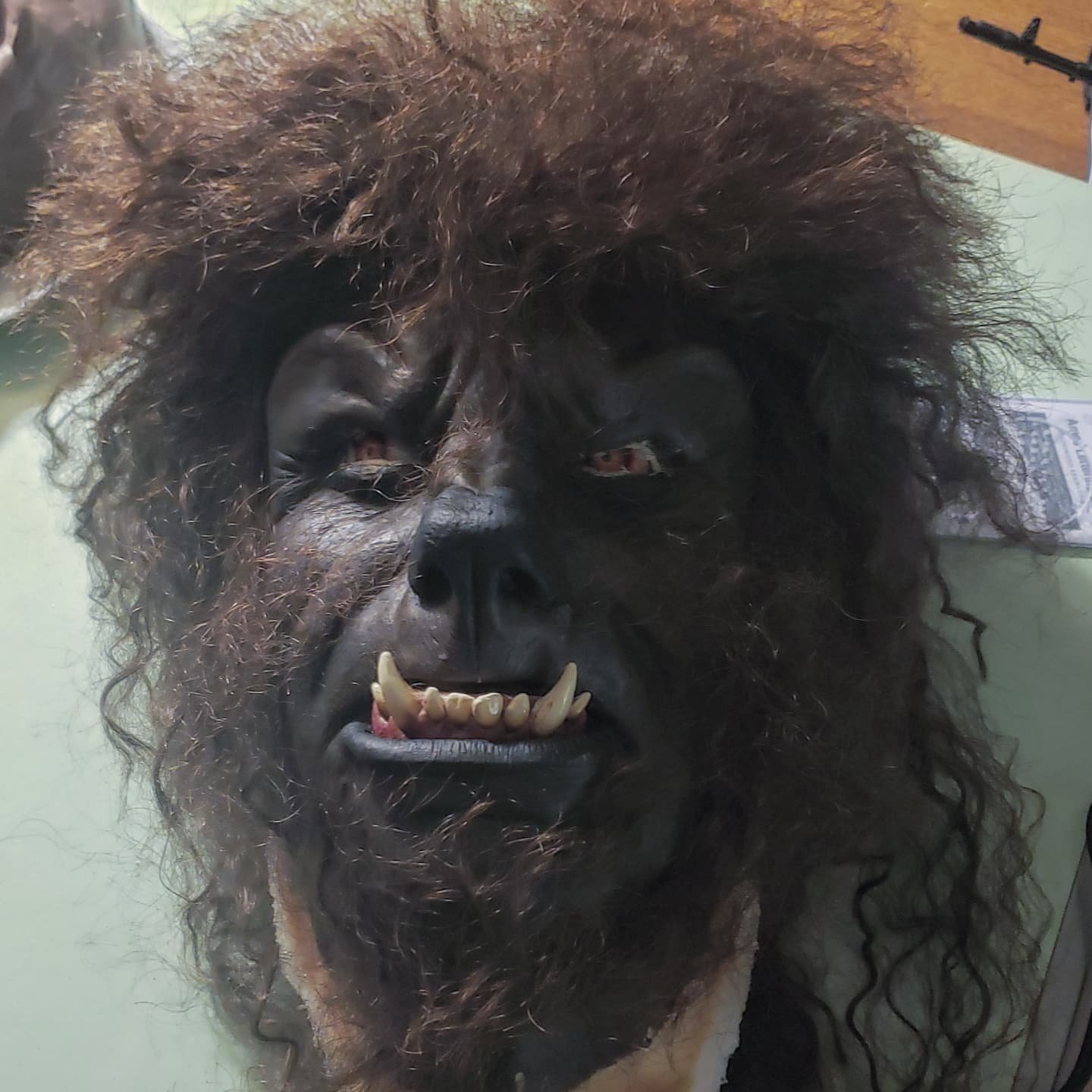
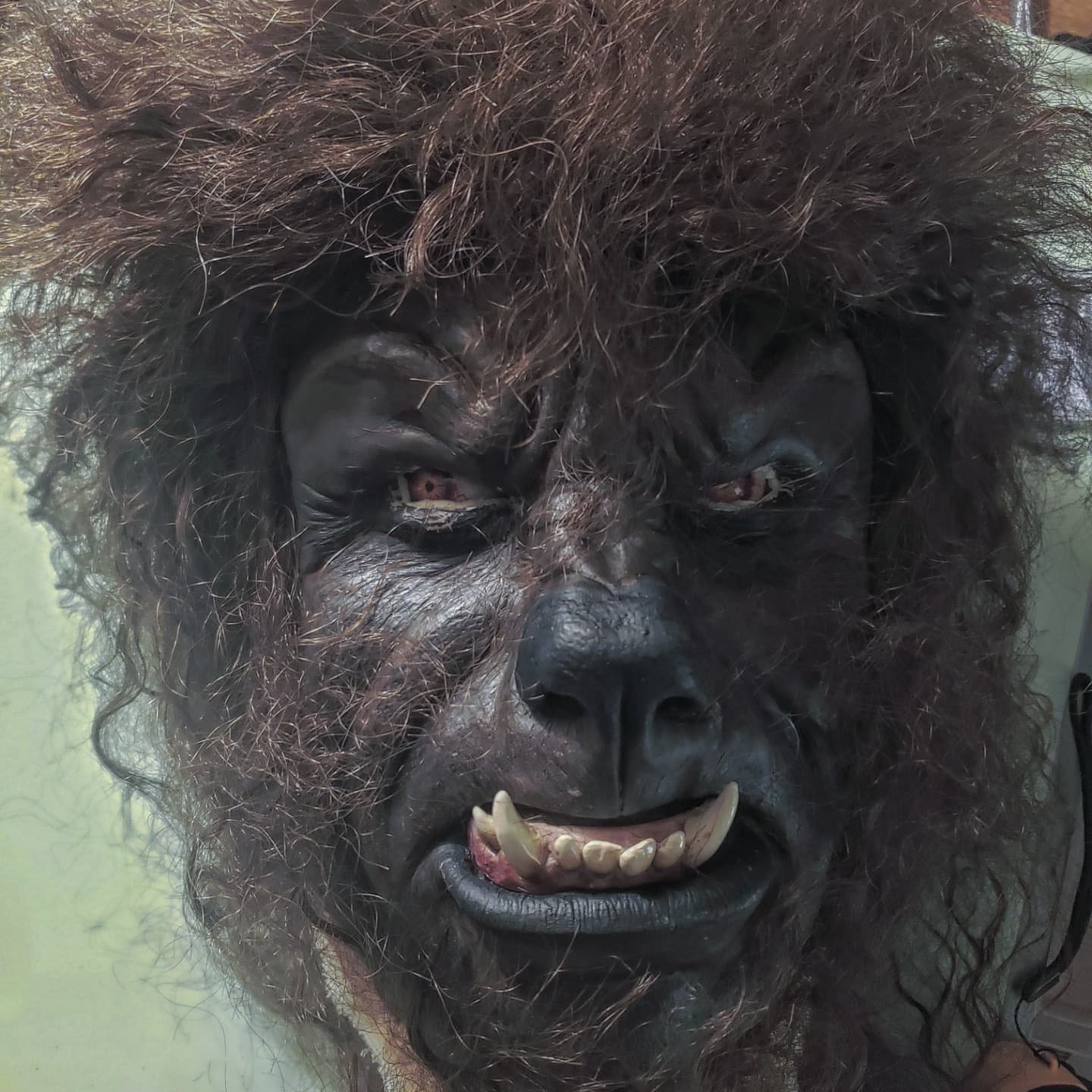